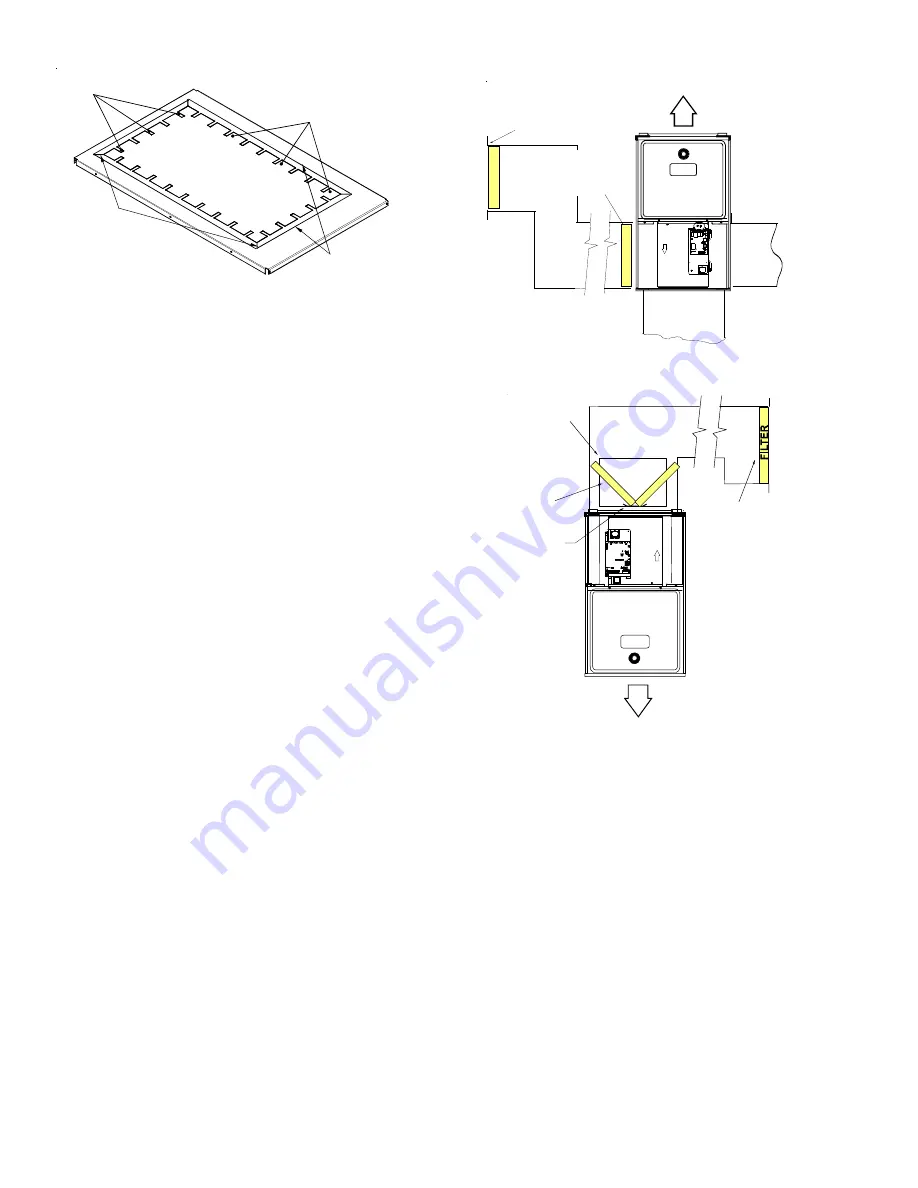
32
CUT FOUR CORNERS
AFTER REMOVING SHEET
METAL
CUT USING TIN SNIPS
PRESS OUT BY HAND
SCRIBE LINES OUTLINING
DUCT FLANGES
Duct Flange Cut Outs
When a cooling coil is installed with the furnace, it must be
installed in the supply air to avoid condensation from
occuring in the heat exchanger.
When the furnace is installed without a cooling coil, it is recom-
mended that a removable access panel be provided in the out-
let air duct. This opening shall be accessible when the furnace
is installed and shall be of such a size that the heat exchanger
can be viewed for visual light inspection or such that a sam-
pling probe can be inserted into the airstream. The access
panel must be made to prevent air leaks when the furnace is in
operation.
When the furnace is heating, the temperature of the return air
entering the furnace must be between 55°F and 100°F.
F
ILTERS
- R
EAD
T
HIS
S
ECTION
B
EFORE
I
NSTALLING
T
HE
R
ETURN
A
IR
D
UCT
WORK
Filters must be used with this furnace. Discuss filter mainte-
nance with the building owner. Filters do not ship with this
furnace, but must be provided, sized and installed externally by
the installer. Filters must comply with UL900 or CAN/ULCS111
standards. Damage or repairs due to the installation of the
furnace without filters is not covered under the warranty.
On upflow units, guide dimples locate the side return cutout
locations. Use a straight edge to scribe lines connecting the
dimples. Cut out the opening on these lines.
NOTE:
An under-
sized opening will cause reduced airflow.
FIL
T
E
R
AIR FLOW
CENTRAL
RETURN
GRILLE
FI
L
T
E
R
SIDE RETURN
EXTERNAL FILTER
RACK KIT
(EITHER SIDE)
Possible Upright Upflow
FI
LT
ER
AIR FLOW
CENTRAL
RETURN
GRILLE
RETURN
DUCT
FI
LT
E
R
FILTER
SUPPORT
BRACKET
(Field Supplied)
FILTER
ACCESS
DOOR
Possible Upright Counterflow
Filter Locations
Startup Procedure
Before placing any furnace into service for the first time or
after performing service on an existing furnace, the build-
ing gas piping system, building piping connection to the
furnace, and gas train inside the furnace cabinet must be
proven safe and leak free. Verifying a leak free status is
most thoroughly accomplished when a combination of ap-
proved methods is used, meter dial test, electronic gas leak
detector, liquid leak detector solution.
The furnace must have a 115 volt power supply properly
connected and grounded. Line and Neutral polarity must be
correct
OPERATION