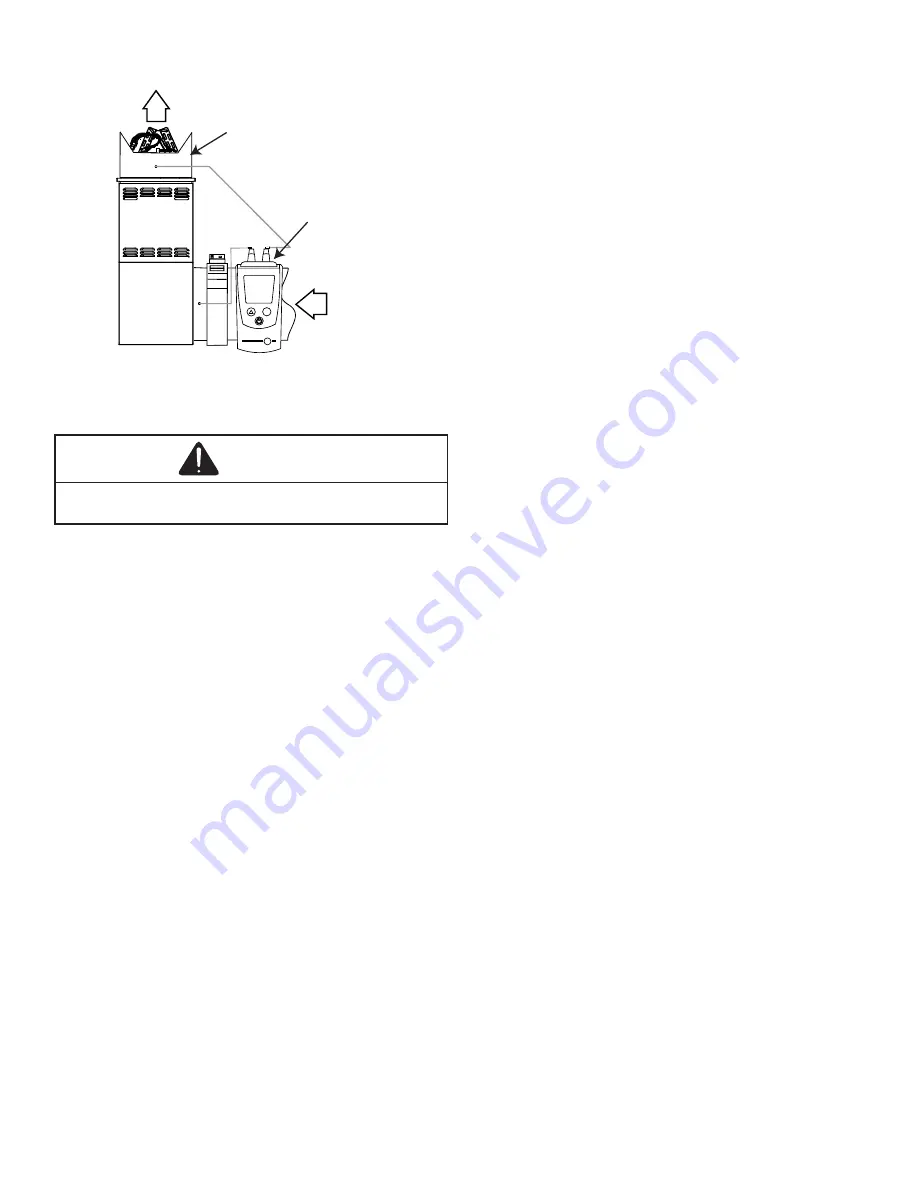
35
CUTAWAY OF DUCTWORK
TO EXPOSE COIL
DIGITAL
MANOMETER
RETURN
AIR
Mode
.
SUPPLY
AIR
Temperature Rise Measurement
Figure 42
Circulator Blower Speeds
WARNING
To avoid personal injury or death due to electrical shock,
turn OFF power to the furnace before changing speed taps.
This furnace is equipped with a multi-speed circulator
blower. This blower provides ease in adjusting blower
speeds. The Specification Sheet applicable to your model
provides an airflow table, showing the relationship between
airflow (CFM) and external static pressure (E.S.P.), for the
proper selection of heating and cooling speeds.
1.
Determine the tonnage of the cooling system installed
with the furnace. If the cooling capacity is in BTU/hr
divide it by 12,000 to convert capacity to tons.
Example:
Cooling Capacity of 30,000 BTU/hr.
30,000/12,000 = 2.5 Tons
2. Determine the proper air flow for the cooling system.
Most cooling systems are designed to work with air
volume between 350 and 450 CFM per ton. Most
manufacturers recommend an air flow of about 400
CFM per ton.
Example:
2.5 tons X 400 CFM per ton = 1000 CFM
3.
Select the heating speed for your model from the
heating speed chart in the Specification Sheet. The
selected speed must provide a temperature rise within
the rise range listed with the particular model.
To adjust the circulator blower speed, proceed as follows:
1. Turn OFF power to the furnace.
2. Select the heating and cooling blower speeds that
match the installation requirements from the airflow
table in the Specification Sheet.
3. Relocate desired motor leads to the circulator blower
heat and cool speed terminals on the integrated
control module. (Terminals are identified as HEAT and
COOL. If heating and cooling blower speeds are the
same, a jumper wire must be used between the heat
and cool terminals.
4. Connect all unused blower motor leads to the “PARK”
terminals on the integrated control module. Any leads
not connected to the “PARK” terminals must be taped.
5. Turn ON power to furnace.
6.
Verify proper temperature rise as outlined in the
Temperature Rise section of Startup Procedure and
Adjustment.
In general lower heating speeds will: reduce electrical
consumption, lower operating sound levels of the blower,
and increase the outlet air temperature delivered to the
home. The speeds available allow the blower performance
to be optimized for the particular homeowner’s needs.
Blower Heat Off Delay Timings
The integrated control board on 92% models has a fixed
blower off delay of 150 seconds.
NORMAL SEQUENCE OF OPERATION
Power Up
The normal power up sequence is as follows:
•
115 VAC power applied to furnace.
•
Integrated control module performs internal checks.
•
LED will flash once at power up then remain on.
• Integrated control module monitors safety circuits
continuously.
•
Furnace awaits call from thermostat.
Heating Mode
The normal operational sequence in heating mode is as
follows:
•
R and W thermostat contacts close, initiating a call for
heat.
• Integrated control module performs safety circuit
checks.
•
Induced draft blower is energized for a 15-second
prepurge.
•
Igniter warm up begins upon presence of closed
pressure switch contacts.
•
Gas valve opens at end of igniter warm up period,
delivering gas to burners and establishing flame.
•
Integrated control module monitors flame presence.
Gas valve will remain open only if flame is detected.
•
Circulator blower is energized on heat speed following
a thirty (30) second blower on delay.
•
Furnace runs, integrated control module monitors
safety circuits continuously.
•
R and W thermostat contacts open, completing the
call for heat.
•
Gas valve closes, extinguishing flame.
•
Induced draft blower is de-energized following a
fifteen second post purge.
•
For 92% Models: The blower off delay is 150 seconds
(non-adjustable).
•
Furnace awaits next call from thermostat.
Содержание DM92SS
Страница 45: ...45 THIS PAGE IS LEFT INTENTIONALLY BLANK...
Страница 46: ...46 THIS PAGE IS LEFT INTENTIONALLY BLANK...
Страница 47: ...47 THIS PAGE IS LEFT INTENTIONALLY BLANK...