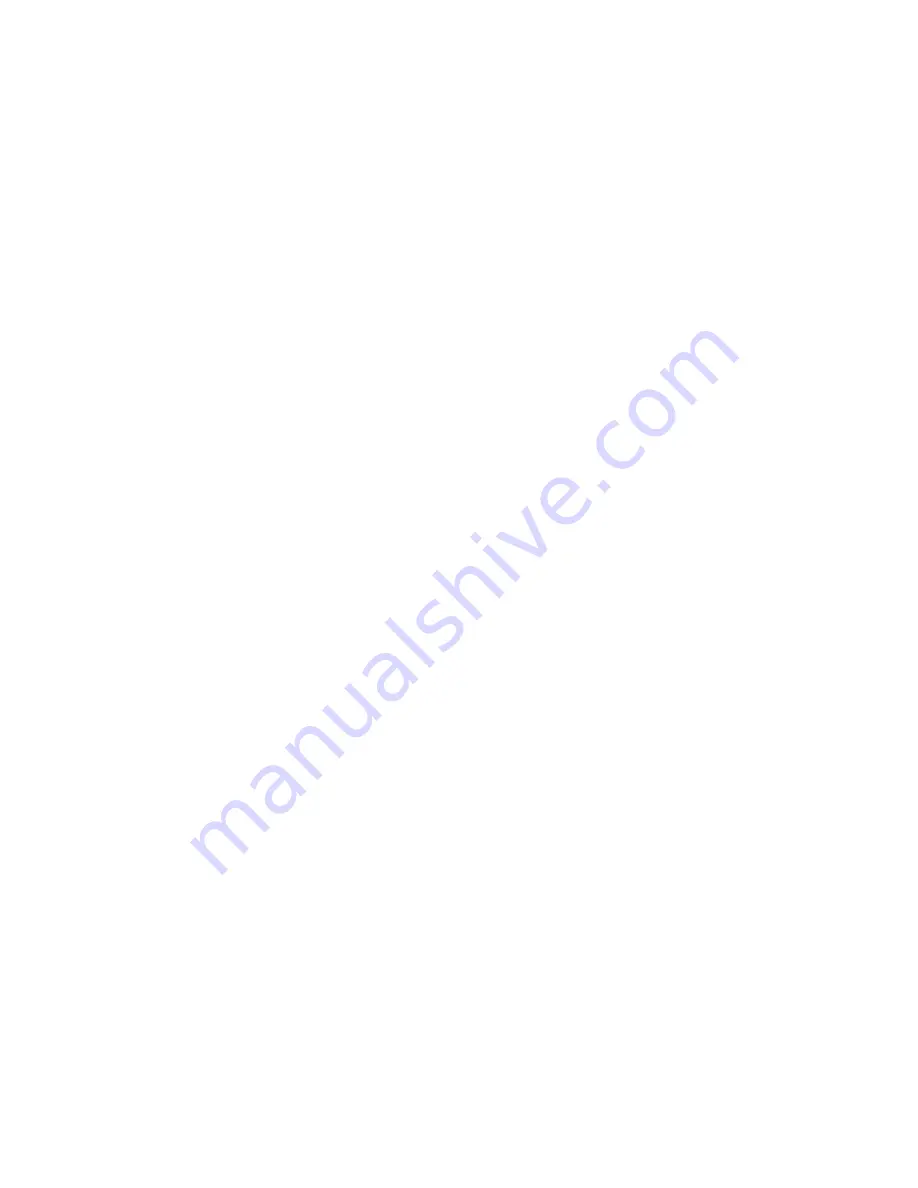
36
Respirator Performance Post Reprocessing
Inherent for the re-‐use of an N95 mask is the requirement to assure that the decontamination
process does not jeopardize the safety and health of the healthcare practitioner re-‐using the N95
mask. N95 respirators/masks are commonly made of nonwoven fabric consisting of three composite
layers: outer-‐layer consisting of spunbond polypropylene; mid-‐layer consisting of meltblown
polypropylene; and an inner-‐layer consisting of spunbond polypropylene). Some N95 respirators
also incorporate an additional layer of cellulose/polyester nonwoven, the outer active layer coated
with a hydrophilic plastic laminated to a second inner layer treated with copper and zinc ions. This
additional dual layer is designed to inactivate influenza viruses using deferent mechanisms of action.
The polypropylene, polyester, and cellulose components all are compatible with the HVHA process
employed in the RH-‐N95, including the retention of the electrostatic charge in the polyethylene
layers (Tsai). Typically, the other mask components of N95 masks are also thermally compatible
with the lower temperatures associated with the HVHA process: (e.g., straps composed of
thermoplastic elastomers; nose clip made from aluminum; nose foam derived from polyurethane;
and thermally resistant adhesives).
Specification performance of the mask’s integrity, composition, filtration and breathability are
physical parameters that require analysis after the mask has been re-‐processed. All visible
indications from testing conducted by CPAC demonstrate that the decontamination process does not
alter the masks after twenty 30-‐minute re-‐processing cycles, the limit of the number of cycles
conducted to date. Observations are consistent with a report from Stanford University which
reported that after the N95 filtration fabric was dry heat treated at 75°C for 30 minutes after 20
cycles there was no change in filtration efficacy or pressure drop. Whole mask studies after 20 cycles
at this time and temperature also showed no deformations in the mask or changes in elasticity of
face/ear straps (Liao).
This work has been further supported by work conducted by the Lawrence Livermore National
Laboratory (Massey et al.) in which dry heat studies at ambient humidity, 75°C for 30 minutes to
discern differences in face fit before and after re-‐processing. Using quantitative fit tests prescribed
by OSHA under protocol 1910.134, Appendix A, no differences were seen for 3M Model 8210
respirators for up to 10 re-‐processing conditions, all respirators achieving a maximum score of 200+
for the four trials conducted.
Comparison of the RH-‐N95 HVHA Process to Other Mask Reprocessing Alternatives
The high-‐velocity hot air process eliminates issues otherwise found in other thermal, chemical, or UV
decontamination methods. Treatment mechanisms that introduce liquids to the mask run the high
risk of severely lowering the mask’s filtration and breathability performance (Liao). This is
especially true of water or water vapor that destroys the electrostatic nature of the mask’s filtration
fabric which gives it the ability to meet its stated performance level. This would include steam
sterilization and any liquid disinfection method. Chemical liquid/gas phase disinfection/sterilization
technologies also introduce issues with:
•
Incompatibilities of mask materials with the disinfectant/sterilant (includes electrostatic
performance, band elasticity; adhesive performance, and metal reactions);
•
Providing uniform concentration of the introduced (and maintenance) of required
disinfectant/sterilant concentration;
•
Providing uniform mask penetration;
•
Mask wetness and required drying times;
•
Mask fiber matting and required filtration and breathability performance;