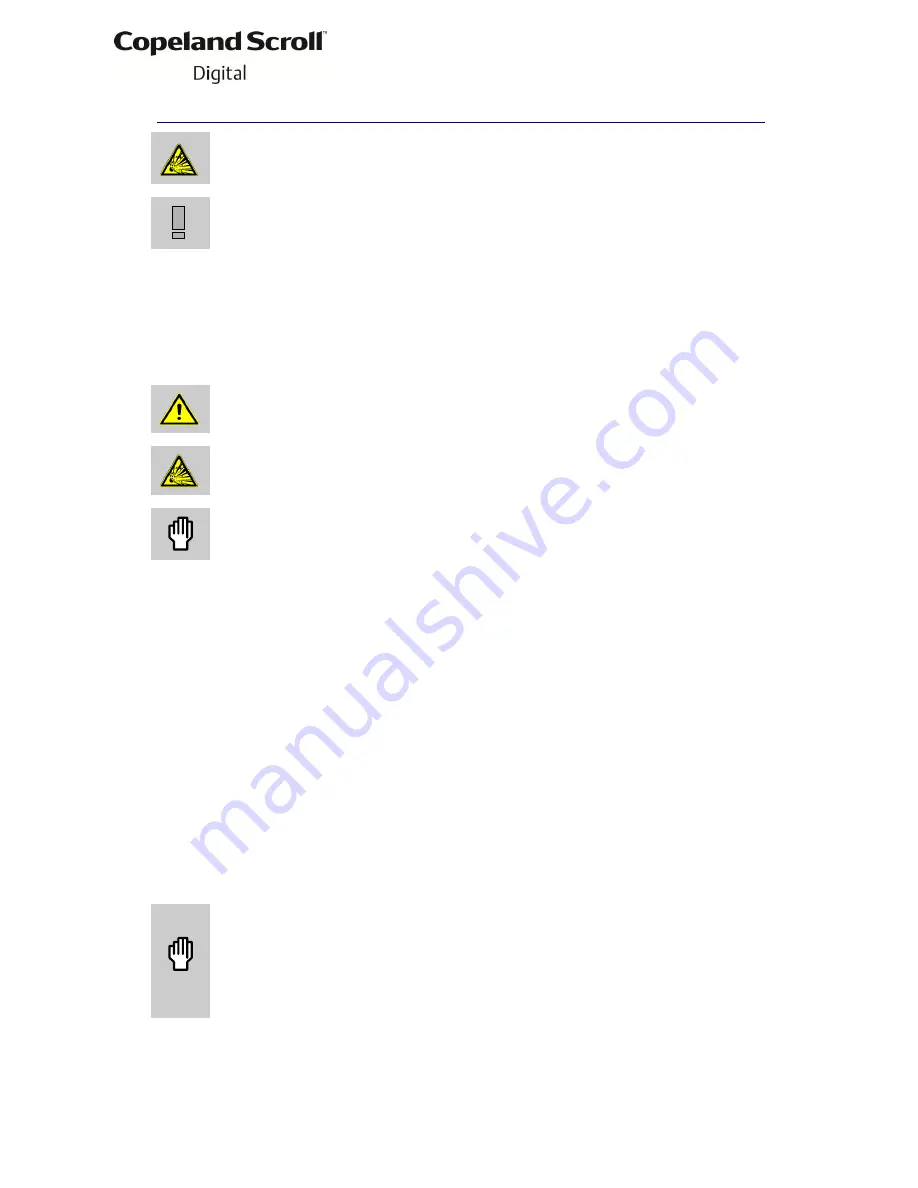
24
C6.2.15/0815/E
5
Starting up & operation
WARNING
Diesel effect!
Compressor destruction!
The mixture of air and oil at high
temperature can lead to an explosion. Avoid operating with air.
IMPORTANT
Oil dilution! Bearing malfunction!
Turn the crankcase heater on 12 hours
before starting the compressor.
5.1 Strength pressure test
The compressor has been strength-tested in the factory. It is not necessary for the customer to
strength- or leak-test the compressor again although the compressor will normally be exposed to
the testing made as part of system testing.
5.2 Tightness/pressure test
WARNING
High pressure! Personal injuries!
Consider personal safety requirements
and refer to test pressures prior to test.
WARNING
System explosion! Personal injuries!
DO NOT USE other industrial
gases.
CAUTION
System contamination! Bearing malfunction!
Use only dry nitrogen or
dried air for pressure testing.
If using dry air do not include the compressor in the pressure test
– isolate it first. Never add
refrigerant to the test gas (as leak indicator).
5.3 Preliminary checks
– Pre-starting
Discuss details of the installation with the installer. If possible, obtain drawings, wiring diagrams,
etc.
It is ideal to use a check-list but always check the following:
Visual check of the electrics, wiring, fuses etc.
Visual check of the plant for leaks, loose fittings such as TXV bulbs etc.
Compressor oil level
Calibration of HP & LP switches and any pressure actuated valves
Check setting and operation of all safety features and protection devices
All valves in the correct running position
Pressure and compound gauges fitted
Correctly charged with refrigerant
Compressor electrical isolator location & position
5.4 Charging procedure
CAUTION
Low suction pressure operation! Compressor damage!
Do not operate
with a restricted suction. Do not operate with the low-pressure cut-out
bridged. Do not operate compressor without enough system charge to
maintain at least 0.5 bar(g) suction pressure. Allowing pressure to drop
below 0.5 bar(g) for more than a few seconds may overheat scrolls and
cause early drive bearing damage.
The system should be liquid-charged through the liquid-receiver shut-off valve or through a valve
in the liquid line. The use of a filter drier in the charging line is highly recommended.
Because
R410A and R407C are blends and scrolls have discharge check valves, systems should be
liquid-charged on both the high and low sides simultaneously to ensure a positive refrigerant