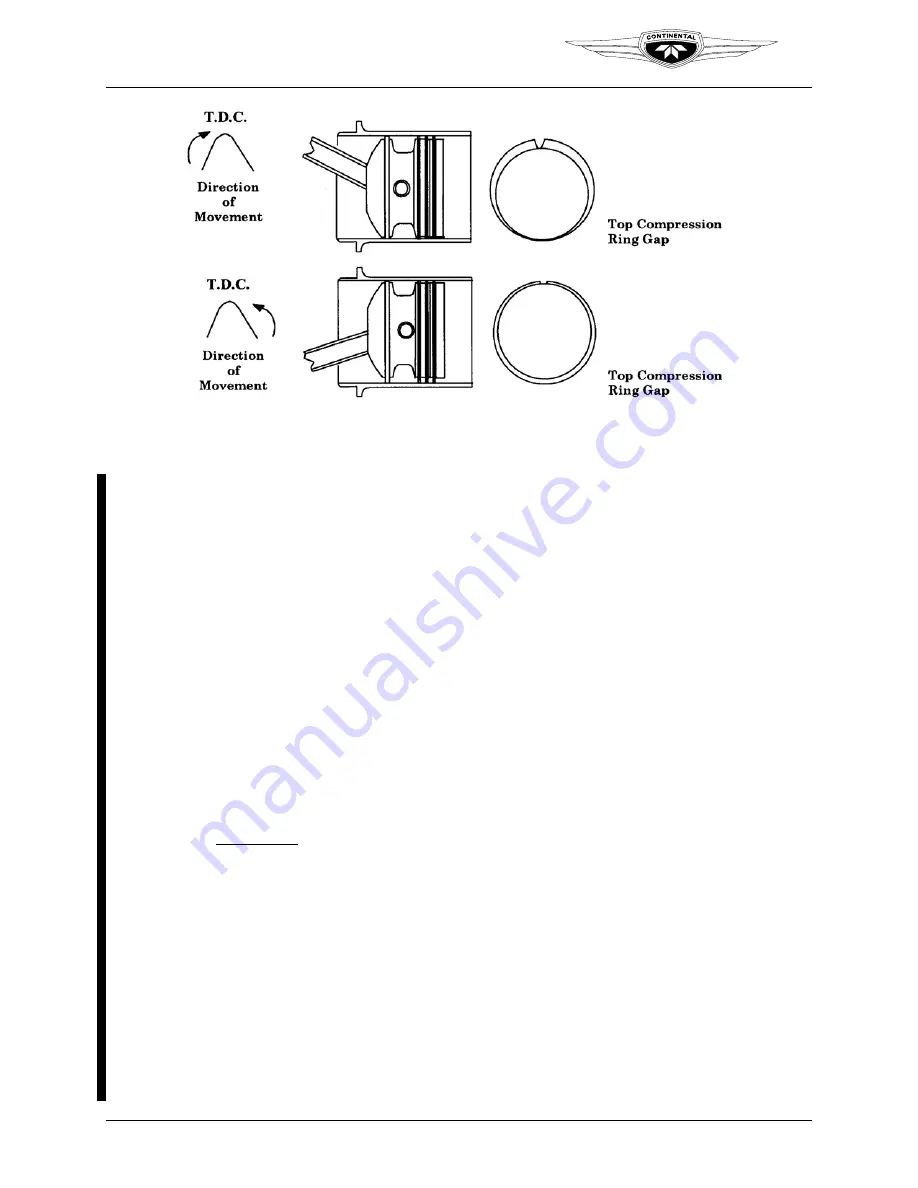
Maintenance Inspections
Teledyne Continental Motors, Inc.
TM
Figure 7-7.
Piston Ring Positions
7-24
IOF-240 Series Engine Maintenance Manual
4.
To check the static seals (Figure 7-6) while the cylinder is still installed:
a.
For each cylinder under test, position the piston as close to bottom dead center as
possible on the compression stroke, ensuring the intake and exhaust valves remain
closed to allow the cylinder to hold pressure.
b.
Saturate the cylinder with a soapy water solution. If bubbling appears during the
inspection, the static seal is leaking; replace the cylinder. Repeat soapy water
application, as required, to complete a thorough inspection of each cylinder.
Slowly increase the pressure in the cylinder to 80 psi. Inspect the following for
evidence of leakage:
1)
Cylinder head to barrel seal
2)
Spark plug port seal
3)
Intake and exhaust ports
c.
Reduce pressure to 0 psi. Repeat steps a and b for each cylinder. Record the
results on Table 7-10, the “Cylinder Inspection Checklist.”
d.
No leakage is allowed in the static seals. If leakage is noted between the cylinder
head and barrel, replace the cylinder according to instructions in Chapter 10.
e.
Refer to the “Summary of Seal Checks and Corrective Actions” (Table 7-4) for
corrective action:
1)
If the cylinder pressure gauge reading now is
higher
than the previously
determined minimum acceptable cylinder pressure leakage limit, record
Differential Pressure Test result as passing.
2)
If no leakage was detected and the cylinder pressure gauge reading remains
lower
than the previously determined minimum acceptable cylinder pressure
leakage limit, perform a “Cylinder Borescope Inspection” according to
instructions in Section 7-3.7.3 prior to performing any invasive inspections.
Change 1
31 August 2007