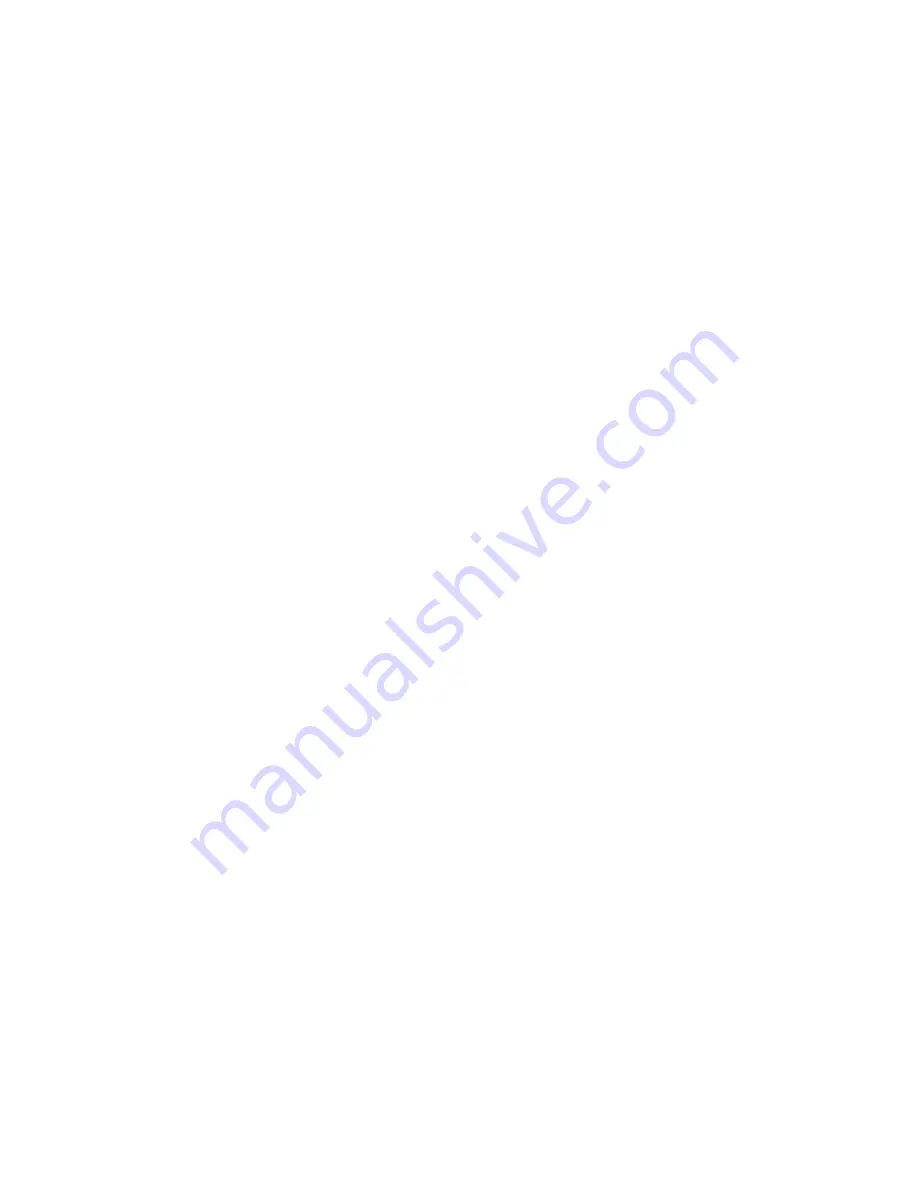
detected during the weld cycle. When the Cycle On input (INP2) is cleared the
“No Fault”
(CR2) output will be asserted if the AAD testing passed the
established limits. The
“No Fault”
(CR2) output will always be cleared when a
weld is detected. The Third output CR3 provides a
“Fault”
output. This out will
be asserted when a fault has occurred during the active weld cycle. When the
Cycle On input (INP2) is cleared the
“Fault”
(CR3) output will be asserted if the
AAD testing failed the established limits. The
“Fault”
(CR3) output will always be
cleared when a weld is detected. At the end of every weld and/or Part the
“No
Fault”
CR2 or
“Fault”
CR3 output will be asserted.
6.2 OPERATIONAL
DESCRIPTION
The normal operation of the Micro ADM™ requires a user provide
“INP2-New
Part”
signal that must be asserted at the beginning of the part weld sequence.
This input must be held during the complete part weld cycle. The Micro ADM™
will count and test each weld as the part is welded. Each weld will then be
verified based on AAD process algorithms. If the optional
“Part B”
input is used
the input must be reset prior to asserting the
“INP 2 - New Part”
signal and must
be asserted at the end of the Part A weld cycle.
At the end of each weld the previous test status will be asserted by the
“CR2-NO
Fault”
or
“CR3-Fault”
outputs. One of the two outputs will be set at the end of the
weld. If a fault occurs during the weld cycle then the
“CR3-Fault”
output will be
set at the first occurrence of the fault. The Status outputs CR2 and CR3 will be
cleared when the next weld is detected.
The Micro ADM™ will count each valid weld and will internally load new Process
limits for each weld event. The
“INP2-New Part”
signal is used to synchronize
the weld counts. A min arc time for a valid weld is used to verify valid completion
of a specific weld event. At the end of each weld event the Micro ADM™ will
summarize and store the results of the previous weld to include average Volt,
Amp, Wire Speed, Arc Time and Weld Number.
When the
“Part B”
is asserted or the
“INP2–New Part”
input is cleared the Micro
ADM™ will calculate the total wire volume, work applied, spot heat and total
number of welds on part. The result of the previous part data will be verified to
the part control limits and the Part Status will be asserted on the Status outputs
“CR2–No Fault”
or
“CR3–Fault”
. The status condition will remain until the next
“INP2–New Part”
input is asserted.
20
Содержание Micro ADM
Страница 2: ......
Страница 35: ...A 8 NetHub Mounting Dimensions 31...
Страница 42: ...Appendix B Micro ADM Assembly Parts List B 1 Micro ADM Sensor Assembly P N A3A0226 Rev 0 38...
Страница 43: ...39...
Страница 45: ...B 2 Micro ADM Sensor Assembly P N A3A0226 Rev A 41...
Страница 46: ...42...
Страница 48: ...B 3 Micro ADM Sensor Assembly P N A3A0226 Rev B 44...
Страница 49: ...45...
Страница 51: ...B 4 Micro ADM Sensor Assembly P N A3A0226 Rev C 47...
Страница 52: ...48...