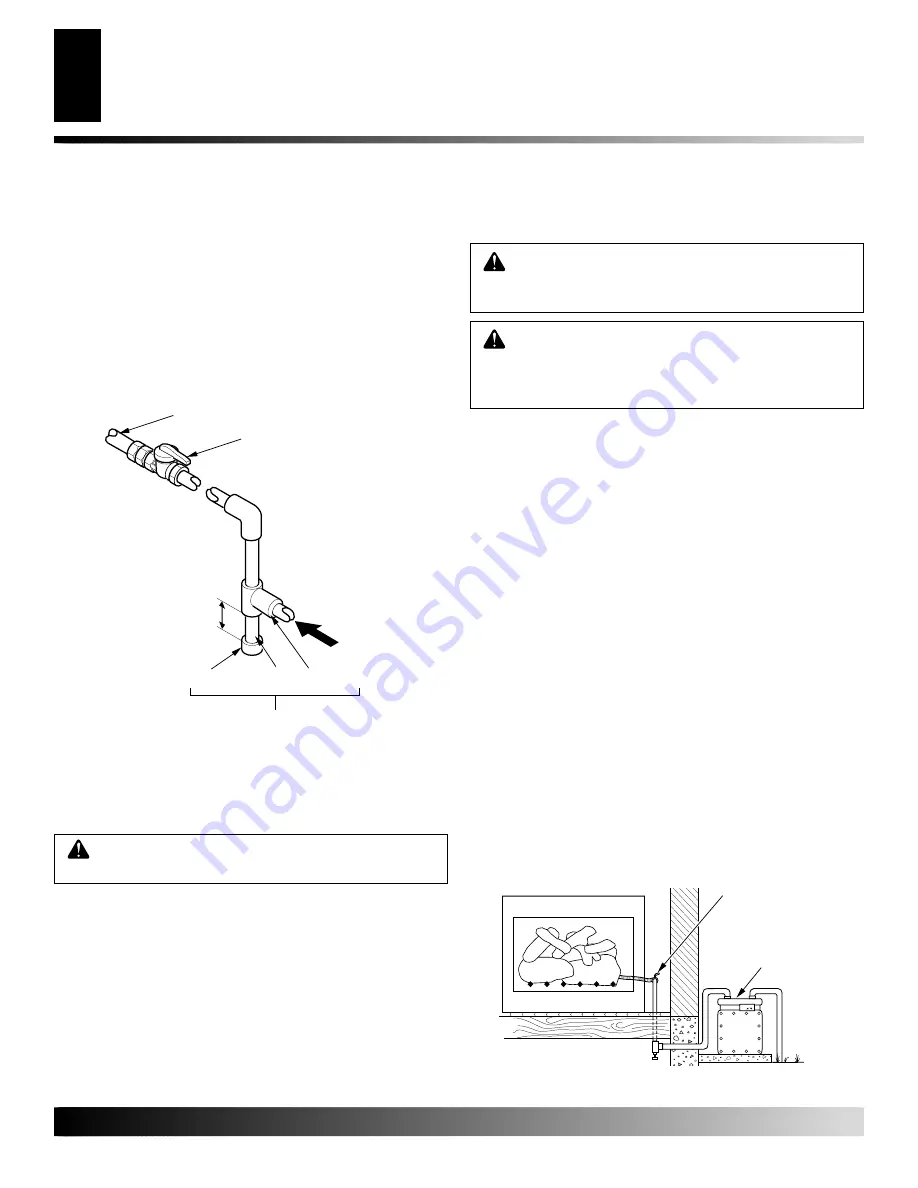
901915-01B
For more information, visit www.desatech.com
For more information, visit www.desatech.com
6
Figure 5 - Checking Gas Joints
INSTALLATION
Continued
WARNING: Test all gas piping and connections,
internal and external to unit, for leaks after installing
or servicing. Correct all leaks at once.
WARNING: Never use an open flame to check for
a leak. Apply a noncorrosive leak detection fluid to
all joints. Bubbles forming show a leak. Correct all
leaks at once.
CHECKING GAS CONNECTIONS
Pressure Testing Gas Supply Piping System
Test Pressures In Excess Of 1/2 PSIG (3.5 kPa)
1.
Disconnect appliance with its appliance main gas valve (control
valve) and equipment shutoff valve from gas supply piping sys-
tem. Pressures in excess of 1/2 psig will damage heater regulator.
2.
Cap off open end of gas pipe where equipment shutoff valve
was connected.
3.
Pressurize supply piping system by either using compressed air or
opening main gas valve located on or near gas meter.
4.
Check all joints of gas supply piping system. Apply noncor-
rosive leak detection fluid to gas joints. Bubbles forming show
a leak.
5.
Correct all leaks at once.
6.
Reconnect log set and equipment shutoff valve to gas supply.
Check reconnected fittings for leaks.
Test Pressures Equal To or Less Than 1/2 PSIG (3.5 kPa)
1.
Close equipment shutoff valve (see Figure 5).
2.
Pressurize supply piping system by either using compressed air or
opening main gas valve located on or near gas meter.
3.
Check all joints from gas meter to equipment shutoff valve (see
Figure 5). Apply noncorrosive leak detection fluid to gas joints.
Bubbles forming show a leak.
4.
Correct all leaks at once.
We recommend that you install a sediment trap in supply line as
shown in Figure 4. Locate sediment trap where it is within reach for
cleaning. Install in piping system between fuel supply and heater.
Locate sediment trap where trapped matter is not likely to freeze. A
sediment trap traps moisture and contaminants. This keeps them
from going into log set controls. If sediment trap is not installed or
is installed wrong, log set may not run properly.
Installation must include an equipment shutoff valve, union, and
plugged 1/8" NPT tap. Locate NPT tap within reach for test gauge
hook up. NPT tap must be upstream from log set (see Figure 4).
IMPORTANT:
Install equipment shutoff valve in an accessible
location. The equipment shutoff valve is for turning on or shutting
off the gas to the appliance.
Apply pipe joint sealant lightly to male threads. This will prevent
excess sealant from going into pipe. Excess sealant in pipe could
result in a clogged burner injector.
WARNING: Use pipe joint sealant that is resistant
to liquid petroleum (LP) gas.
Figure 4 - Gas Connection
* Purchase the optional CSA design-certified equipment shutoff
valve from your dealer. See Accessories, page 17.
** Minimum inlet pressure for purpose of input adjustment.
3" Minimum
Sediment Trap
From Gas Meter
(5" W.C.** to 10.5"
W.C. Pressure)
CSA Design-Certified
Equipment Shutoff Valve
With 1/8" NPT Tap*
Approved
Gas Hose
Tee Joint
Pipe Nipple
Cap
Gas Meter
Equipment Shutoff Valve
INSTALLATION
Connecting To Gas Supply (Cont)
Checking Gas Connections