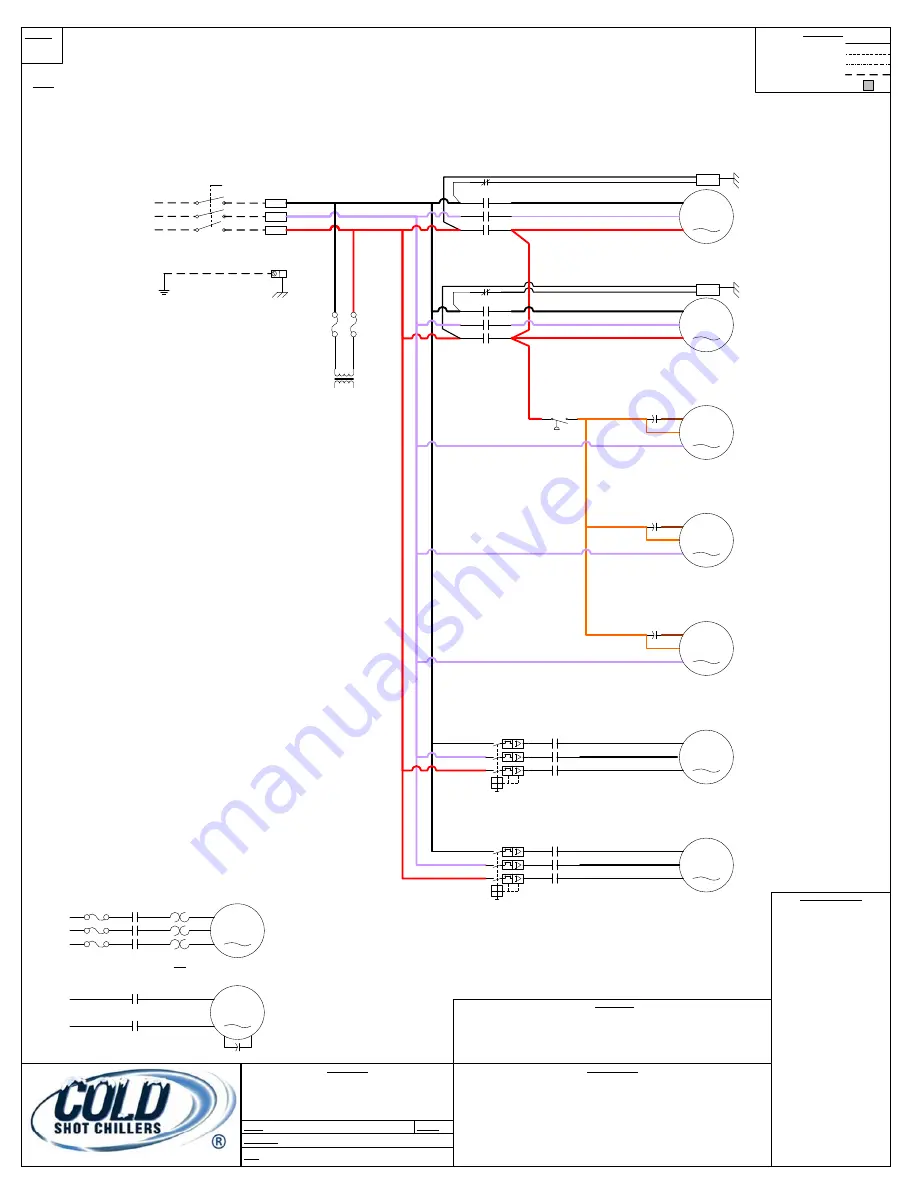
GENERAL NOTES
1. WARNING-For continued protection against fire hazard replace fuses with the same type and rating only.
2. Unit must be permanently grounded and conform to N.E.C. & local codes.
3. Use copper conductors for field-wiring. Class 1, unless noted. All wire based on 105°C insulation wire, minimum.
4. Wire colors shown may differ from actual unit.
5. Drawing line item reference identification:
- Number in parenthesis near output is location of controlled items.
- First number is sheet #, second & third are line#
- No underline indicates normally open (NO) contact
- Underline indicates normally closed (NC) contact
6. Design, specifications, and components are subject to change without notice.
7. All intellectual property, including designs and programming logic are the property of Cold Shot Chillers and is not
to be copied or used without permission from Cold Shot Chillers.
COMPONENT CODES
AUX
Auxiliary (contact block)
BZR
Buzzer
CC1
Compressor Contactor 1
CC2
Compressor Contactor 2
CCH
Crank Case Heater
COM
Common
CR
Control Relay
CR1
Control Relay for Cooling Mode Status
CR2
Control Relay for Active Cooling On
CR3
CR for Chiller Pump functions
CR4
CR for Process Pump functions
CR5
CR for Remote ON/OFF Operation
DB
Distribution Block
FPS
Fan-Cycling Pressure Switch
F1/F2
Fuse 1 and 2 (Transformer Primary)
F3
Fuse 3 (120VAC Control Voltage)
F4
Fuse 4 (24VAC Control Voltage)
FST
Flow Safety T-Stat
FZT
Freeze Safety T-Stat
GND
Ground
HG
Hot Gas
HPS
High Pressure Switch
L
Line
LAR
Low Ambient Relay
LAT
Low Ambient Thermostat
LFS
Liquid Flow Switch
LPS
Low Pressure Switch
LT1
Light 1 for Cooling Status – OK
LT2
Light 2 for Cooling Fault Condition
M
Motor
MS
Motor Starter
NC
Normally Closed
NO
Normally Open
PC1
Pump Contactor 1 (Chiller Pump)
PC2
Pump Contactor 2 (Process Pump)
PLC
Programmable Logic Controller
PS
Power Supply
RC
Run Capacitor
SW1
Selector Switch (Pump/Off/Cooling)
SW2
Selector Switch (Process Pump)
SW3
Local/Remote Switch
TB1
Terminal Block 1 (for Internal)
TB2
Terminal Block 2 (for External)
TC
Thermocouple
TLH
Tank Level Switch – High
TLL
Tank Level Switch – Low
TLM
Tank Level Switch – Mid
TRAN
Transformer
EDIT DATE:
August 26, 2015
DESCRIPTION
ELECTRICAL DRAWING: Series A – Level 1 Delta Controls
Typical design for One and Two Compressor systems.
Using standard 24VDC on/off inputs. 24VAC controls outputs.
Options and typical variations shown or noted.
FILE:
DWG_Electrical-DeltaControl-SeriesA120_081915.vsd
PAGE#:
1
01
02
03
04
05
06
07
08
09
10
11
12
13
14
15
16
SHEET:
1
PAGE:
A120-PowerCircuit(3phase)
LINE#
17
18
LINE LEGEND
FACTORY SUPPLIED/INSTALLED
DETAILS
FACTORY OPTION
FIELD SUPPLIED/INSTALLED
TERMINAL BLOCK CONTACT #
#
GROUNDING
LUG
CHASSIS
GND
GND
M
Pump #2 (Process Pump)
(OPTION)
PC2
M
Pump #1 (Chiller Pump)
PC1
M
Compressor #2
(Tandem Compressor Systems)
CC2
CCH
CC2-Aux
M
Compressor #1
CC1
CCH
CC1-Aux
MAIN POWER
3PHASE
L1
L2
L3
MAIN
DISCONNECT
L1
L2
L3
DB-Line
RC3
M
Fan #3
(180&240models)
(See Page Note #3)
RC2
M
Fan #2
(See Page Note #3)
FPS
RC1
M
Fan #1
(See Page Note #3)
MS1
( 212 )
MS2
( 207 )
Field Supplied/Installed
* PAGE NOTES
1. Control transformers must be wired/tapped for the appropriate incoming voltage. Depending on design, one dual
voltage or two independent voltages.
2. Models -24 to -90 models have 1 fan, -120 and -150 models have 2 fans. -180 and -240 models have 3 fans.
3. Fan speed controller will be installed on #2 fan on 120 to 150 models and installed on #3 on 180 and 240 models.
4. Fuse block, contactor, and overload may be used in place of motor starter and contactor combination.
5. Single phase pump motors may be used. Motors must be internally, thermally protected.
To CONTROL
CIRCUIT
( See 201 )
TRAN1
(PageNote 1,2)
F2
F1
M
Single Phase Pump Motor
(Example)
PC#
See PAGE NOTE #5
M
Three Phase Pump Motor
(Example)
PC#-OL
( ### )
PC#
FB
See PAGE NOTE #4
Содержание ACWC-180-EM-DR-LT-0-5
Страница 35: ...Notes...
Страница 36: ...MAINTENANCE RECORD DATE PROCEDURE PERFORMED...