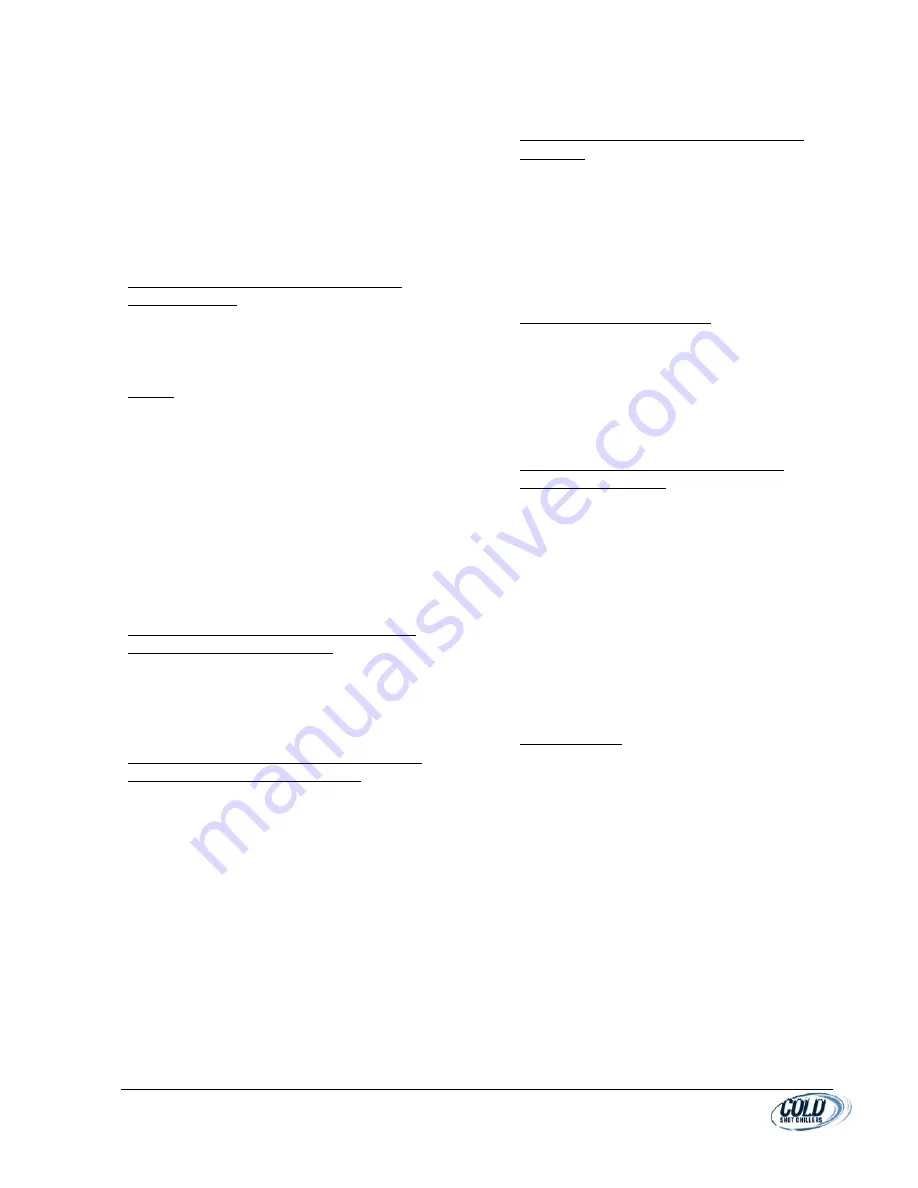
process, use a wrench to hold the strainer
stationary while another wrench is placed on
the strainer screen cap. The wrench on the
strainer body must prevent the body from
turning in the piping. Remove the cap and the
strainer screen. Clean the screen and
reinsert, taking care not to damage by
crushing. Tighten the screen cap.
c.
Setup a schedule based on the systems
cleanliness and trends of use.
7.
FLUID SYSTEM CONNECTIONS (INSPECT FOR
LEAKS OR LOOSE)
a.
Visually check for fluid leaks throughout
system. Physically check for loose pipe
fittings or hoses. Ensure that no plumbing
parts are wearing, cracking, or chaffing.
8.
PUMPS
a.
Check the pumps for leakage. Visual
indication of leakage from the pump end at
the pump connection to the motor is usually
an indication of a seal or O-ring failure. Only
action is to replace the seal with a new seal.
Seals are a consumable item.
b.
O-Rings may harden with age and may need
to be replaced when they leak.
c.
Close-coupled centrifugal pumps have no
bearings. Bearings in the motors are
permanently grease lubricated and cannot be
re-greased, unless indicated on motor.
9.
MOTOR LOADS (COMPRESSOR, PUMPS, FANS,
ETC...) CHECK AMPS/OPERATION
a.
Use an amp-meter to check for proper current
draws on all motors and heaters. Refer to the
chiller’s electrical schematics or the motor
nameplate for proper amp draws. Log
readings.
10.
ELECTRICAL CONNECTIONS (CHECK ALL WIRING
FOR LOOSE, CHAFFING, OR DAMAGE)
a.
Disconnect power to the chiller. Check the
electrical box and all junction boxes for any
loose or damaged wiring. Replace any wiring
that could cause problems with shorting or
unintentional grounds.
b.
Check the condition of the contactor points
for the compressor and pump. Replace them
if the edges become jagged or splattered to
avoid premature compressor and/or pump
failure. Contactor points are consumable and
their life is dependent on the amount of use
and power characteristics at the unit.
11.
REFRIGERATION SYSTEM FOR LEAKS (INSPECT
AND TEST)
a.
If the system is operating and there is no
indication of leaks, avoid accessing the system
unless necessary.
b.
Have a certified refrigeration technician check
the refrigeration system for proper operation.
c.
Leak check the unit, monitor operating
pressures, and adjust as needed. Refer to
manual for proper charging instructions.
12.
CASTER WHEELS AND SWIVELS
a.
Wheels may require frequent lubrication
based on the amount of use. Use good quality
bearing grease and pump it into the grease
fittings on the axle and swivel.
b.
If casters have locks, ensure that they are
locked prior to connecting to fluid and
electrical systems.
13.
COMPARE TEMPERATURE READOUT WITH
ACTUAL TEMPERATURE
a.
Use an independent thermometer (or
multiple for averaging) and compare to the
actual digital temperature display. If the
temperature varies more than a few degrees,
check condition of thermocouple/sensor.
Variation more than a few degrees is usually
not common.
b.
If the temperature controller is located in a
different location than the
thermocouple/sensor, then it may be
necessary to adjust the offset in the controller
parameters. Contact Cold Shot Chillers for
assistance.
14.
WINTERIZATION
a.
During cold operation months, the chiller
piping exposed to freezing temperatures
should be protected or damage will result. If
the system is not needed during winter
months, a possible option is to drain the
system of all fluid and tag the system for non-
use until needed again.
b.
All fluid must be removed from all
components and piping to prevent possible
damage.
c.
Follow the startup instructions in the manual
for refilling and startup.
MNL_Standard-Basic_ACWC-24to240-E-(IN PROGRESS)_(0815).docx
- 14 -
Содержание ACWC-180-EM-DR-LT-0-5
Страница 35: ...Notes...
Страница 36: ...MAINTENANCE RECORD DATE PROCEDURE PERFORMED...