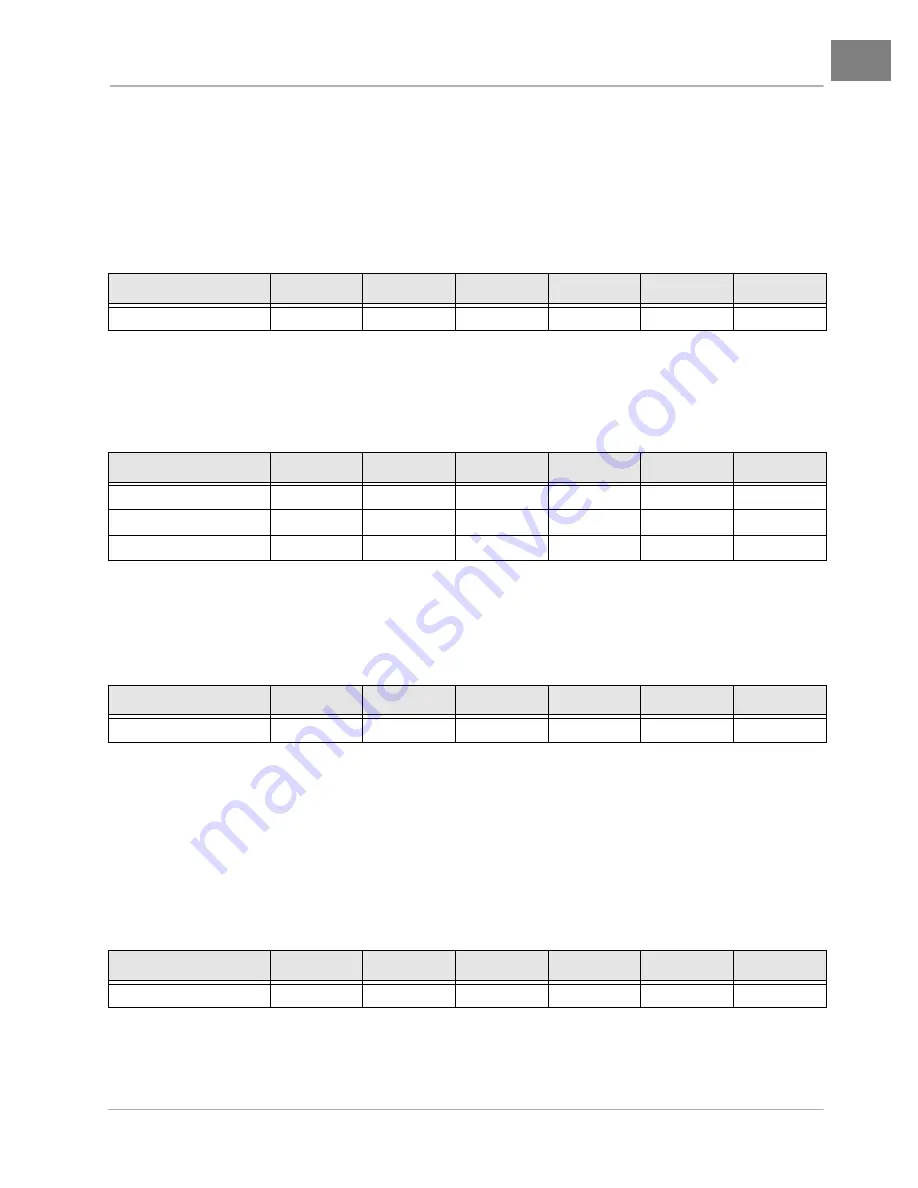
BATTERIES
Battery Testing
2004 V-Glide 36-Volt Electric Vehicle Maintenance and Service Supplement
Page 13-13
13
BATTERY TROUBLESHOOTING EXAMPLES
The following information represents a few examples of troubleshooting battery problems.
Example 1
Vehicle no. 68 was suspected of having a bad battery due to its performance. As a result, the battery charger
test was performed. After a full charge, the battery charger ammeter read 8.0 amps. Next, the on-charge volt-
age test was performed and the following results were recorded:
*Battery no. 3 appears suspect. Battery nos. 1 and 4 are also suspect. Next, a hydrometer test should be con-
ducted on all batteries.
Hydrometer test results:
*After the hydrometer test, it appears that battery no. 1 is the problem. Next, the discharge test was per-
formed.
Discharge test results:
*After a discharge test which lasted 45 minutes, battery no. 1 is clearly shown to be the problem. Battery no.
4 should be watched a little more closely but appears to be okay. Battery no. 1 should be replaced with a bat-
tery that has about the same age and usage as the other batteries in the set.
Example 2
Vehicle no. 70 was also suspected of having a bad battery due to its performance. The battery charger test
showed 7.0 amps after a full charge. After confirming there were no problems with the electrical system,
charger or brakes, the on-charge voltage was recorded as follows:
*Battery no. 2 was immediately suspected as the problem. After checking battery no. 2 with a hydrometer, it
was discovered that the negative (–) post cell was completely dead. Battery no. 2 should be replaced with a
battery that has the same age and usage as the other batteries in the set.
BATTERY NO.
1
2
3
4
5
6
On-Charge Voltage
7.61 V
7.95 V
7.36* V
7.62 V
7.92 V
7.96 V
BATTERY NO.
1
2
3
4
5
6
Positive Post Cell
1.200*
1.265
1.300
1.250
1.280
1.260
Center Cell
1.285
1.275
1.290
1.270
1.295
1.265
Negative Post Cell
1.265
1.270
1.285
1.265
1.275
1.275
BATTERY NO.
1
2
3
4
5
6
Discharge Voltage
4.08 V
5.50 V
5.80 V
5.36 V
5.57 V
5.56 V
BATTERY NO.
1
2
3
4
5
6
On-charge Voltage
7.86 V
7.33 V
7.90 V
7.93 V
7.91 V
7.75 V
Содержание V-GLIDE
Страница 2: ......
Страница 8: ......
Страница 30: ...11 ...
Страница 48: ...12 ...
Страница 64: ...14 ...
Страница 90: ...16A ...
Страница 104: ...16B ...
Страница 108: ......
Страница 109: ...2004 V Glide 36 Volt Electric Vehicle Maintenance and Service Supplement ...
Страница 110: ......
Страница 111: ......
Страница 112: ...Golf Cars and Utility Vehicles Club Car Inc P O Box 204658 Augusta GA 30917 4658 ...