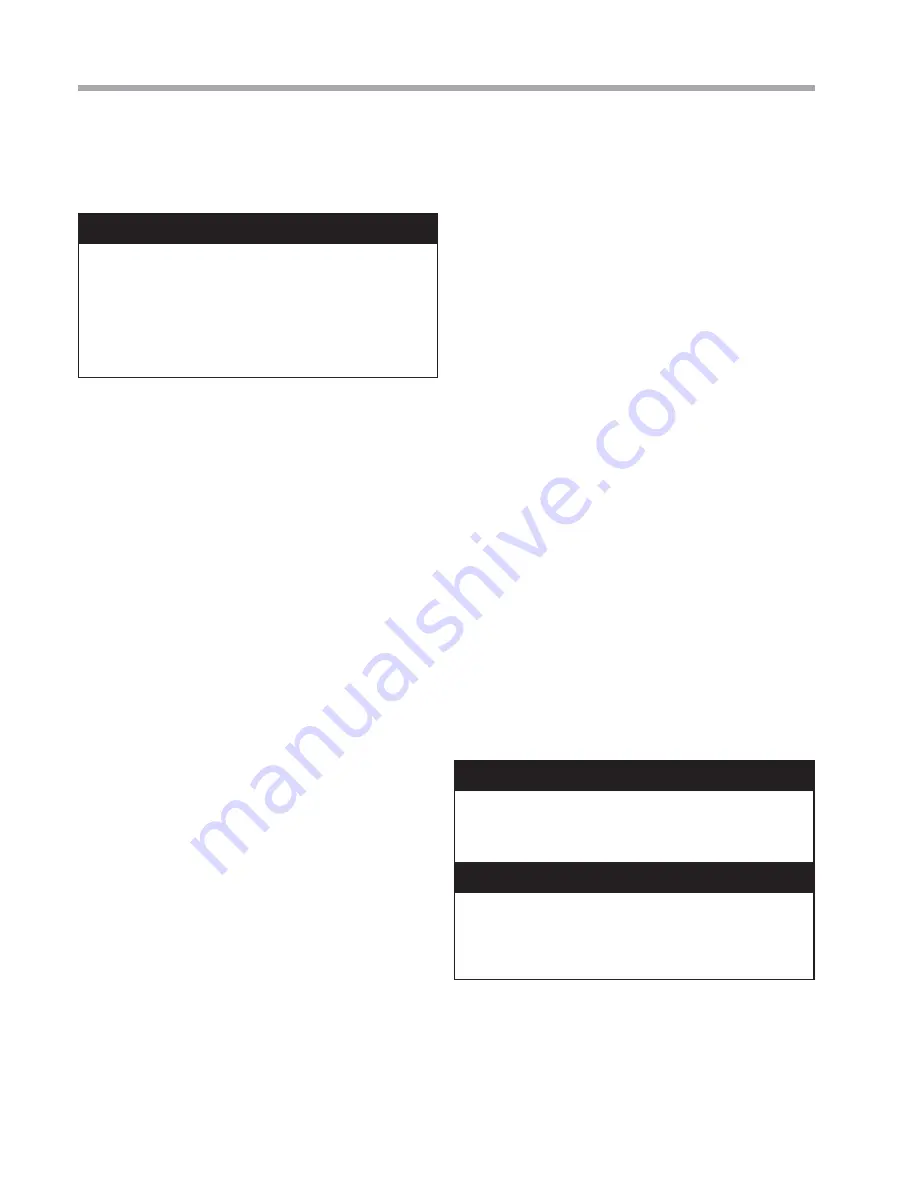
C L I M A T E M A S T E R W A T E R - S O U R C E H E A T P U M P S
Consoles
R e v. : 0 8 / 2 4 / 1 5
32
C l i m a t e M a s t e r Wa t e r - S o u rc e H e a t P u m p s
Unit and System Checkout Procedure
BEFORE POWERING SYSTEM, please check the
following:
UNIT CHECKOUT
Balancing/shutoff valves: Insure that all isolation valves
are open and water control valves are wired.
Line voltage and wiring: Verify that voltage is within
an acceptable range for the unit and wiring and fuses/
breakers are properly sized. Verify that low voltage
wiring is complete.
Unit control transformer: Insure that transformer has
the properly selected voltage tap. Commercial 208-
230V units are factory wired for 208V operation unless
specifi ed otherwise.
Entering water and air: Insure that entering water and
air temperatures are within operating limits of Table 8.
Low water temperature cutout: Verify that low water
temperature cut-out on the CXM/DXM control is
properly set.
Unit fan: Manually rotate fan to verify free rotation and
insure that blower wheel is secured to the motor shaft.
Be sure to remove any shipping supports if needed.
DO NOT oil motors upon start-up. Fan motors
are pre-oiled at the factory. Check unit fan speed
selection and compare to design requirements.
Condensate line: Verify that condensate line is open
and properly pitched toward drain.
Water fl ow balancing: Record inlet and outlet water
temperatures for each heat pump upon startup.
This check can eliminate nuisance trip outs and high
velocity water fl ow that could erode heat exchangers.
Unit air coil and fi lters: Insure that fi lter is clean and
accessible. Clean air coil of all manufacturing oils.
Unit controls: Verify that CXM or DXM fi eld selection
options are properly set.
SYSTEM CHECKOUT
System water temperature: Check water temperature
for proper range and also verify heating and cooling
set points for proper operation.
System pH: Check and adjust water pH if necessary
to maintain a level between 6 and 8.5. Proper pH
promotes longevity of hoses and fi ttings
(see Table 3).
System fl ushing: Verify that all hoses are connected
end to end when fl ushing to insure that debris
bypasses the unit heat exchanger, water valves and
other components. Water used in the system must be
potable quality initially and clean of dirt, piping slag,
and strong chemical cleaning agents. Verify that all air
is purged from the system. Air in the system can cause
poor operation or system corrosion.
Cooling tower/boiler: Check equipment for proper set
points and operation.
Standby pumps: Verify that the standby pump is
properly installed and in operating condition.
System controls: Verify that system controls function
and operate in the proper sequence.
Low water temperature cutout: Verify that low water
temperature cut-out controls are provided for the
outdoor portion of the loop. Otherwise, operating
problems may occur.
System control center: Verify that the control center
and alarm panel have appropriate set points and are
operating as designed.
Miscellaneous: Note any questionable aspects of
the installation.
CAUTION!
Verify that ALL water control valves are open and
allow water fl ow prior to engaging the compressor. Freezing
of the coax or water lines can permanently damage the heat
pump.
CAUTION!
To avoid equipment damage, DO NOT
leave system fi lled in a building without heat during the
winter unless antifreeze is added to the water loop. Heat
exchangers never fully drain by themselves and will freeze
unless winterized with antifreeze.
NOTICE! Failure to remove shipping brackets from
spring-mounted compressors will cause excessive
noise, and could cause component failure due to
added vibration.
CAUTION!
CAUTION!
WARNING!
Polyolester Oil, commonly known as POE oil, is
a synthetic oil used in many refrigeration systems including
those with HFC-410A refrigerant. POE oil, if it ever comes
in contact with PVC or CPVC piping, may cause failure of
the PVC/CPVC. PVC/CPVC piping should never be used
as supply or return water piping with water source heat
pump products containing HFC-410A as system failures and
property damage may result.
WARNING!