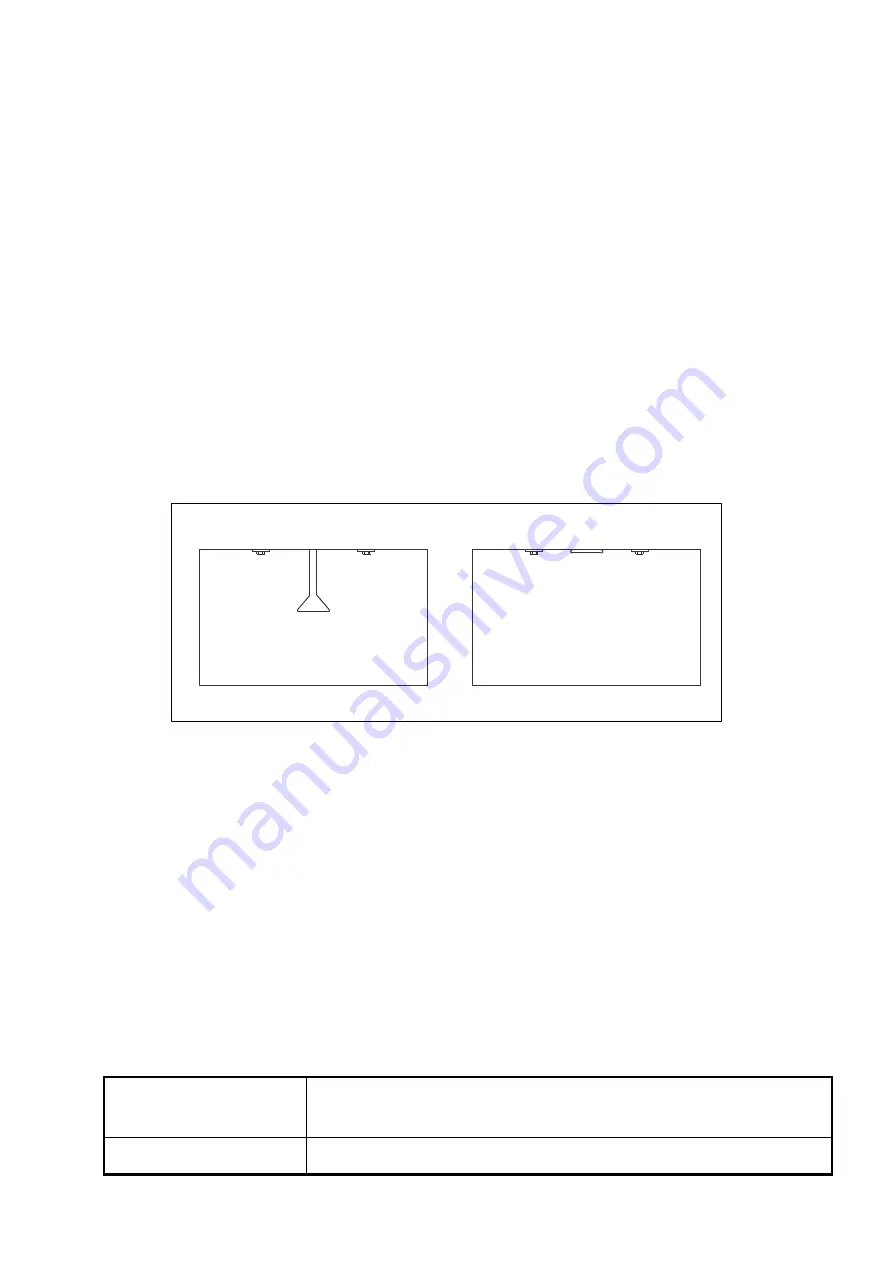
Page 8
The precautions described above also apply to portable compressors. In addition, in the case of
engine-driven compressors, precautions must be taken to prevent engine exhaust gases from en-
tering the air intake of the compressor. Compressor engine exhaust should be piped to a location
safely downwind from the compressor air intake. Compressors may vary in design and operation.
A fitted Air Filter like the CPF-20 Filter (part No 03580 D), has to be interconnected and must be
maintained regularly, to filter bad smells, oil fog, condensed water, rust from pipes and other con-
tents.
For trouble-free blasting we recommend an air supply free of oil and water.
5.2 Air Volume Velocity, Pressure and Hose Length
The quantity of air needed from a blaster for having enough oxygen to breathe is between
130l/min ... 190l/min.
This minimal quantity makes sure that the volume indicator is on function, which means that the flag is
pulled in
– otherwise the flag falls down.
As supply hoses between the air filter and the control valve you may use only CE-approved hoses with
safety couplings (see section 11
– spare parts).
The
maximum hose length
between the filter and the control valve can be
40m
. If it is necessary to use
longer hoses you have to contact the manufacturer to take appropriate measures.
The
maximum pressure
at the supply hose is
8bar
.
6 Operation
Prior to the operation, the helmet, breathing tube, air supply hose, air entry pots and fittings must
be thoroughly inspected and cleaned of all dust and debris. Also inspect the helmet suspension
and adjust it if necessary
(Adjustments see section 7.2).
The following steps have to be done before setting into operation:
(1) Air supply.
Start compressor.
Open service valve to pressurize the air supply line.
(2) Check air pressure.
Pressure must be set with the connected respirator.
View from inside
Too less air volume velocity
Enough air volume velocity