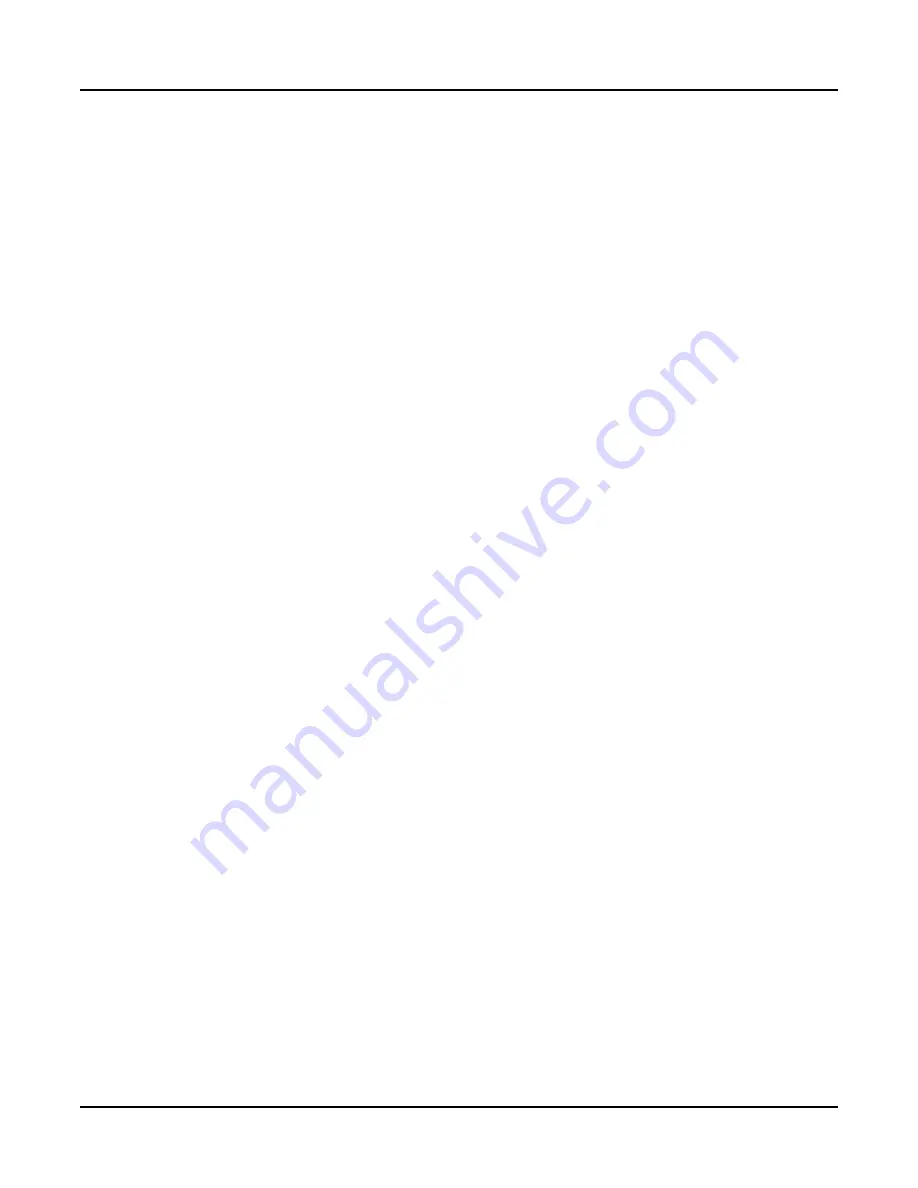
Chapter 1 — General
1-4
Part No. 750-386
1.3-Two Tank System Description
Two Tank systems can control up to 4 boiler feed pumps and 3
transfer pumps (6 pumps total), all of which can be run by
contactors, combination starters, soft starters, or Variable
Frequency Drives. The pump control method selected must be the
same for all pumps on a tank, but the Tank 1 method can be
different from Tank 2. For example, Tank 1 may use Variable
Frequency Drives, but Tank 2 may use contactors.
Pumps on a common header can be alternated on a customer
defined schedule and be set up in a customer defined lead lag
format.
When lead lag operation is in use, a pressure transmitter mounted
in the common header sends a signal to the PLC. The customer sets
the pressure point via the touch screen. If the first pump cannot
achieve that set point, the PLC will start a second pump and so on.
If the pressure rises above the set point, the PLC will shed the last
pump and so on. During normal operation the lead pump will
always run.
Pumps on a “one pump per boiler” installation can be controlled by
the boiler. Variable Frequency Drives cannot be used in a one pump
per boiler configuration where each pump is hard piped to
individual boilers. VFDs are only available on common pump
discharge header configurations.
Standard system is capable of using discrete level alarm switches
(such as the McDonnell Miller 63 or 64) for fixed level alarms, or a
level transmitter which can be configured from the touch screen.
1.3.1 - Standard Equipment
7 inch color touch screen is standard.
A three module stack light is standard with a light for each mode.
Green for normal, Yellow for non critical alarms Red for critical
alarms. An audible alarm is standard, either a bell, horn or
electronic sounder
PLC based control system for a two tank starts with and includes a
base unit consisting of the processor and embedded I/O, power
supply, I/O cards, 7" color touch screen, and Nema 4 control panel
to provide the following functions
Level control can be an independent mechanical system, or by using
the above mentioned transmitter, control an electrical or I/P make-
up valve.
Tank Pressure is monitored by a transmitter in steam space. PRV
can be an independent mechanical system or an electrical or I/P
pressure reducing valve.
The second tank will be treated as an atmospheric pressure tank
and will not have a tank pressure sensor.
Содержание ADAC 1000
Страница 1: ...750 386 05 2017 ADAC 1000 Deaerator Control Operation Manual...
Страница 11: ...www cleaverbrooks com Chapter 2 System Components Components 2 2 Control Panel 2 7 Optional Accessories 2 9...
Страница 22: ...Chapter 2 System Components 2 12 Part No 750 386...
Страница 87: ...www cleaverbrooks com Chapter 5 Input Output Lists Single Tank PLC I O Layout 5 2 Two Tank PLC I O Layout 5 4...
Страница 92: ...Chapter 5 Input Output Lists 5 6 Part No 750 386...
Страница 93: ...www cleaverbrooks com Chapter 6 Parts Parts List 6 2...
Страница 120: ...A 26 Part No 750 386...
Страница 128: ...APPENDIX B ADAC 1000 ProtoNode Tags B 8 Part No 750 386...
Страница 132: ...APPENDIX C Loading a PLC Program C 4 Part No 750 386...
Страница 133: ...APPENDIX D Deaerator Reference Drawings Part No 750 386 D 1 APPENDIX D Deaerator Reference Drawings Water Levels...
Страница 136: ...APPENDIX D Deaerator Reference Drawings D 4 Part No 750 386 Major Components DA with ADAC typical...
Страница 137: ...APPENDIX D Deaerator Reference Drawings Part No 750 386 D 5 Major Components Surge Tank with ADAC typical...
Страница 138: ...APPENDIX D Deaerator Reference Drawings D 6 Part No 750 386 Duo Tank Components typical...
Страница 139: ......
Страница 140: ...e mail info cleaverbrooks com Web Address http www cleaverbrooks com...