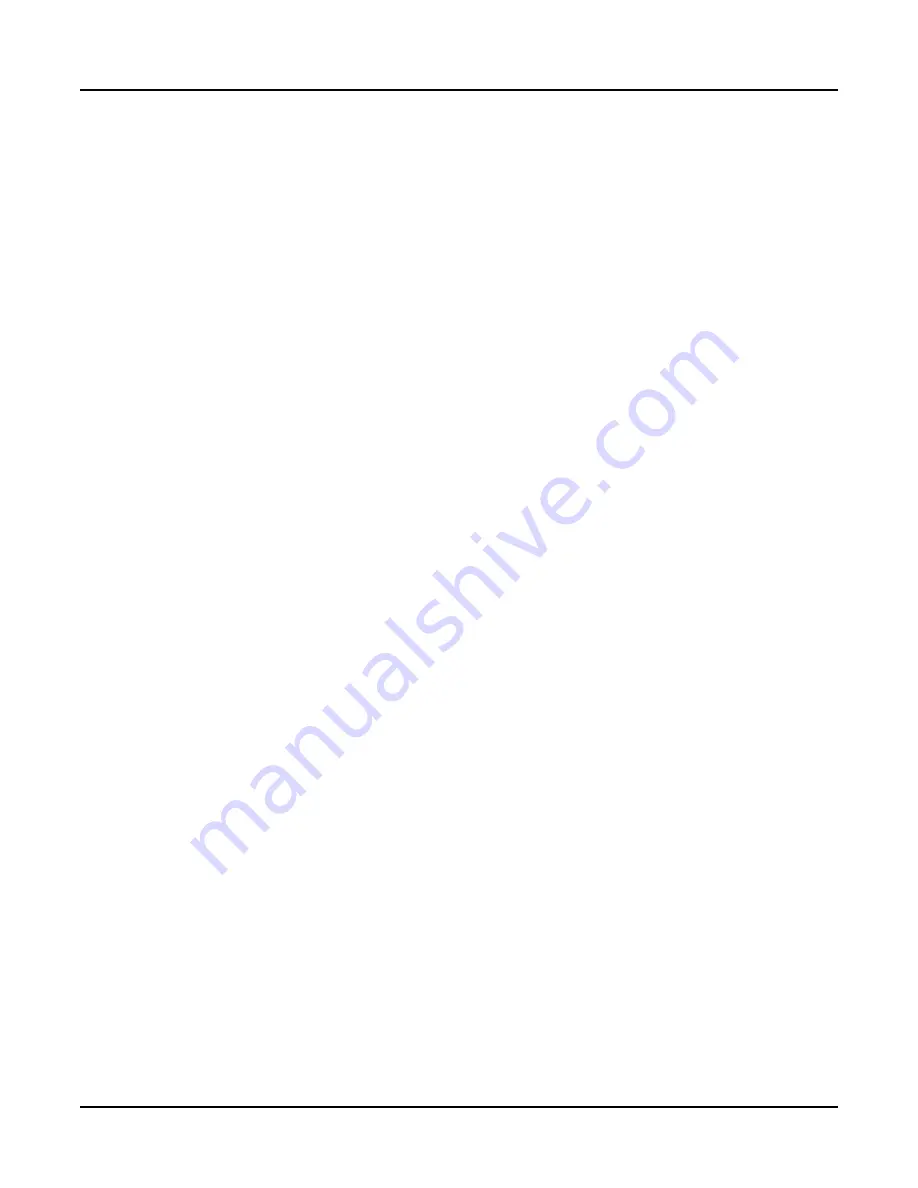
Chapter 4 — Operation
Part No. 750-386
4-5
• Status of the optional Flow Switches – OPEN/CLOSED
• Selector Switch Position HAND/OFF/AUTO
• OFF/ON/FAULT status for each of the Feed Pumps
• Lead-Lag status (Lead, Lag1, Lag2, etc.) for each of the Feed
Pumps
• Elapsed Run Time for each Feed Pump
• Feed Pump Alternate Time increment
• Lead Pump Elapsed Time (when the Alternate function is active)
The Feed Pump Control Screen provides the following Control
Functions:
• Individual Feed Pump START/STOP Push Buttons
When the Selector Switch is in AUTO(PLC) and the LEAD/LAG is
OFF, the START/STOP Push Button can be used to START/STOP
the corresponding Feed Pump.
If the LEAD/LAG is ON, the START/STOP Push Buttons are not
active.
• Individual Feed Pump LEAD/LAG assignment Push Buttons
These Push Buttons are used to assign the LEAD Pump and the
LAG Pump Sequence. Each Feed Pump must have its own
unique value or an “LEAD/LAG INVALID” indicator will appear on
the screen. Once a valid Lead-Lag Configuration has been
selected, the Lead/Lag button will become available for user to
enable Lead/Lag.
• START LEAD/LAG Push Button. This button will START and STOP
the Lead-Lag sequencing.
To START the LEAD/LAG function: At least two Feed Pumps need
to be Configured (present in the system) and have the Selector
Switch in the AUTO position.
When the Lead-Lag sequence is started, if a pump(s) has been
started with the Individual Feed Pump START/STOP Push
Button, if that pump is not the LEAD Pump, it will be shut off.
The LEAD Pump will be Started.
If one or more of the LAG Pumps is required, they will be Started.
When the LEAD/LAG function is turned off (LEAD/LAG STOP
Push Button), the Feed Pumps will be OFF.
• The <FEED PUMP ROTATION> Push Button. If a Feed Pump
Rotation Time value has been entered (on the Feed Pump Config
screen), The Feed Pump Rotation sequence can be Started and
Stopped using the <FEED PUMP ROTATION> Push Button.
• The <RESET Hours> and the <RESET Elapsed Time> push
buttons can be used to reset the corresponding elapsed time values
to 0 (zero).
Содержание ADAC 1000
Страница 1: ...750 386 05 2017 ADAC 1000 Deaerator Control Operation Manual...
Страница 11: ...www cleaverbrooks com Chapter 2 System Components Components 2 2 Control Panel 2 7 Optional Accessories 2 9...
Страница 22: ...Chapter 2 System Components 2 12 Part No 750 386...
Страница 87: ...www cleaverbrooks com Chapter 5 Input Output Lists Single Tank PLC I O Layout 5 2 Two Tank PLC I O Layout 5 4...
Страница 92: ...Chapter 5 Input Output Lists 5 6 Part No 750 386...
Страница 93: ...www cleaverbrooks com Chapter 6 Parts Parts List 6 2...
Страница 120: ...A 26 Part No 750 386...
Страница 128: ...APPENDIX B ADAC 1000 ProtoNode Tags B 8 Part No 750 386...
Страница 132: ...APPENDIX C Loading a PLC Program C 4 Part No 750 386...
Страница 133: ...APPENDIX D Deaerator Reference Drawings Part No 750 386 D 1 APPENDIX D Deaerator Reference Drawings Water Levels...
Страница 136: ...APPENDIX D Deaerator Reference Drawings D 4 Part No 750 386 Major Components DA with ADAC typical...
Страница 137: ...APPENDIX D Deaerator Reference Drawings Part No 750 386 D 5 Major Components Surge Tank with ADAC typical...
Страница 138: ...APPENDIX D Deaerator Reference Drawings D 6 Part No 750 386 Duo Tank Components typical...
Страница 139: ......
Страница 140: ...e mail info cleaverbrooks com Web Address http www cleaverbrooks com...