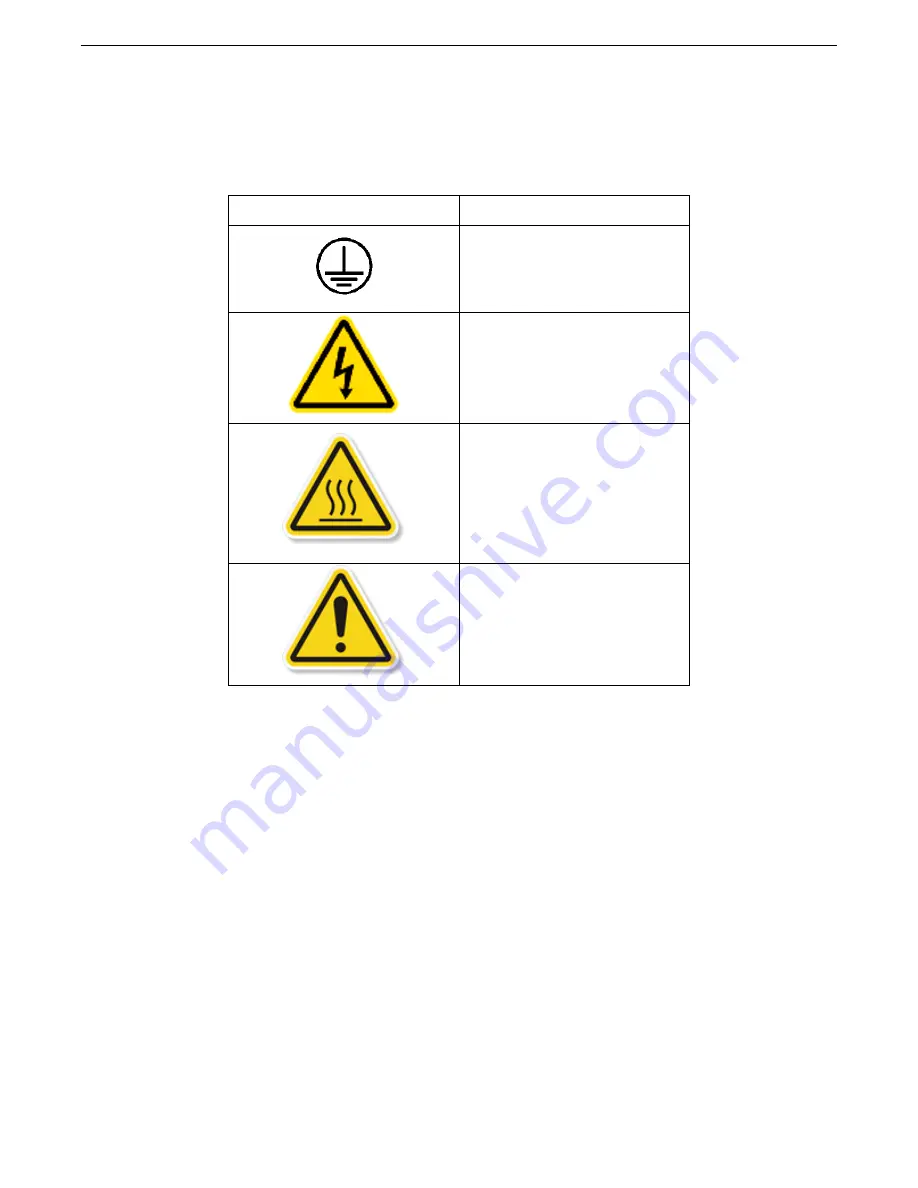
PREFACE P
-
5
Symbols Used on Equipment
Symbol
Meaning
Protective Conductor
Terminal
Hazardous Voltage Inside
Disconnect power before
opening
Hot Surface
Do Not Touch
Allow to cool before
servicing
Documentation must be
consulted in all cases
where this caution symbol
is marked.
Where to Find Help
Training classes are available in your laboratory and at Chandler Engineering. For more
information, contact our sales department at Chandler Engineering. In the event of problems,
your local sales representative will be able to help, or you can contact the personnel at
Chandler Engineering using the following:
•
Telephone:
1-918-250-7200
•
FAX:
1-918-459-0165
•
E-mail:
•
Website:
www.chandlereng.com
Содержание AMETEK 7200
Страница 10: ......
Страница 16: ...2 2 SECTION 2 OPERATING INSTRUCTIONS Figure 1 Front Panel...
Страница 38: ......
Страница 48: ...5 2 SECTION 5 TROUBLESHOOTING GUIDE This page is intentionally left blank...
Страница 50: ...6 2 SECTION 6 REPLACEMENT PARTS This page is intentionally left blank...
Страница 52: ...6 2 SECTION 6 REPLACEMENT PARTS This page is intentionally left blank...
Страница 65: ...CHANDLER ENGINEERING...
Страница 66: ......
Страница 76: ...cut out postcards on dotted lines...