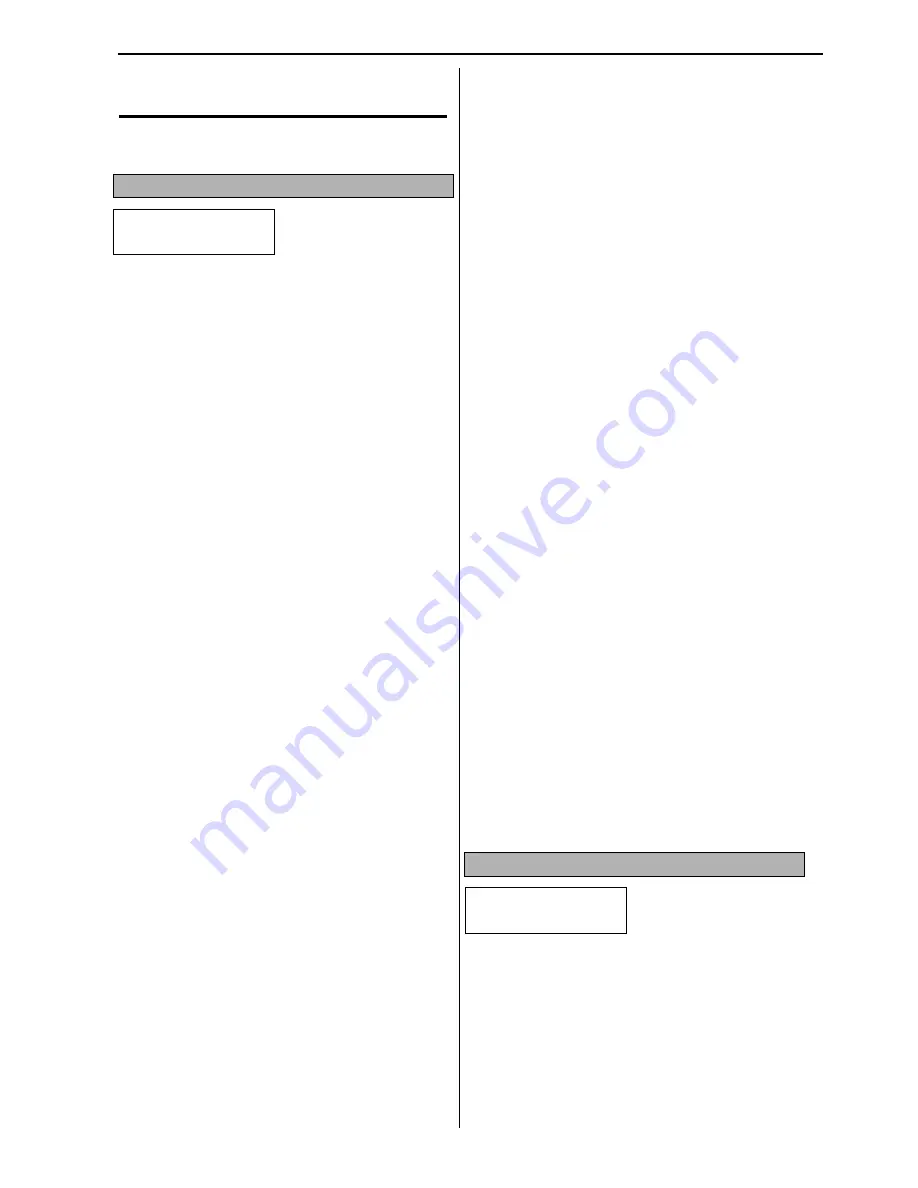
Chapter 6 - Parameter Description
6-1
CHAPTER 6 -
PARAMETER
DESCRIPTION
6.1 Setup group [SET]
)**+ %
!
!
The first step in
VFD setup is an
application selection.
When VFD is powered up first time, the screen
SET-00 shows no application selected (None).
Press [ENTER] key and [UP] key to select proper
application for your motor. Many parameters in
VFD parameter groups will be automatically set to
provide most stable and reliable equipment
operation.
There are eight application choices: Basic,
Supply Fan, Exhaust Fan, Cooling Tower Fan,
Circulating Pump, Submersible Pump, Vacuum
Pump, and Constant Torque.
The Basic
selection provides a
standard basic
VFD control with start/stop command from via
keypad and speed reference via remote 4-20mA
analog signal. Most of the advanced motor control
and protective features such as, Damper Control,
Under Load Protection, Pipe Broken, etc. are
disabled. This control method can be used in many
applications where VFD simply needs to follow a
remote speed reference signal and start/stop
command from the keypad.
The Supply or Exhaust Fan
selection sets VFD
for remote BMS (Building Management System) or
PLC (Programmable Logic Controller) Start/Stop
control and 4-20mA speed reference signal. If
application requires the VFD to utilize internal PID
(Proportional- Integral) control with pressure
transducer feedback, the PID parameter SET-20
should be enabled. All other related parameters
such as Transducer range, Process Unit inWC,
Direct or Inverse PID, etc. will be automatically set
to the most common factory default values
providing accurate motor control. In some cases
extra adjustment of some parameters is necessary to
achieve better control. Stop mode is set to Coast
mode to protect from any possible overvoltage trips
while decelerating during stop mode.
The Cooling Tower Fan
selection configures
VFD for fan motor with internal inverse PID
control and feedback from a temperature transducer.
The process unit is set to °F with 0-122°F
temperature transducer range and 80°F PID set
point. If MMC (Multi-motor Control) feature is
enabled with one of the auxiliary relays, the VFD
can start a spray pump based on VFD speed and
system temperature. The inverse PID control
increases fan motor speed if temperature is above
set point.
The Circulating Pump
selection provides
constant pressure PID control with pressure
transducer feedback. The process unit is set to PSI
with 0-100PSI transducer range and 50PSI set-point.
The sleep mode is enabled and parameters are set to
optimal values, which should be readjusted for
better performance based on the system parameters
and type of pump. There is an adjustable run time
delay parameter FG1-81 that can be used as a
backspin timer. If the application is a hollow shaft
pump and it requires to run water for bearing
lubrication before motor starts, there are selections
“Lubrication Mode” and “Lubrication Timer” in
parameters I/O-68, 69, 76~79, which will control a
selected auxiliary relay to activate a water solenoid
valve for an adjustable time delay before pump
motor starts.
The Submersible Pump
selection provides, in
addition to Circulating pump, default features Pre-
PID (Pipe Fill mode), Pipe Broken and Under Level
Protection with well fill timer (Dry Well protection).
The default settings for some parameters are:
Acceleration Time is 2sec., Deceleration Time is
10sec., and motor speed is 3600RPM. The process
unit is set to PSI with 0-100PSI transducer range
and 50PSI set-point. Some parameters should be
readjusted for better control based on the pump type
and system parameters.
The Vacuum Pump
selection provides constant
vacuum (negative pressure) PID control with
vacuum transducer feedback. The process unit is set
to inWC with 0-406.9inWC transducer range and
60inWC vacuum set-point. The sleep mode and
other pump control features are disabled but can be
activated. The default parameter settings are set to
optimal values and should be readjusted based on
system parameters.
The Constant Torque
application selection sets
VFD to 20% de-rated motor HP(horse power)
rating, start/stop command from terminal blocks
and speed reference control from a keypad. This
control selection is suitable for conveyors, grinders,
mixers and similar applications.
)* + $! ' ,
!
The VFD is capable of
running from 3-Phase
or Single-Phase power source but it should be 50%
de-rated for Single-Phase input power. When this
parameter is set to Single-Phase mode, the motor
HP rating is automatically changed to 50% of the
VFD capacity. All protective and filtering devices
on VFD power input should be sized based on
doubled motor FLA.
SET App. Select
00 None
SET Input Phase
01 3-Phase
Содержание CI-007-P2
Страница 23: ......
Страница 107: ......
Страница 109: ...Chapter 6 Parameter Description 7 2 7 3 PID control Sleep mode with Sleep Pressure Boost function diagram...
Страница 110: ...Chapter 6 Parameter Description 7 4 PID control with Pipe Broken function diagram...
Страница 111: ...Chapter 6 Parameter Description 7 4 7 5 PID control with Pre PID function diagram...
Страница 112: ...Chapter 6 Parameter Description 7 5 7 6 PID Control Setting Notes...
Страница 113: ......
Страница 126: ...Chapter 9 Options 9 7 Conduit box for 030 040HP VFD Conduit box for 050 075HP VFD Conduit box for 100 125HP VFD...