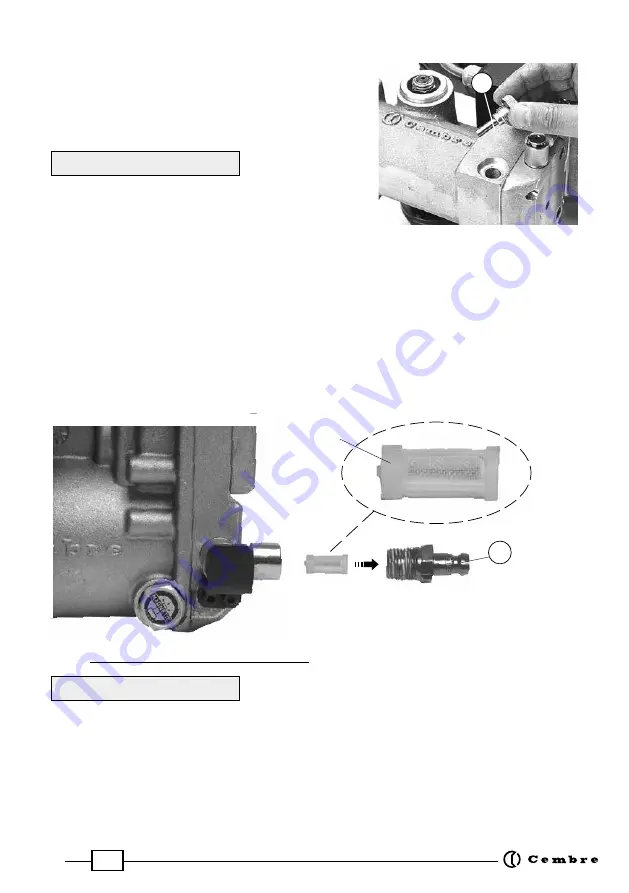
27
anti-impurity filter
02
FIG. 27 –
COOLANT FILTER CLEANING
21
11.1.2) Removal of metallic residues from the crankcase
When the drill is positioned as shown in Figure unscrew
the appropriate cap, with magnetic insert (21) on which
any metallic residue will have collected.
Carefully clean the magnetic insert with a clean rag and
screw it back in the appropriate housing.
Every 50 hours of operation
11.1.3) Checking of screws
– Check and re-tighten all screws where necessary.
11.1.4) Lubrication
Lubricate the spindle support housing by means of the appropriate lubricator (35), the screw of
the clamping device with moving arm,
DBG-F2
and
DBG-LF2
.
11.1.5) Coolant filter cleaning
(Ref. to Fig. 27)
The coolant circuit of the drilling machine is provided with anti-impurity filter; should an evident
decrease of the flow of the lubrocoolant occur, it could be necessary to clean the filter in the
following way:
– Using a 14 mm key, unscrew the coupling (02).
– Extract the filter and clean it carefully.
– Reassemble the filter into the coupling (02) as shown in the Fig. 27 and fully tighten the
coupling.
11.2) ROUTINE MOTOR MAINTENANCE
(Ref. to Fig. 28)
Every 50 hours of operation
11.2.1) Changing the brushes
After disconnecting the power plug check the degree of wear of the brushes; if necessary replace
them by proceeding as follows:
– Unscrew with a screwdriver the two screws located underneath the protective covers.
– Remove the two protective covers.
– Replace the brushes.
– Reassemble the two protective covers.
– Tighten the locking screws.