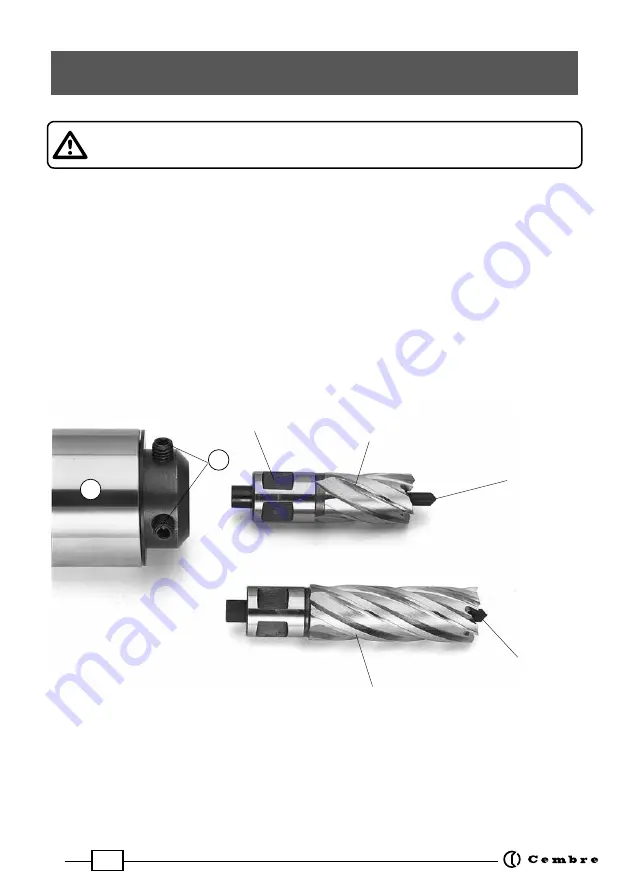
13
DISCONNECT always the power supply when servicing the drill:
before removing the broach cutters, spiral bits, positioning templates etc.
6.1) Assembling broach cutters
(Ref. to Figs. 8-11).
6.1.1)
Insert the guide bit in the cutter from the side of the spigot.
6.1.2)
Using the lever (36), position the spindle shaft (07) so that both grub screws (18) become
accessible and sufficient space is provided to insert the cutter; if necessary rotate the
spindle shaft manually and sufficiently by inserting the 4 mm male hexagon key in the
appropriate intermediate gear housing (33) in the crankcase of the drill corresponding
to the feed handle (71) (see Fig. 11).
6.1.3)
Insert the cutter in the spindle shaft so that the two engaging dogs on the cutter spigot
line up with the grub screws.
6.1.4)
Clamp the cutter by fully tightening the grub screws by means of the 4 mm male hexagon
key.
6.1.5)
Check that the guide bit slides freely by applying slight pressure on it.
6.2) Assembling spiral bits
(Ref. to Figs. 9 - 11)
6.2.1)
Using the advance lever, position the spindle shaft so that both grub screws become
accessible and sufficient space is provided to insert the spiral bit; if necessary rotate the
spindle shaft manually and sufficiently by inserting the 4 mm male hexagon key in the
appropriate intermediate gear housing in the crankcase of the drill corresponding to the
feed handle (see Fig. 11).
Short type broach cutter
Maximum drilling thickness: 25 mm
Guide bit PP..
Long type broach cutter
Maximum drilling thickness: 50 mm
Guide bit PPL..
Engaging dogs
07
18
FIG. 8 – ASSEMBLING BROACH CUTTERS
6. PREPARING THE RAIL DRILL