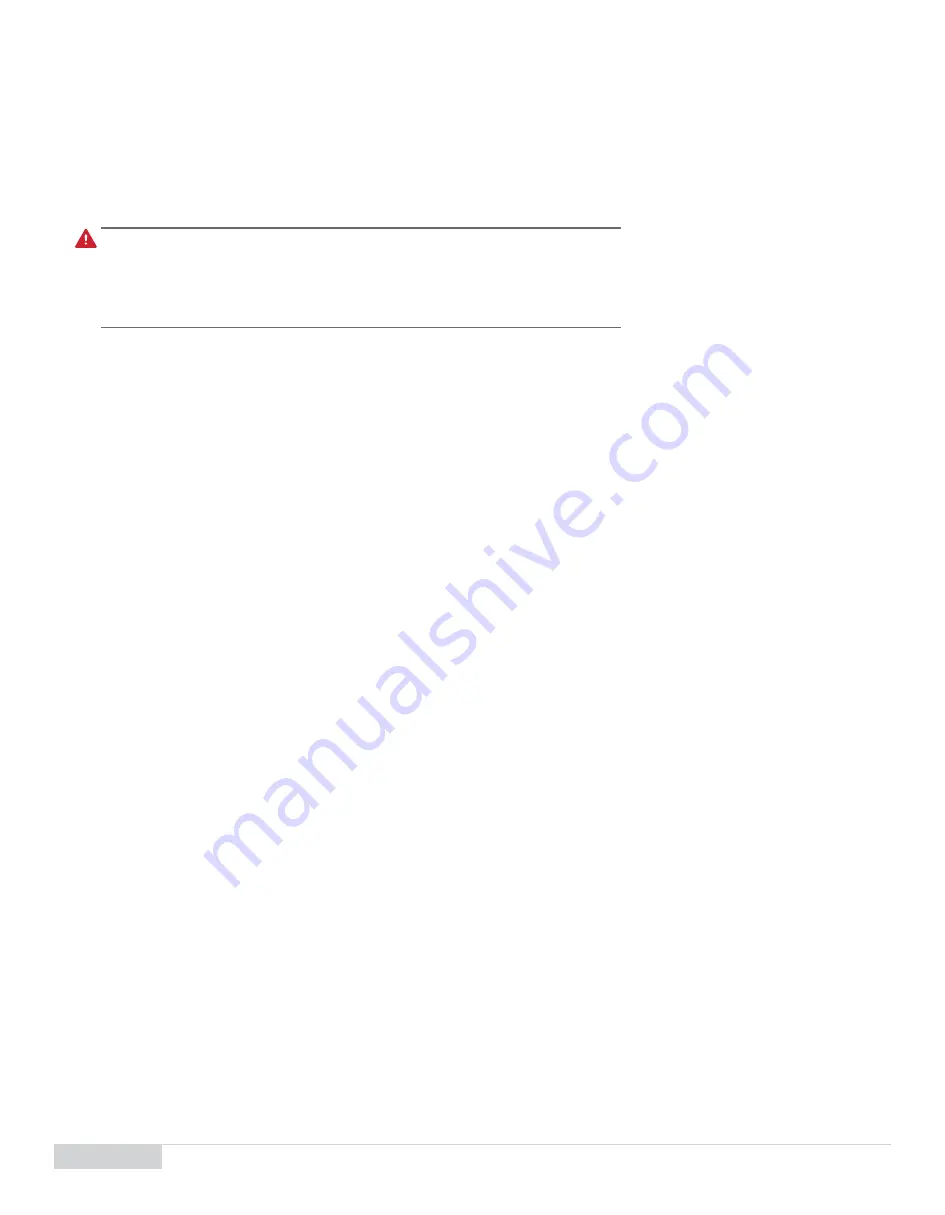
CCH® Elite Operation and Installation Manual (Model CCH1-HCE) Rev 1.0 3/2020
8
4
Pre-installation Instructions
4 .1 Prepare the Site
Before installing equipment, ensure that:
1.
The site has all electrical connections installed. All electrical lines should be secured to meet site safety procedures and to prevent tripping
over electrical lines.
Danger:
All wiring connections, fusing, grounding, inspection, and maintenance of wiring
must be performed by a licensed electrician in accordance with the National Electric
Code (NEC), Occupational Safety and Health Act (OSHA) in the United States, and all
local electrical codes. Failure to properly install and wire this product can result in
property damage, injury, or death, and may affect warranty coverage.
2.
Site meets criteria noted in Site Requirements on page 8.
4.1.1
Site Requirements
The feeder must fit in the selected room with enough clearance for maneuvering and servicing the equipment.
–
Recommended clearance for feeder installation is 48" L x 48" W x 76" H [121.9 cm x 121.9 cm x 193.0 cm]
–
Minimum clearance for feeder installation is 36" L x 36" W x 64" H [91.4 cm x 91.4 cm x 162.6 cm].
The room must have proper ventilation.
The room must be climate-controlled between 40 °F – 90 °F [4 °C – 32 °C].
Required electrical service as follows:
–
100 - 240 V AC / 15 - 20 A dedicated outlet.
–
50 - 60 Hz single-phase only.
–
50 Hz systems require a locally-sourced booster pump (see booster pump section, page 11, for more information.
Determine the inlet and outlet location of the booster pump and venturi loop.
–
It is preferable to install this loop across the heater bypass valve to maximize the pressure differential of the system to enhance
performance.
–
The booster pump suction should always be downstream of the pool filter(s) to ensure the use of clean, filtered water to protect the
solenoid valves. Refer to Figure 1. Process Flow Diagram - Chlorination System on page 6 for proper location of piping connections.
–
The booster pump and venturi should be located to minimize the use of 90° elbows on the venturi outlet.
The following cable lengths need to be considered for placement of the control box and feeder:
–
The control box feeder cable is 20 ft [6 m]; the feeder will need to be within 20 ft [6 m] of the control box.
–
The ORP control cable is 20 ft [6 m]; the control box will need to be within 20 ft [6 m] of the ORP controller.
–
The flow switch cable is 32 ft [10 m]; the distance between the control box and flow switch should be considered.
4 .2
Gather Equipment for Feeder Installation
Assemble these products in preparation for installation:
CCH® Elite components
Essential equipment supplied by others
Commercial off-the-shelf (COTS) tools
Personal Protective Equipment (PPE)
4.2.1
CCH® Elite Components
See the Components List on page 7.