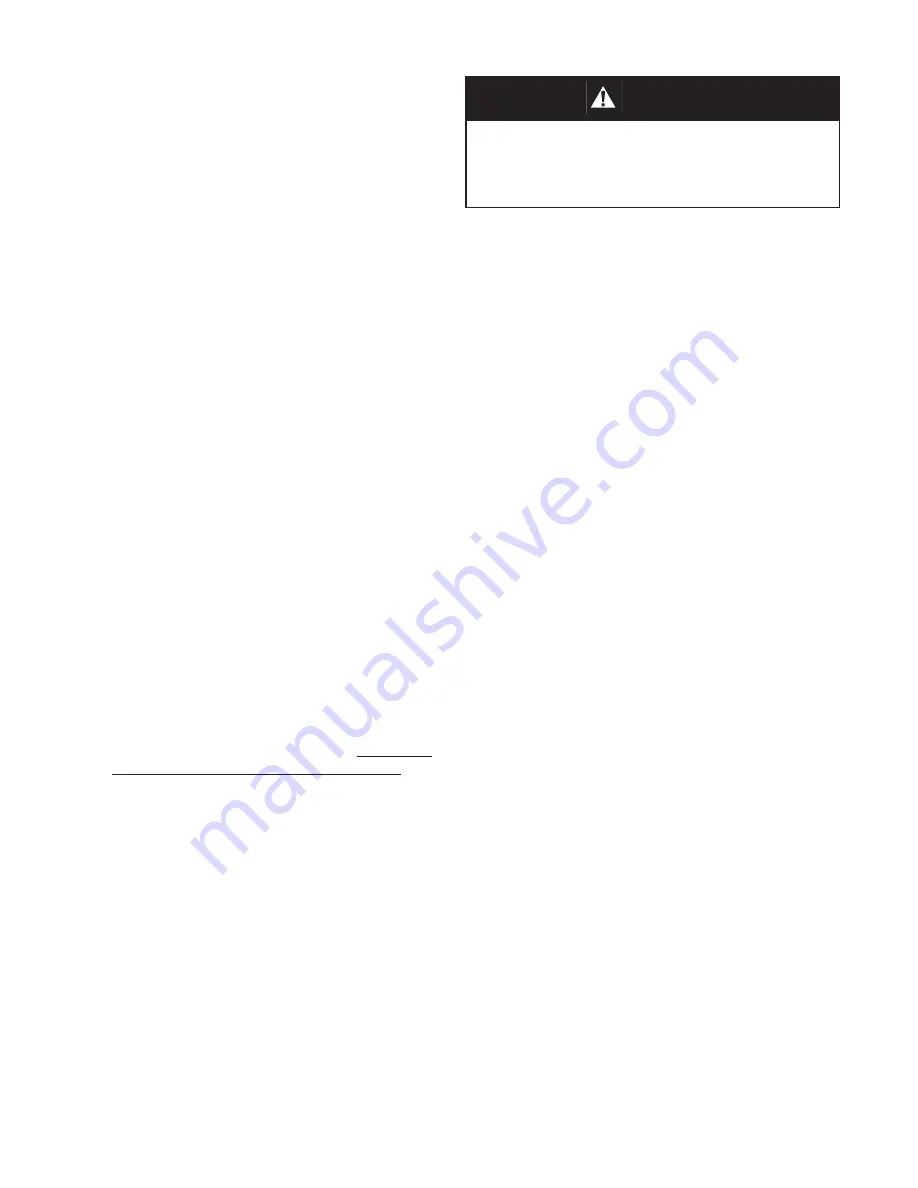
IOM-HP-S-DIFF
2
V. SHUTDOWN
SECTION V
SECTION IV
* NOTE:
Systems sequencing operations at startup,
normal operation, failure mode(s), and shutdown must
assure that the pressure (P
Load
) on the spring chamber does
not exceed the pressure registering on the wetted side of
the diaphragm. Should this "pressure reversal" occur,
particularly to metal diaphragms, the diaphragm may be
permanently damaged and cause improper operation.
P
1
> P
2
> P
Load
Pressure reversal is normally caused by the inlet pressure
to a regulator being interrupted (automatically or manually)
.
1. On initial start-up with your system op er at ing at
nor mal conditions, check the differential gauge to
ensure the desired differential pressure is being
maintained. If not, go to step 2 and make one final
ad just ment. (This should only be nec es sary on
first start-up.)
NOTE:
It is crucial that the ad just ing
screw (6) threads not be dam aged. Do not use
any type of pliers on the adjusting screw (6).
REFER TO THE COM PRES SOR / EXPANDER MAN U FAC TUR ER'S MANUAL FOR DETAILED SHUTDOWN
OF THIS UNIT.
2. To adjust differential setting, use one of the two
following methods: (
NOTE:
Both methods re quire
a flowing condition
.)
a. Loosen the closing cap (28) by turning CCW
(as viewed from above) 3 to 4 complete
rev o lu tions. Loos en lock nut (7) by turning CCW
until it is tight (dou ble-nutted) against closing
cap (28). Now the dif fer en tial set ting may be
ad just ed by turn ing the closing cap (28) CW
to increase dif fer en tial or CCW to de crease.
After desired setting is reached, loos en lock
nut (7) from clos ing cap (28) and tighten each
se cure ly to spring cham ber (2).
b. Remove closing cap (28) from ad just ing screw
(6) by turning CCW. Loosen lock nut (7) by
turning CCW. Adjust the differential setting by
turning the ad just ing screw (6) CW to in crease
dif fer en tial pres sure or CCW to de crease.
Tight en lock nut (7) se cure ly to spring chamber
(2). Re place closing cap (28) and tighten.
REFER TO THE COMPRESSOR / EXPANDER MANUFACTURER'S MANUAL FOR DETAILED START-UP OF
THIS
UNIT.
IV. STARTUP
CAUTION
Limit any field hydrostatic test to 1-1/2 times the Maximum
Outlet and Spring Chamber Pressure Rat ing (See Ta ble
2 in HP-S-DIFF TB). En sure that the test pressure is
applied uni form ly to the body inlet, body outlet, and spring
chamber.
2. A complete diaphragm failure will cause the
reg u la tor to fail open.