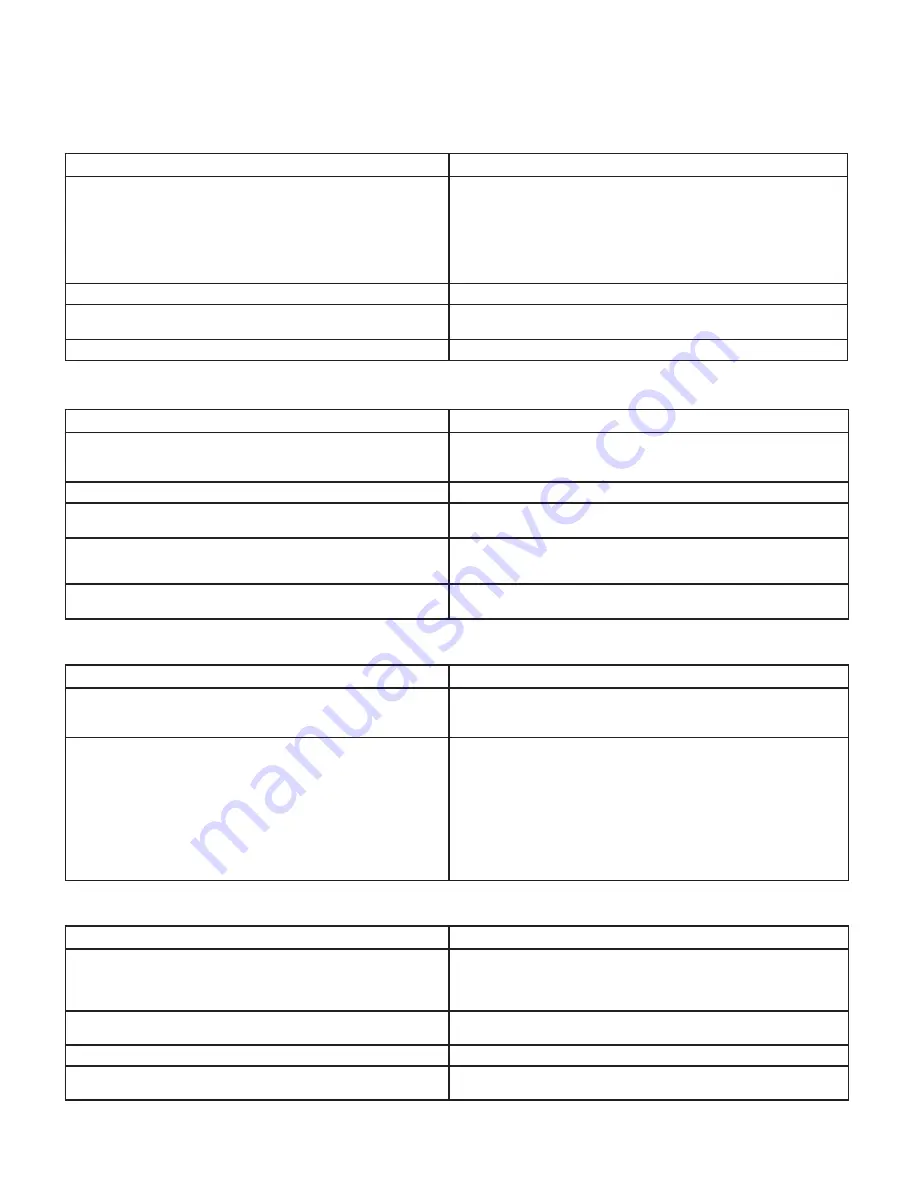
IOM-HP-S-DIFF
6
SECTION VII
VII. TROUBLE SHOOTING GUIDE
Possible Cause
Remedy
A.
Oversized regulator; inadequate rangeability.
A1.
A2.
A3.
A4.
A5.
Check actual flow conditions, resize regulator for minimum and
maximum flow.
Increase flow rate.
Decrease regulator pressure drop; decrease inlet pressure by placing
a throttling orifice in inlet piping union.
Install next step higher range spring. Contact factory.
Before replacing regulator, contact factory.
B.
Worn piston; inadequate guiding.
B.
Replace trim.
C.
Weakened/broken piston spring.
C.
Replace piston spring. De ter mine if corrosion is causing the failure.
If so, consider NACE acceptable trims.
D.
Unstable loading pressure.
D.
Stabilize loading pressure; i.e. pump, control valve, etc.
1. Erratic operation; chattering.
Possible Cause
Remedy
A.
Regulator undersized;
A1.
A2.
Con firm by opening bypass valve together with regulator.
Check actual flow conditions, resize regulator; if regulator has
inadequate ca pac i ty, replace with larger unit.
B.
Plugged trim.
B.
Re move trim and check for plugged holes in cylinder.
C.
Incorrect range spring (screwing in adjusting screw CW does not
bring pressure up to proper level).
C.
Re place range spring with proper higher range. Contact factory.
D.
Too much proportional band (droop); outlet (P
2
) pressure droops
below load pressure (P
LOAD
).
D1.
D2.
Re view Proportional Band (droop) expected.
Con tact factory.
E.
Restricted diaphragm movement.
E.
En sure no moisture in spring chamber at temperatures below freeze
point.
2. Downstream pressure will not reach desired setting.
Possible Cause
Remedy
A.
Normal-life diaphragm failure.
A1.
A2.
Re place diaphragm.
Check actual flow conditions, resize regulator; if regulator has
inadequate ca pac i ty, replace with larger unit.
B.
Abnormal short-life diaphragm failure.
B1.
B2.
B3.
B4.
B5.
Can be caused by excessive chattering. See VII - 1. to remedy
chatter.
Can be caused by corrosive action. Consider NACE acceptable
trims.
En sure not subjecting to over-temperature conditions.
Down stream outlet (P
2
) pressure buildup occurring that overstresses
di a phragms. Protect with safety relief valve.
Inlet (P
1
) pressure valve is shutoff while loading (P
LOAD
) pressure
is still on.
3. Leakage through body spacer vent hole, or mixing of fluids.
Possible Cause
Remedy
A.
Regulator not closing tightly.
A1.
A2.
In spect the seating. Replace if depressed, nicked or embedded
with debris.
Inspect guides in body cap. If damaged, replace body cap and/or
piston.
B.
Downstream block.
B.
Check system; isolate (block) flow at regulator inlet - not outlet.
Relocate regulator if necessary.
C.
No pressure relief protection.
C.
In stall safety relief valve, or rupture disc.
D.
Restricted diaphragm movement.
D1.
Ensure no moisture in spring chamber at temperatures below
freeze point.
4. Excessive pressure downstream.