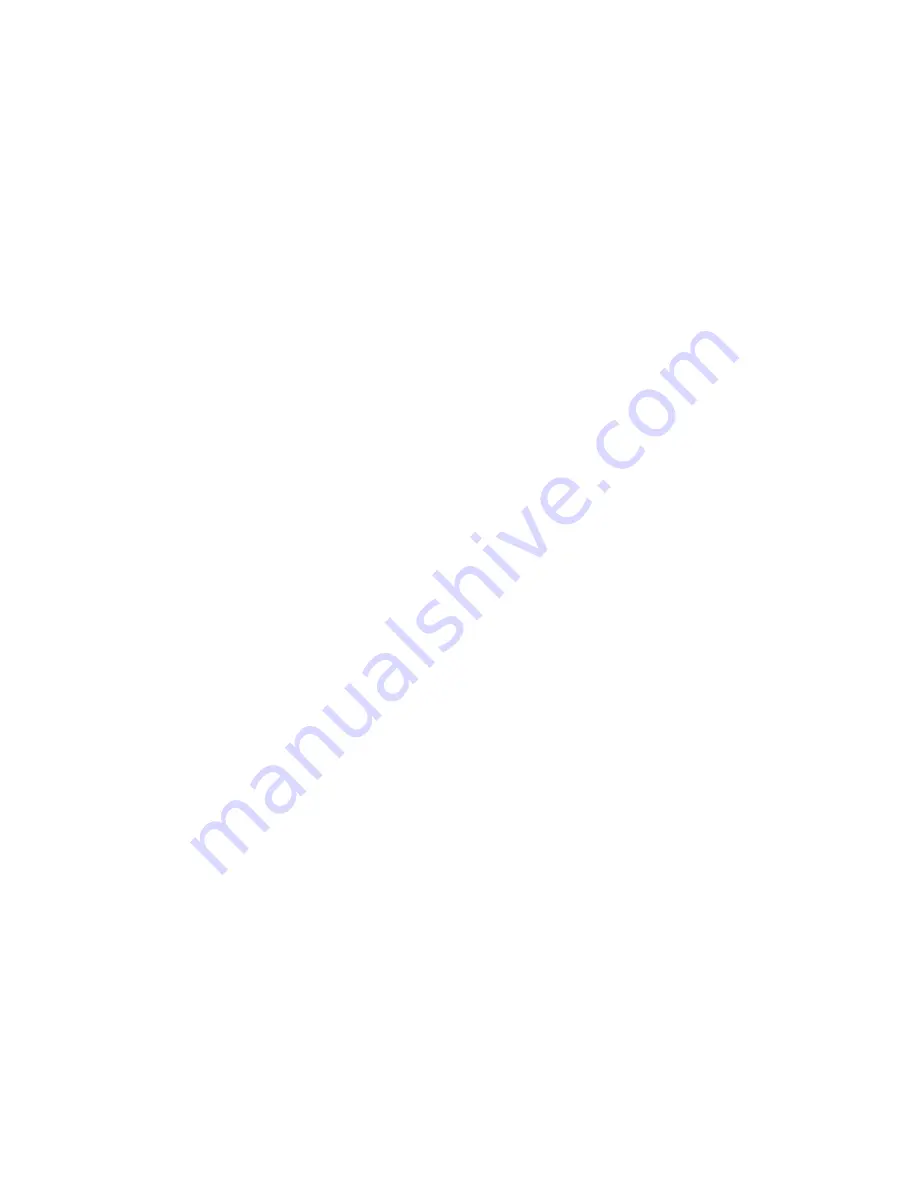
IOM-HP-S-DIFF
10
Cashco, Inc.
P.O. Box 6
Ellsworth, KS 67439-0006
PH (785) 472-4461
Fax. # (785) 472-3539
www.cashco.com
email: [email protected]
Printed in U.S.A. IOM-HP-S-Diff
Cashco do Brasil, Ltda.
Al.Venus, 340
Indaiatuba - Sao Paulo, Brazil
PH +55 11 99677 7177
Fax. No.
www.cashco.com
email: [email protected]
Cashco GmbH
Handwerkerstrasse 15
15366 Hoppegarten, Germany
PH +49 3342 30968 0
Fax. No. +49 3342 30968 29
www.cashco.com
email: [email protected]
indicating the gauge is compliant with the ATEX Directive (See items 26, 27, and 28 in Appendix A). Until compliance
is determined, regulators should not be ordered with pressure gauges for use in potentially explosive environments.
3.
Tied diaphragm regulators with outlet ranges greater than 100 psig should be preset to minimize the risk that improper
operation might lead to an outboard leak and a potentially explosive atmosphere (See item 6 in Table 1).
4.
Regulators must be ordered with the non-relieving option (instead of the self-relieving option) if the process gas they are
to be used with is hazardous (flammable, toxic, etc.). The self-relieving option vents process gas through the regulator
cap directly into the atmosphere while the non-relieving option does not. Using regulator with the self- relieving option
in a flammable gas system could create an explosive atmosphere in the vicinity of the regulator.
5.
Regulators with customer supplied parts are to be assumed to not have been evaluated with regard to ATEX and thus
are not to be used in a potentially explosive environment unless a documented evaluation for the specific customer
supplied parts in question has been made. Refer to Table 1 for all models and options that have been evaluated.
Product Usage
A summary of ATEX related usage issues that were found in the assessment are listed below.
1.
Pressure regulators and control valves must be grounded (earthed) to prevent static charge build-up due to the flowing
media. The regulator can be grounded through any mounting holes on the body with metal to metal contact or the
system piping can be grounded and electrical continuity verified through the body metal seal connections. Grounding
of the regulator should follow the same requirements for the piping system. Also see item 30 in Table 1.
2.
The system designer and users must take precautions to prevent rapid system pressurization which may raise surface
temperatures of system components and tubing due to adiabatic compression of the system gas.
3.
Heating systems installed by the user could possibly increase the surface temperature and must be evaluated by the
user for compliance with the ATEX Directive. User installation of heating systems applied to the regulator body or
system piping that affects the surface temperature of the pressure regulator is outside the scope of this declaration and
is the responsibility of the user.
4.
The Joule-Thomson effect may cause process gases to rise in temperature as they expand going through a regulator.
This could raise the external surface temperature of the regulator body and downstream piping creating a potential
source of ignition. Whether the Joule-Thomson effect leads to heating or cooling of the process gas depends on
the process gas and the inlet and outlet pressures. The system designer is responsible for determining whether the
process gas temperature may rise under any operating conditions. If a process gas temperature rise is possible under
operating conditions, then the system designer must investigate whether the regulator body and downstream piping
may increase in temperature enough to create a potential source of ignition.
The process gas expansion is typically modeled as a constant enthalpy throttling process for determining the temperature change.
A Mollier diagram (Pressure – Enthalpy diagram with constant temperature, density, & entropy contours) or a Temperature –
Entropy diagram with constant enthalpy lines, for the process gas, can be used to determine the temperature change. Helium
and hydrogen are two gases that typically increase in temperature when expanding across a regulator. Other gases may
increase in temperature at sufficiently high pressures.
Product Declaration
If the above issues are addressed by selecting options that do not have potential sources of ignition, avoiding options that
have not been assessed, and by taking the proper usage issue precautions, then Cashco regulators can be considered to be a
mechanical device that does not have its own source of ignition and thus falls outside the scope of the ATEX directive.