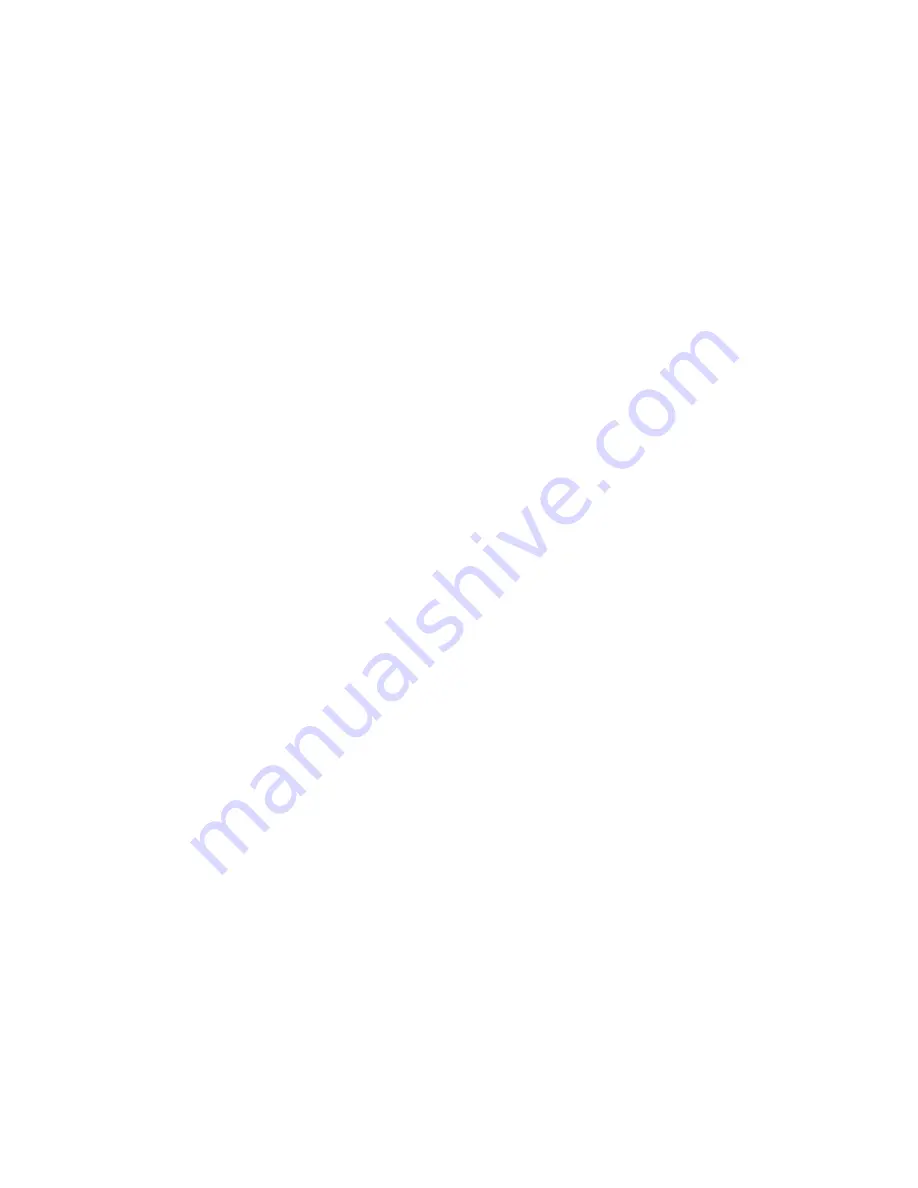
40
10.3 - Electronic expansion device (EXV)
The microprocessor controls the EXV through the EXV control
module. Inside this EXV is a linear actuator stepper motor. High-
pressure liquid refrigerant enters the valve through the bottom. A
series of calibrated slots are located inside the orifice assembly.
As refrigerant passes through the orifice, the pressure drops and
the refrigerant changes to a 2-phase condition (liquid and vapour).
To control refrigerant flow for different operating conditions, the
sleeve moves up and down over the orifice, thereby changing
effective flow area of expansion device. The sleeve is moved by
a linear stepper motor. The stepper motor moves in increments
and is controlled directly by the processor module. As the stepper
motor rotates, motion is transferred into linear movement by the
lead screw. Through the stepper motor and lead screws, 1500
discrete steps of motion are obtained. The large number of steps
and long stroke result in very accurate control of refrigerant flow.
At initial start-up, the EXV position is at zero. After that, the
microprocessor keeps accurate track of the valve position in order
to use this information as input for the other control functions. It
does this by initializing the EXV’s at startup. The processor sends
out enough closing pulses to the valve to move it from fully open
to fully closed, then resets the position counter to zero. From this
point on, until the initialization, the processor counts the total
number of open and closed steps it has sent to each valve.
10.4 - Economizer
Economizers are installed on 30HXC 190, 285 and 375.
The economizer improves both the chiller capacity and efficiency as
well as providing motor cooling. The economizers used are direct-
expansion plate heat exchangers.
The flow of the direct-expansion plate heat exchanger circuit is
adjusted by the thermostatic cooling valves.
10.5 - Oil pumps
The 30HXC screw chillers use one externally mounted
pre-lubricating oil pump per circuit. This pump is operated as part
ot the start-up sequence.
ATTENTION: The operating temperature of the coil may reach
80°C. In certain temporary conditions (especially during
start-up at low outside temperature or low condenser loop
temperature) the oil pump can be reactivated.
10.6 - Motor cooling valves
Compressor motor winding temperatures are controlled to the
optimum setpoint. The control accomplishes this by cycling the
motor cooling solenoid valve to allow liquid refrigerant to flow
across the motor windings as needed.
On units equipped with economizers with plate heat exchangers,
a thermostatic valve controls the necessary refrigerant flow entering
this heat exchanger and continuously flowing over the motor
windings. All refrigerant used for motor cooling returns to the rotors
and is compressed to the discharge pressure.
10.7 - Sensors
The units use thermistors to measure the temperature, and pressure
transducers to control and regulate system operation (see 30GX/
HXC - Pro-Dialog Plus Control IOM for a more detailed
explanation).
Содержание 30HXC Series
Страница 49: ......