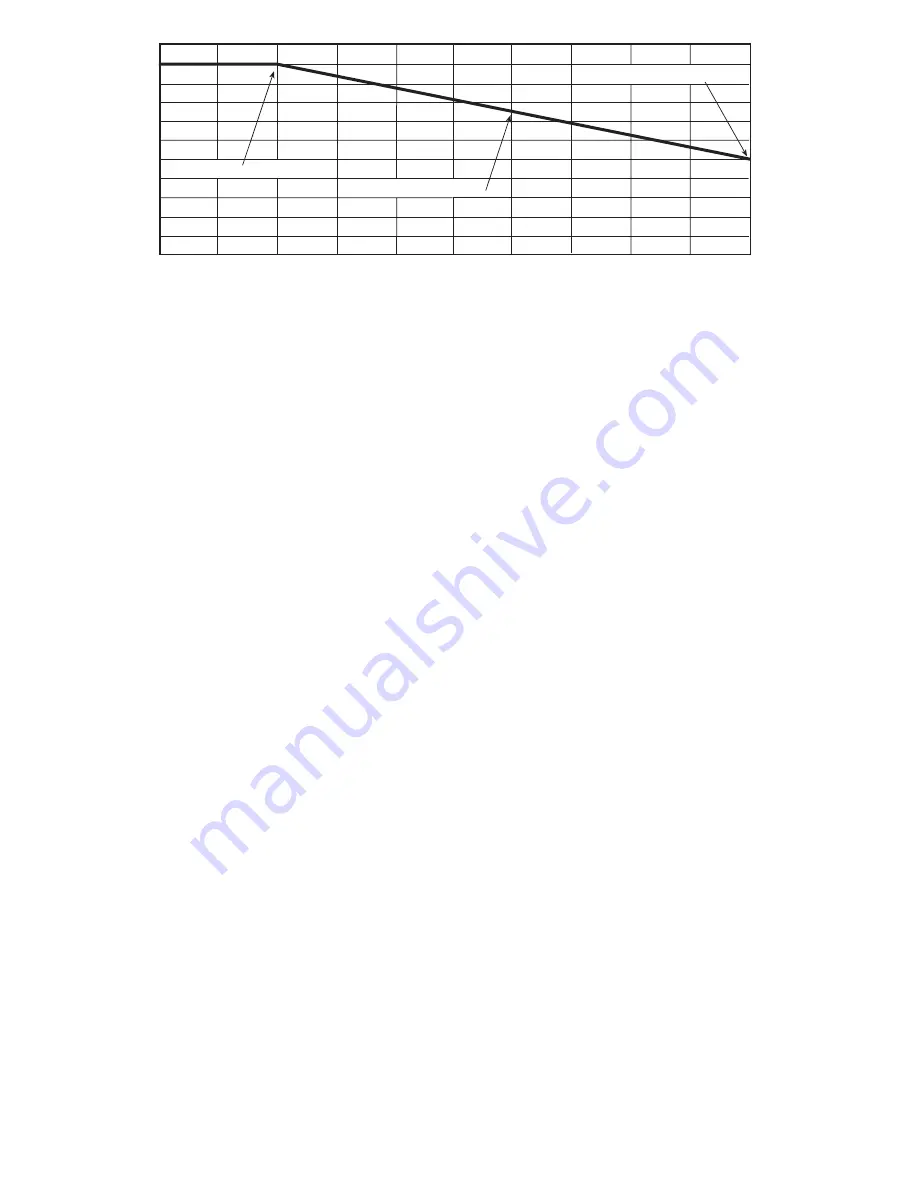
TROUBLESHOOTING
Compressor Protection Control System (CPCS)
Board —
The compressor protection board controls the
compressor and compressor crankcase heater.
The ground current protection is provided by the com-
pressor board.
The large relay located on the board is used to provide a
feedback signal to the Main Base Board.
The operation of the compressor board can be checked
using the Service Test procedure. When the Service Test step
is turned on, the compressor board is energized. All safeties
are continuously monitored. The crankcase heater will be turned
off and the compressor contactor will be turned on. The feed-
back contacts will close and the Main Base Board (MBB)
will read the feedback status.
If the board does not perform properly, use standard wir-
ing troubleshooting procedures to check the wiring for open
circuits. Refer to Alarms and Alerts section on page 45 for
alarm or alert codes for possible causes for failure.
If a compressor short-to-ground exists, the compressor board
may detect the short before the circuit breaker trips. If this
is suspected, check the compressor for short-to-ground fail-
ures with an ohmmeter. The ground current is sensed with a
current toroid (coil) around all 3 or 6 wires between the main
terminal block and the compressor circuit breaker(s).
Compressor Ground Current (CGC) Board
(30GTN,R130-210, 230A-315A, and 330A/B-
420A/B) —
One board is used for each circuit of these
units. Each board receives input from up to 4 toroids wired
in series, one toroid per compressor. With 24 v supplied at
terminals A and B, a current imbalance (compressor ground
current) sensed by any toroid causes the NC (normally closed)
contacts to open, shutting down the lead compressor in the
affected circuit. All other compressors in that circuit shut down
as a result. The NC contacts remain open until the circuit is
reset by momentarily deenergizing the board using the push-
button switch.
If the NC contacts open, it is necessary to remove toroids
from the T1-T2 circuit to determine which toroid is causing
the trip. The chiller circuit can then be put back on line after
the circuit breaker of the faulty compressor is opened. The
compressor problem can then be diagnosed by normal trouble-
shooting procedures.
EXV Troubleshooting —
If it appears that the EXV is
not properly controlling operating suction pressure or super-
heat, there are a number of checks that can be made using
the quick test and initialization features built into the
ComfortLink™ control.
Follow the procedure below to diagnose and correct EXV
problems.
STEP 1 — CHECK PROCESSOR EXV OUTPUTS — Check
EXV output signals at the J6 and J7 terminals of the EXV
board.
Turn unit power off. Connect the positive lead of the meter
to terminal 3 on connector J6 on the EXV board. Set meter
for approximately 20 vdc. Turn unit power on. Enter and
enable the Service Test mode. Locate the appropriate valve
under ‘OUTS.’ Select the desired percentage and press En-
ter to move the valve. The valve will overdrive in both di-
rections when either 0% or 100% are entered. During this
time, connect the negative test lead to terminals 1, 2, 4, and
5 in succession. The voltage should fluctuate at each pin. If
it remains constant at a voltage or at 0 v, replace the EXV
board. If the outputs are correct, then check the EXV.
To test Circuit B outputs, follow the same procedure above,
except connect the positive lead of the meter to terminal 3
on connector J7 on the EXV board and the negative lead to
terminals 1, 2, 4, and 5 in succession.
STEP 2 — CHECK EXV WIRING — Check wiring to EXVs
from J6 and J7 terminal strips on EXV board.
1. Check color coding and wire connections. Make sure that
wires are connected to correct terminals at J6 and J7 ter-
minal strips and EXV plug connections. Check for cor-
rect wiring at driver board input and output terminals. See
Fig. 2-4.
2. Check for continuity and tight connection at all pin
terminals.
3. Check plug connections at J6 and J7 terminal strips and
at EXVs. Be sure EXV connections are not crossed.
STEP 3 — CHECK RESISTANCE OF EXV MOTOR WIND-
INGS — Remove plug at J6 and/or J7 terminal strip and
check resistance between common lead (red wire, terminal
D) and remaining leads A, B, C, and E. Resistance should be
25 ohms ± 2 ohms.
STEP 4 — CHECK THERMISTORS THAT CONTROL EXV
— Check thermistors that control processor output voltage
pulses to the EXVs. Circuit A thermistor is T7, and circuit
B thermistor is T8. Refer to Fig. 9 and 10 for location.
1. Use service test to determine if thermistors are shorted or
open.
2. Refer to Thermistors section on page 57 for details on
checking thermistor calibration.
50% CAPACITY AT 20 mA
75% CAPACITY AT 12 mA
100% CAPACITY AT 4 mA
0
2
4
6
8
10
12
14
16
18
20
DEMAND LIMIT SIGNAL – 4 - 20 mA INPUT (VOLTS DC)
100
80
60
40
20
0
MAX.
ALLOW
ABLE LOAD (%)
Fig. 21 — 4 to 20 mA Demand Limiting
46
Содержание 30GTN
Страница 6: ...Fig 1 Typical Control Box 080 110 and Associated Modular Units Shown 6 ...
Страница 7: ...Fig 2 24 V Control Schematic Unit Sizes 040 070 7 ...
Страница 8: ...Fig 3 24 V Control Schematic Unit Sizes 080 110 230B 315B 8 ...
Страница 9: ...Fig 4 24 V Control Schematic Unit Sizes 130 210 230A 315A 330A B 420A B 9 ...
Страница 75: ......