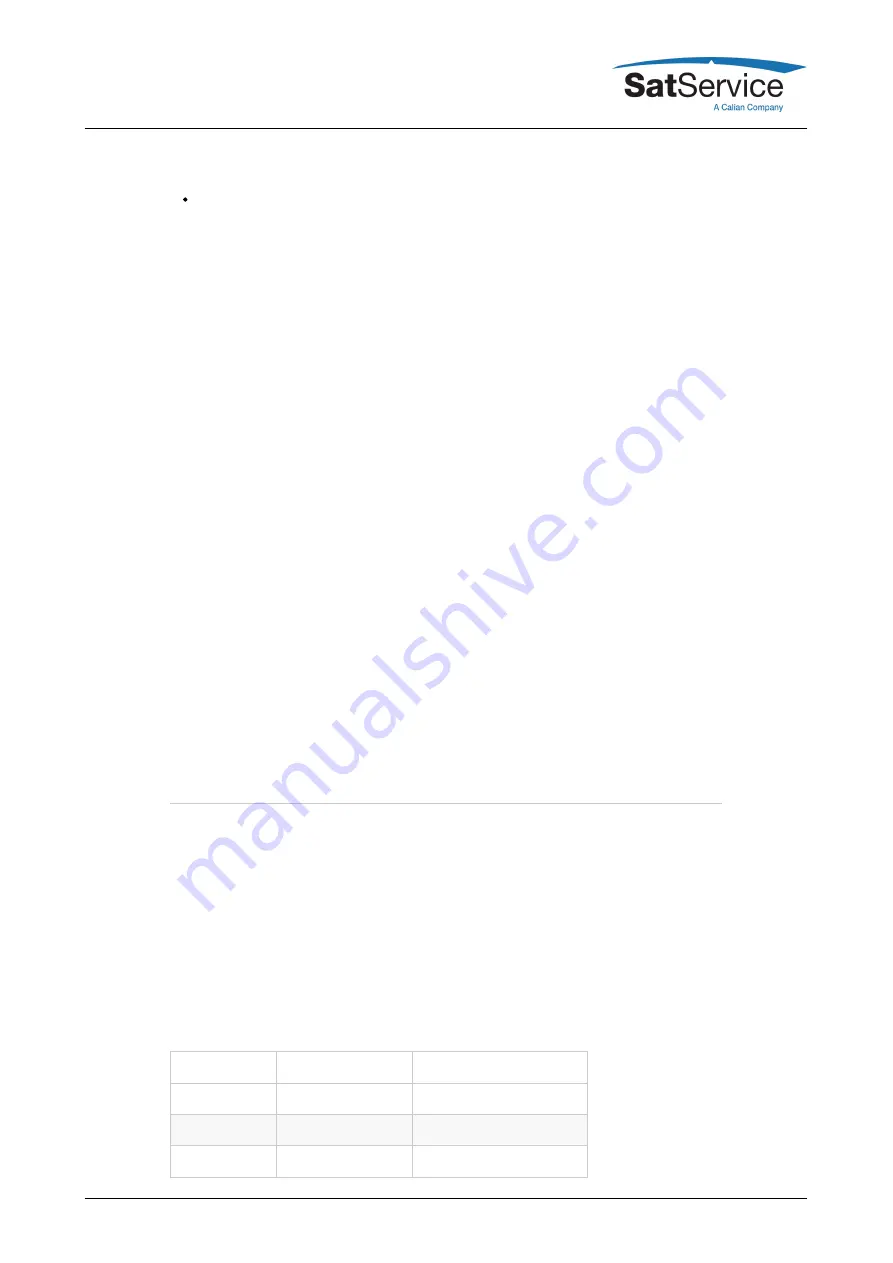
has 16 bit binary resolution.
ANALOG --- For small antennas with reduced accuracy requirements using analog angle to
voltage sensors (in fact precision potentiometers) is an inexpensive alternative. The analog
sensor interface board may be set up for several voltages to connect to the commonly used
sensor types. The analog interface board uses a 16 bit precision ADC with a temperature
compensated voltage reference.
Angle calibration
Analogous to the modular position interface hardware concept, the ACU software uses
configurable drivers to read the different types of position interfaces. From the user's point of
view, the ACU accepts and displays pointing angles as floating point numbers with 0.001??
resolution. Internally the software treats angles as 32 bit integer numbers where the full 32 bit
range corresponds to 360??. This is equivalent to a resolution of 0.000000084??.
When the software calculates the pointing angles from the sensor readings, it includes some
calibration parameters configurable at the
Setup
page. The steps of calculating a pointing angle
are as follows:
1. Get the raw value.
2. Extend (left shift) the value to 32 bits.
3. Reverse the sign if this option is set in the setup.
4. Apply (add) the pre-scale offset.
5. Convert to degrees.
6. If the calibration scale is nonzero, multiply by the calibration scale.
7. Add the post scale calibration offset.
8. For the azimuth axis add the antenna course, too.
The angle calculated this way may exceed a full circle of 360?? if the scaling ensures that there
is no overflow of the encoder reading itself. The value displayed as raw reading at the test page,
is the result of step 2.
The sat-nms ACU performs the pointing / motor control as a closed control loop, independently
for each axis. If the measured position value differs from the target value, the motor is activated to
compensate this difference. It makes no difference if a new target value has been commanded or
if the antenna has moved a little bit due to a squall.
Hysteresis
To avoid that the motor is switched forth and back all the time, the ACU tolerates small differences
between measured and target value within a hysteresis value. This hysteresis is individually
configurable for each axis at the
Setup
page. To ensure that the motor stands still when the target
position is reached, twice the resolution (step size) of the position sensor / encoder must be set.
Common values are:
bit resolution
angular resolution
recommended hysteresis
13 bit
0.044??
0.090??
16 bit
0.005??
0.012??
17 bit
0.003??
0.006??
(C) 2022, SatService GmbH
www.satnms.com
ACU2-19V2-UM-2209 Page 83/99