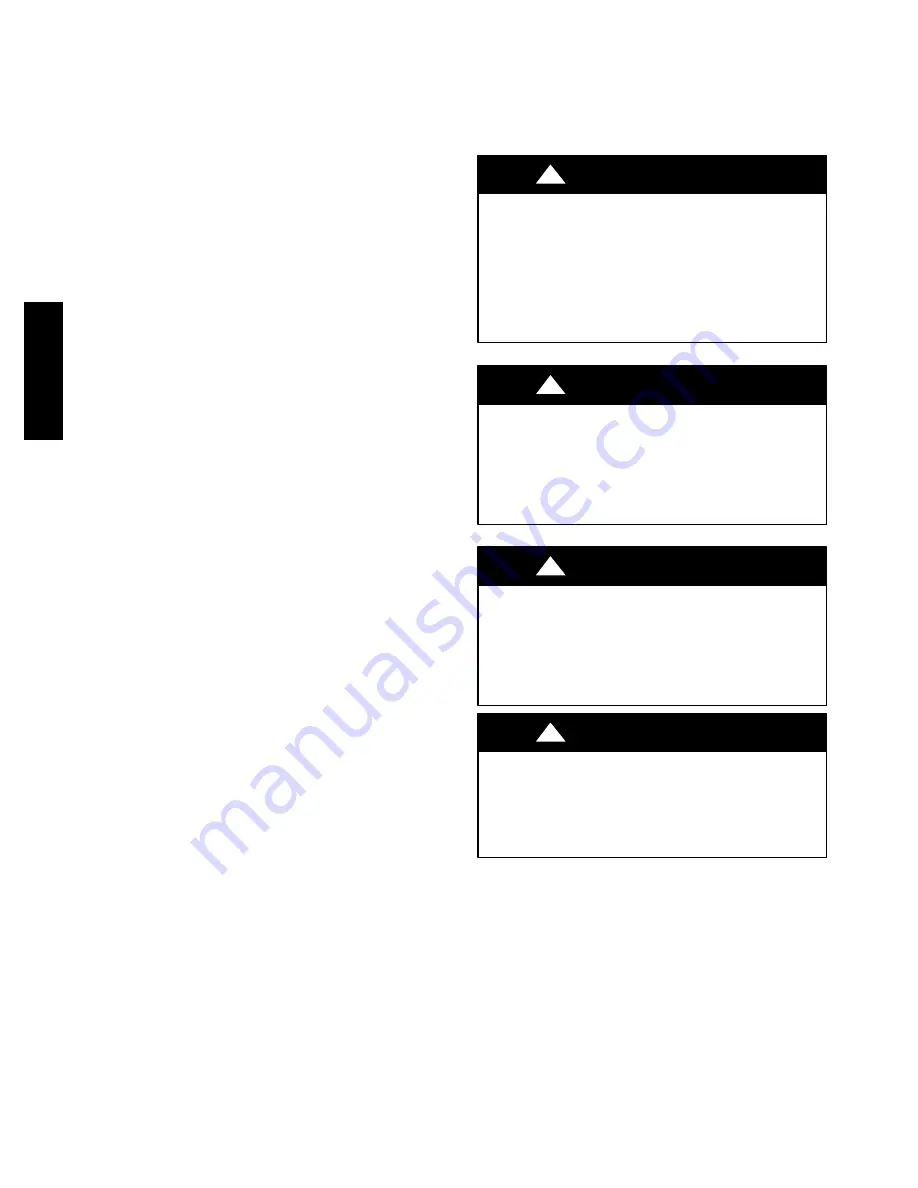
26
the UI. When activated, the following sequence of operation will
occur. Reversing valve will energize and compressor will turn off
for 30 seconds, then turn back on to complete defrost. At the end
of the defrost cycle, the reversing valve de--energizes, compressor
will turn off for another 30 seconds, and the fan will turn off for 40
seconds, before starting in the heating mode.
DEHUMIDIFICATION MODE
This Evolution system can be used to dehumidify the living space.
See User Interface Installation Instructions for more details.
SEQUENCE OF OPERATION--GAS HEAT
NOTE
: Evolution control must be grounded for proper operation
or control will lock out.
NOTE
: If a power interruption occurs during a call for heat, the
control will start a 90--second blower--only ON period two seconds
after power is restored, if the UI is still calling for gas heating. The
amber LED light will flash code 12 during the 90--second period,
after which the LED will be ON continuously, as long as no faults
are detected. After the 90--second period, the unit will respond to
the UI normally.
GAS HEAT MODE AND ADJUSTMENTS
When the UI calls for gas heat, the Evolution furnace board
performs a self--check, verifies the pressure switch is open, and
starts the inducer on high speed.
1. Inducer Pre--purge Period: When the inducer motor comes
up on high speed, the pressure switch closes, and the
Evolution ignition control on the furnace board begins a 15
second pre--purge period. If the pressure switch fails to
remain closed, the inducer will remain running. After the
pressure switch re--closes, the Evolution ignition control
will begin a 15 second pre--purge period.
2. Trial--For--Ignition Sequence: The spark igniter will spark
for 3 seconds. The main gas valve relay contact closes to
energize the gas valve on low stage. After 5 seconds, the
igniter is de--energized and a 2--second flame--proving
period begins. NOTE: The unit always lights on high
speed inducer and low stage gas valve operation.
3. Flame--Proving: When the burner flame is proved at the
flame--proving sensor, the furnace control determines what
heating stage to run based on feedback from the UI. If the
UI is asking for low stage gas heat, the ignition control will
change the inducer speed to low speed and keep the gas
valve energized on low stage. If the UI is asking for high
stage gas heat, the ignition control will maintain running the
inducer on high speed and energize the gas valve’s high
stage relay to increase gas flow.
If the burner flame is not proved within 2 seconds, the control will
close the gas valve and repeat the ignition sequence up to 3 more
Trials--For--Ignition before going to Ignition--Lockout. Lockout
will reset automatically after 3 hours, by momentarily interrupting
230 VAC power, or by interrupting 24 VAC power at SEC1 or
SEC2 to the furnace board.
If flame is proved when there should be no flame present, control
will lock out of Gas--Heating mode and operate the inducer motor
until flame is no longer proved.
4. Blower--On Delay:
If the burner flame is proven,
approximately 37 seconds after the gas valve is opened the
Indoor Blower is turned on to the appropriate speed for the
gas heating stage.
Simultaneously, the humidifier terminal HUM and electronic air
cleaner terminal EAC--1 are energized throughout the heating
cycle.
NOTE
:
EAC--2 terminal is common with L2 and will have
115VAC--to--ground when unit is powered.
5. Blower--Off Delay: When the call for gas heat is satisfied,
the gas valve is de--energized, stopping the flow of gas to
the burners, and de--energizing the HUM terminal. The
inducer motor will remain on for a 4--second post--purge
period. The indoor blower and air cleaner terminal EAC--1
will remain energized for 90, 120, 150, or 180 seconds
(depending on selection of blower--off delay selected in the
UI). The factory--set default is 120--second blower--OFF
delay.
CHECK GAS INPUT (NATURAL GAS)
UNIT DAMAGE HAZARD
Failure to follow this caution may result in component
damage.
Do not
redrill an orifice. Improper drilling (burrs,
out--of--round holes, etc.) can cause excessive burner noise
and misdirection of burner flame. If orifice hole appears
damaged or it is suspected to have been redrilled, check
orifice hole with a numbered drill bit of correct size.
!
CAUTION
FIRE HAZARD
Failure to follow this warning could result in personal
injury, death and/or property damage.
DO NOT bottom out gas valve regulator adjusting screws.
This can result in unregulated manifold pressure and result
in excess overfire and heat exchanger failures.
!
WARNING
CARBON MONOXIDE POISONING HAZARD
Failure to follow this warning could result in personal
injury, death and/or property damage.
If the manifold pressure and/or gas rate is not properly
adjusted on HI and LO stages, excess carbon monoxide can
be produced.
!
WARNING
FIRE AND UNIT DAMAGE HAZARD
Failure to follow this warning could result in personal
injury or death and/or property damage.
Unsafe operation of the unit may result if manifold pressure
is outside of the ranges listed in Table 6.
!
WARNING
Gas input rates on rating plate are for installations at altitudes up to
2000 ft (610 m). Input rate must be within
±
2% of rating plate
input.
1. Determine the correct gas input rate.
a. The rated gas inputs shown in Table 3 are for altitudes
from sea level to 2000 ft (610 m) above sea level.
These inputs are based on natural gas with a heating
value of 1025 Btu/ft3 at .60 specific gravity.
IN THE U.S.A.:
The input rating for altitudes above 2,000 ft (610 m) must be
reduced by 4 percent for each 1,000 ft (305 m) above sea level.
For installations below 2,000 ft (610 m), refer to the unit rating
plate.
677D
--
--
A
Содержание 677D--A
Страница 5: ...5 A09561 Fig 5 677D A24 30 Unit Dimensions 677D A...
Страница 6: ...6 A09562 Fig 6 677D A36 60 Unit Dimensions 677D A...
Страница 18: ...18 A10217C Fig 17 Connection Wiring Schematic 677D A Single Phase Gas Inputs 040 060 090 kBtu hr 677D A...
Страница 19: ...19 A10217L Fig 16 Cont Ladder Wiring Schematic 677D A Single Phase Gas Inputs 040 060 090 kBtu hr 677D A...
Страница 20: ...20 A10219C Fig 18 Connection Wiring Schematic 677D A Single Phase Gas Inputs 115 130 kBtu hr 677D A...
Страница 21: ...21 A10219L Fig 17 Ladder Wiring Schematic 677D A Single Phase Gas Inputs 115 130 kBtu hr 677D A...