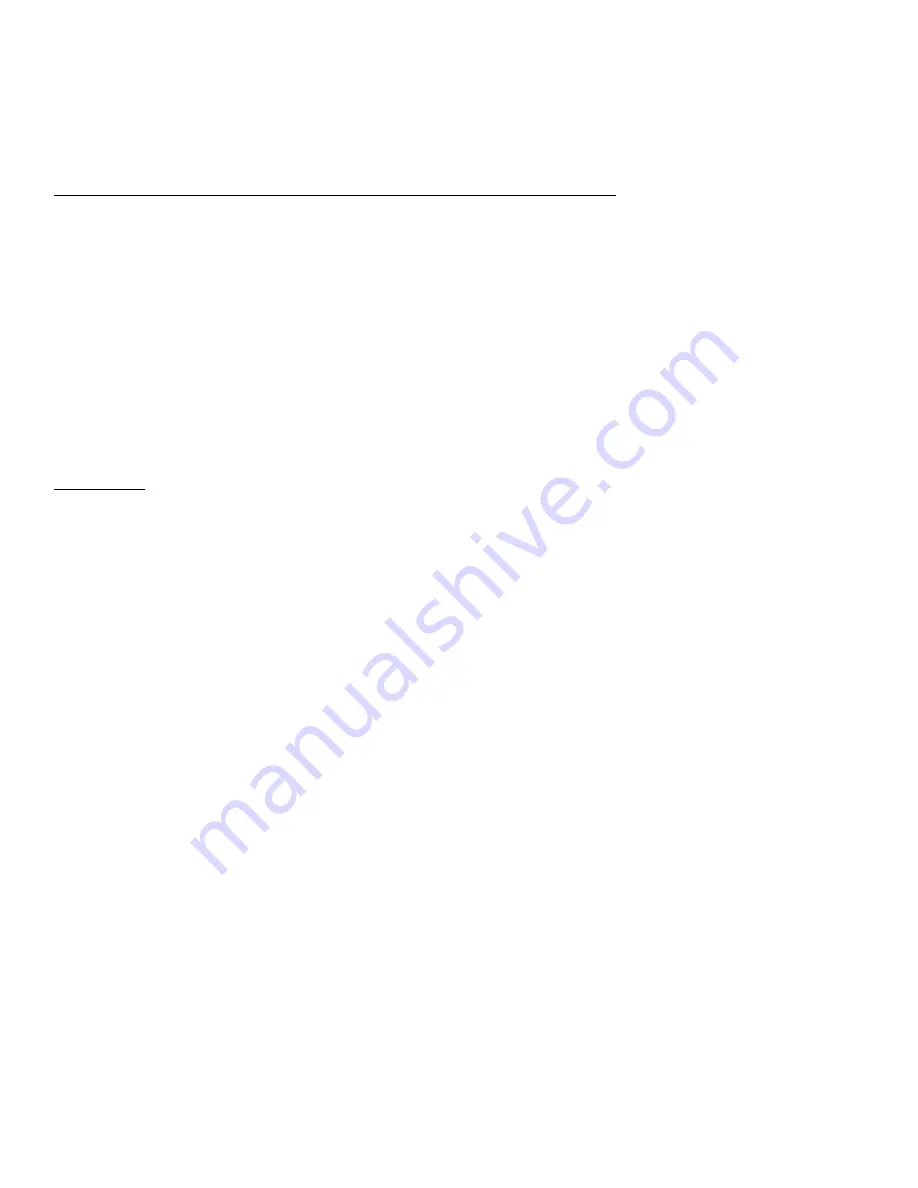
CONDENSING SECTION
SYSTEM CHARGING (DEHUMIDIFIERS WITH CONDENSING UNITS):
The factory installed condensing units are shipped fully charged. The condensing units are pumped down and all
service valves closed prior to shipment. All service valves must be opened before the condensing units may be
operated. Be careful not to over-tighten the valves or damage to the seat and packing gland may result and the valve
may leak refrigerant.
If the condensing unit is supplied with a crankcase heater, power should be supplied to the condensing unit for at
least 5 hours before the condensing unit is put into operation. This will evaporate any liquid refrigerant that may
have condensed in the compressor crankcase.
Compressor shipping hold down bolts (spring mounted compressors) should be loosened until compressor
swings free on its isolators.
START-UP:
This is a continuation of the "system charging" and must be performed before condensing unit(s) may be left
operating and unattended. This will involve checking and adjusting of all safety and operating controls (pressure
and temperature controls have been set at factory, however; it is still desirable to confirm that settings are correct
and controls function properly). Do not attempt to reset safety controls without some means of stopping the
equipment in the event of extreme high or low pressure/temperature conditions that could damage the equipment. If
controls fail to function at set points, determine cause and correct.
(Jumping or bypassing any safety control
other than for testing purposes is dangerous to personnel and equipment, and nullifies the equipment
warranty)
.
NOTE:
a qualified technician should perform Adjustments to the refrigeration equipment.
High-pressure control
- connect a gauge to the compressor discharge service valve. Stop condenser
airflow by stopping fans on air-cooled equipment. Control should open immediately when discharge
pressure reaches control set point.
Low pressure (Pump-down) control
- connect a gauge to the compressor suction service valve.
Throttle liquid line service valve to lower suction pressure at the compressor. Compressor should
pump-down and de-energize when suction pressure reaches "cut-out" setting of control. Open liquid
line service valve and observe rise in pressure at compressor suction connection. Compressor should
be energized when pressure reaches "cut-in" setting of control.
Oil pressure control (if applicable)
- connect the wires between terminals T1 and T2. Compressor
should run approximately 90 seconds and cycle off. Remove jumper and reset control. Check
operating oil pressure. This is the differential between oil pump discharge pressure and suction
pressure and should be a minimum of 10 psig. Also, after several hours running time, check oil level
in compressor. Proper level is approximately 1/4 level on oil sight glass.
Thermal expansion valve
- Check super-heat setting and adjust if necessary. The amount of super-
heat is found by measuring the temperature and the pressure of the suction gas at the leaving side of