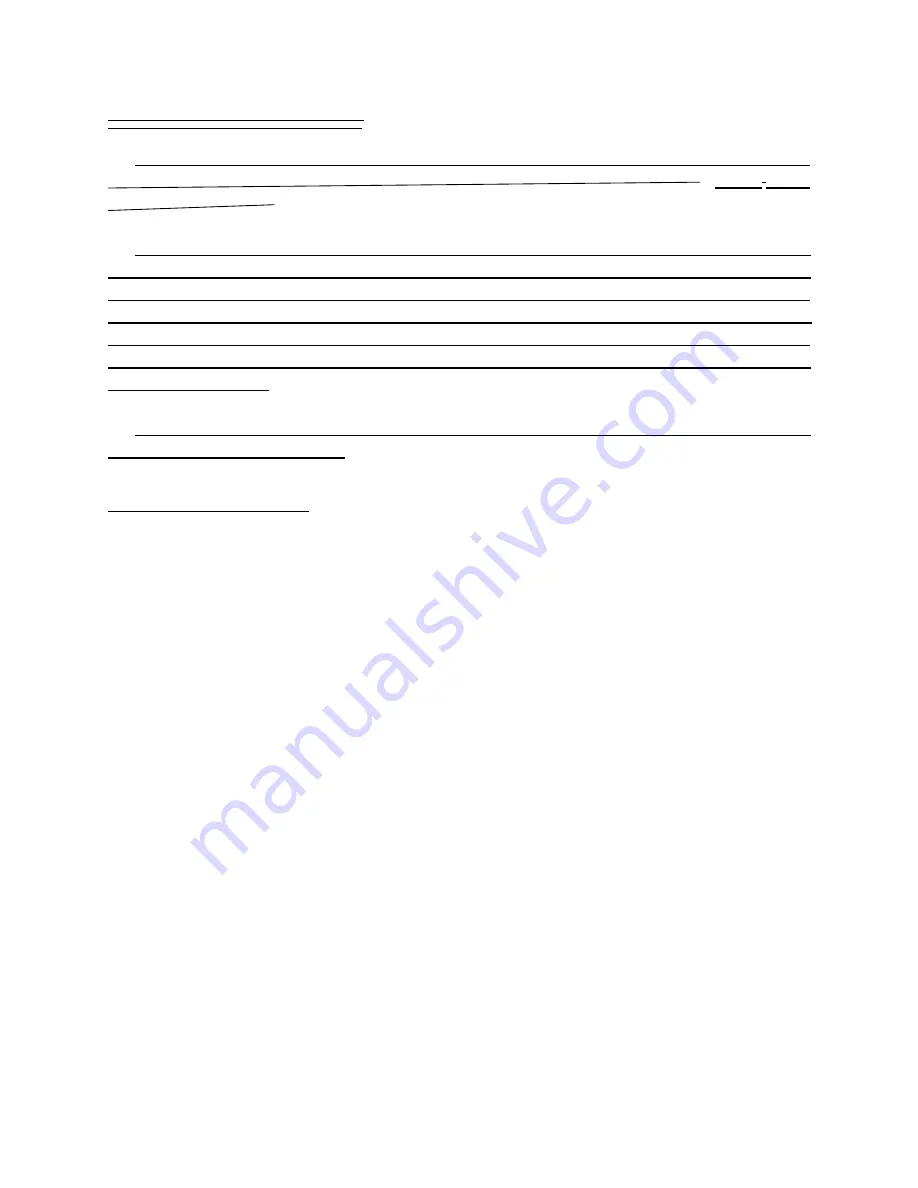
- 14 -
FAN BEARING MAINTENANCE:
For most applications, lithium base grease conforming to NLGI grade 2 consistency should be used.
This type of grease inhibits rust, is water resistant, and has a temperature range of 30
°
F to 200
°
F with
intermittent highs of 250
°
F.
When greasing bearings it is important not to over-grease. This is especially true if the bearings are
equipped with extended grease lines and the bearings are not visible. In this case, more bearing failures
occur due to over-greasing than under-greasing. It is best to give the bearing just one "shot" of grease
periodically, when the bearings are not visible. When the bearings are visible, pump in grease until a small
bead of grease forms around the bearing seals. It is very important that fan bearing greasing take place
while the fan is operating.
Caution should be taken while working on or near rotating equipment to
avoid personal injury
.
When oiling oil-lubricated bearings, oil should be poured into cup at top of bearing until it reaches the
overflow point at the lower oil cup.
MOTOR MAINTENANCE:
Lubricate motor bearings to the manufacturer's recommendations. Lubrication recommendations are
printed on tags attached to the motor. Should these tags be missing, the following will apply:
A. Fractional Horsepower Sleeve Bearing Motors:
Under normal operation at ordinary temperatures and clean surroundings, these motors will operate for
three years without re-lubrication. Then lubricate annually with electric motor oil or SAE 10 oil. Under
continuous operation at higher temperatures (but not to exceed 104
°
F ambient) re-lubricate annually.
B. Fractional Horsepower Ball Bearing Motors:
Under normal conditions, ball bearing motors will operate for five years without re-lubrication. Under
continuous operation at higher temperatures (but not to exceed 104
°
F ambient) re-lubricate after one
year. To re-lubricate where motors are not equipped with pressure fittings, disassemble motor and
clean the bearings thoroughly. Repack each bearing one-third full with ball bearing grease.
C. Integral Horsepower Ball Bearing Motors:
Motors having pipe plugs or grease fittings should be re-lubricated while warm and at a standstill.
Replace one pipe plug on each end shield with grease fitting. Remove other plug for grease relief. On
low pressure, grease, run, and lubricate until new grease appears at grease relief. Allow motor to run for
ten minutes to expel excess grease. Replace pipe plugs. Motors not having pipe plugs or grease fittings
can be re-lubricated by removing end shield, cleaning grease cavity and refilling three-fourths of
circumference of cavity.