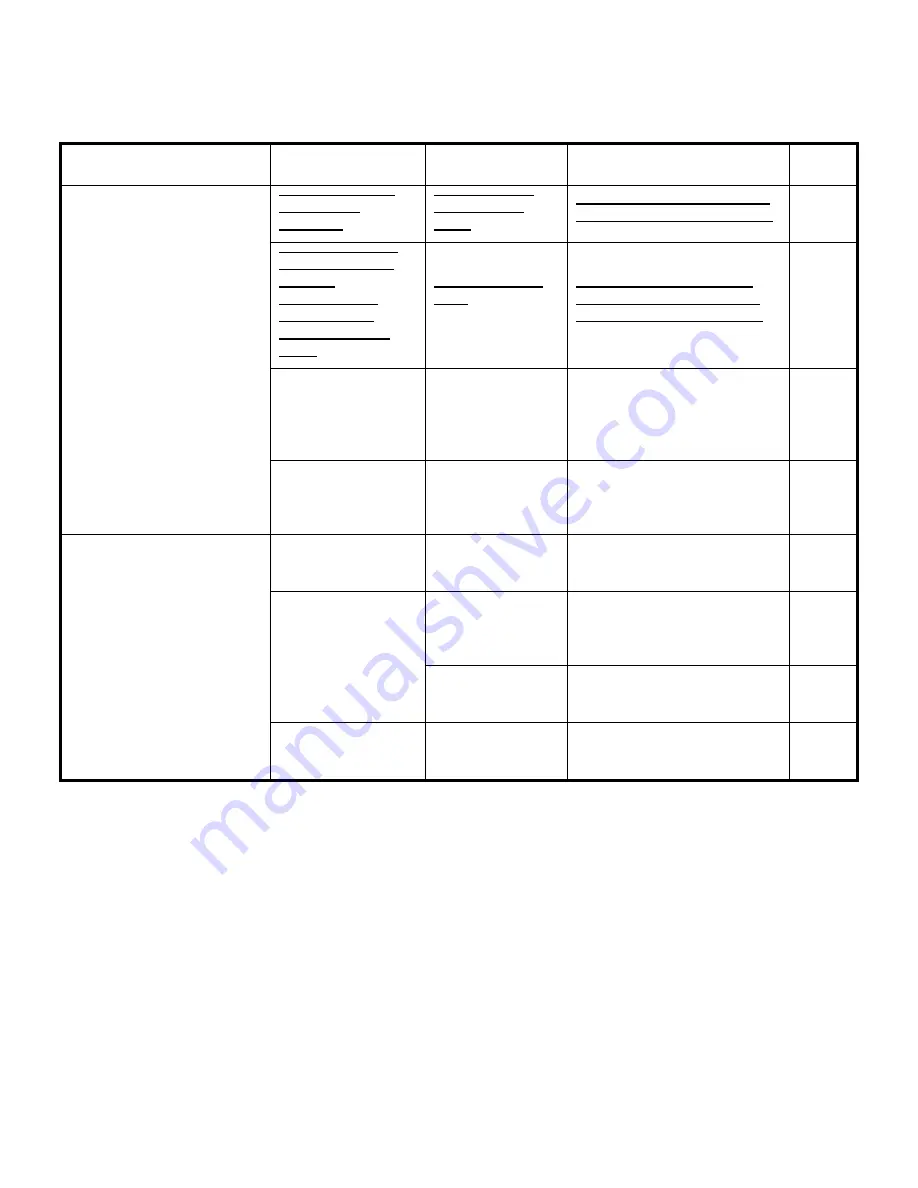
TROUBLE SHOOTING GUIDE FOR UNITS WITH DX COOLING
11
Complaint
Symptoms
Probable Cause
Recommended Action
Ref.
Note
1. Excessively cold
water leaving
condenser.
Too much or too
cool condenser
water.
Adjust water regulating valve or
cooling tower thermostat setting.
2. Cooling tower (if
used) appears to be
operating
satisfactorily yet
excessively low
discharge pressure
exists.
Cooling tower too
large.
Recheck cooling tower rating
table for correct size selection.
Adjust cooling water flow rate.
3. Compressor short
cycles.
Air-cooled
condenser operating
with low
temperature outdoor
air.
Consider controlling condensing
temperature with condenser
discharge air dampers or fan
control.
H. Discharge pressure too low.
4. Suction pressure
rises faster than 5psi
per minute after
compressor shutdown.
Leaky or broken
compressor
discharge valves.
Remove head, examine valves
and replace, as necessary.
1. Compressor runs
continuously.
Excessive load on
evaporator.
Check outdoor air dampers for
excessive intake of high
temperature ventilation air.
a. Expansion valve
overfeeding.
a. Regulate superheat setting of
expansion valve and check to see
that remote bulb is properly
attached to suction line.
5
2. Abnormally cold
suction line. Liquid
flooding back to
compressor.
b. Expansion valve
stuck in open
Position.
b. Repair or replace valve.
J. Suction pressures too high.
3. Noisy compressor.
Broken suction
valves in
compressor.
Remove head; examine valves
and replace, as necessary.
4