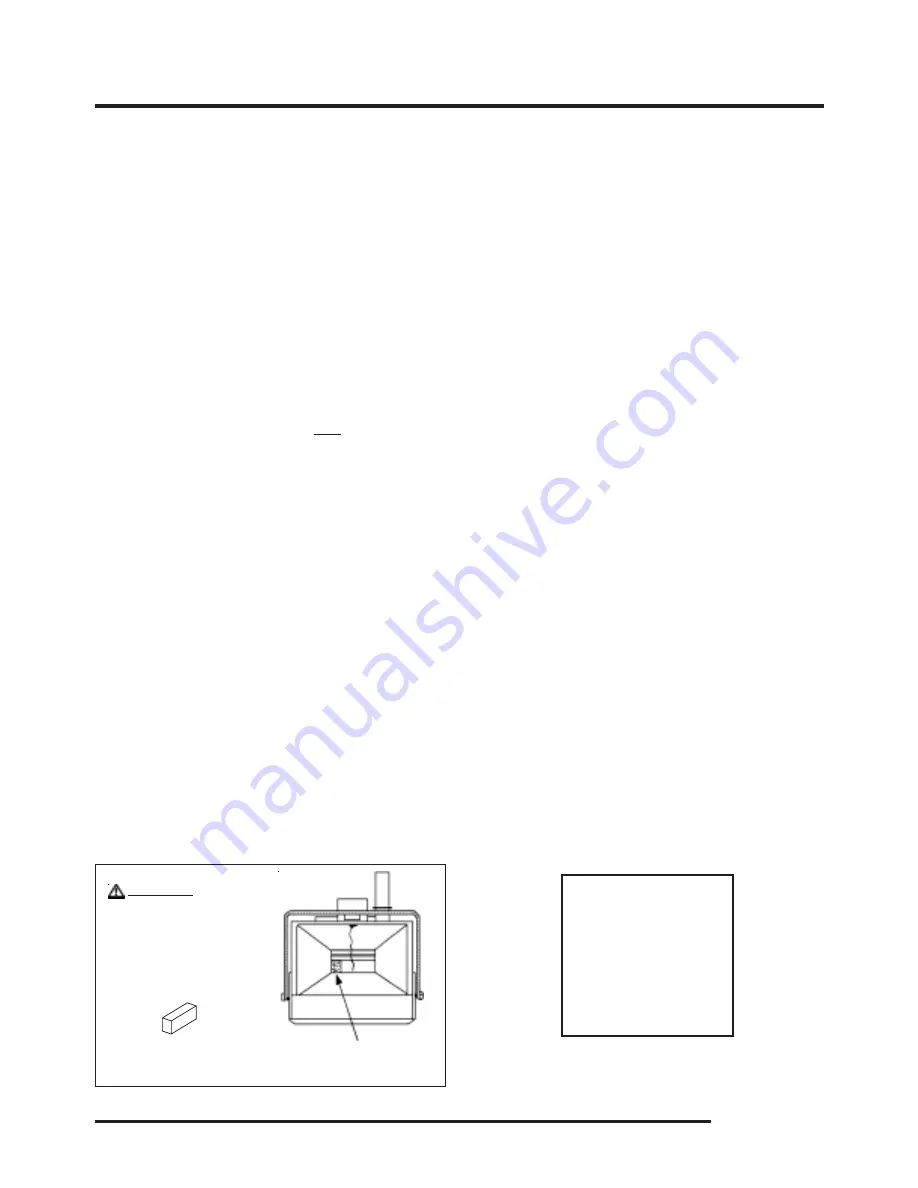
Bandit
PRINTED 4/02
PAGE 33
MODELS 65A & 65AW
MAINTENANCE SECTION
DAILY MAINTENANCE (cont.)
9) Check air cleaner or precleaner, clean or
replace as necessary:
Clean or replace element following engine manual
recommendations.
10) Check hydraulic oil level:
In the hydraulic oil reservoir tank the level should
always remain at 7/8 full.
11) Check for any oil, or fuel fitting leaks:
Inspect for any oil, fuel, hydraulic oil, or engine
coolant leaks. Check all hoses, fittings, lines, tanks,
repair or replace.
12) Grease all feedwheel, and chipper bearings
daily:
Use an EP-2 Lithium type grease only for all bearings.
13) Check clutch:
Check for proper lubrication, and engagement tension
adjustment, frequently adjust and lubricate per PTO
clutch manufacturers manual. Bandit Industries Inc.
does not warranty clutch failures.
14) Check the safety decals and engine gauge:
Replace if missing or damaged. Check the engine
manufacturer’s manual to make sure your chipper
engine is running properly.
15) Check Knife Bolts:
All knife bolts and nuts must be of premium quality,
and meet all SAE standards for “Grade 8” hardness.
Bolts and nuts must be replaced after a maximum of
4-5 knife rotations/changes to insure safe clamping
ability. Torque set to 70-80 ft./lbs. AT ALL TIMES.
16) Inspect/replace axle dust caps:
Grease axles per axle MFG. manual. Inspect and
adjust brakes as needed per axle MFG. manual.
17) Check Chipper disc assembly:
Cehck for elongated bolt holes, secure welds, torqued
bolts, excessive wear, and impact cracks. If a
problem is found, contact chipper manufacturer.
WEEKLY MAINTENANCE
1) Check anvil clearance, tightness, and wear:
Measure the anvil clearance at the top and bottom of
the knife anvil by using a feeler gauge, the clearance
should be .045 to .065 from highest knife. Check the
anvil hardware, make sure the bolts are at the proper
tightness. The anvil is a normal wear item, if it is worn
you can rotate it to a new working edge. Always
remove yoke springs, and use a top wheel block, lock
pin, and safety chain when working inside infeed
hopper area. Always use sight slot to see if belts are
stopped before servicing.
2) Check alternator and fan belts on engine (as
applicable):
Adjust and maintain per the engine manufacturer’s
manual.
3) Check spring tension on feedwheel system:
Do not over tighten. Keep tight for small diameter
material and progressively looser for larger diameter
material.
4) Check and retighten fuel tank mount bolts:
Check the hydraulic tank mount bolts also at this
time.
5) Check wheel lug nuts:
Keep lug nuts tight, retorque, replace if needed.
AE-10
MICRON
FILTER
WOODEN BLOCK TO
HOLD FEEDWHEEL UP
DANGER
WHEN WORKING INSIDE
THE INFEED HOPPER
AREA, ALWAYS REMOVE
YOKE SPRINGS, INSTALL
LOCK PIN, HOOK UP
SAFETY CHAIN, AND
INSERT BLOCK.
APPROXIMATE
2” X 8” X 12”
WOODEN BLOCK
Содержание 65A
Страница 2: ......
Страница 3: ......
Страница 4: ......
Страница 5: ......
Страница 6: ......
Страница 7: ......
Страница 8: ......
Страница 9: ......
Страница 10: ......
Страница 11: ......
Страница 12: ......
Страница 13: ......
Страница 14: ......
Страница 19: ......
Страница 60: ...SERVICE RECORD DATE DESCRIPTION AMOUNT Bandit PRINTED 4 02 PAGE 46 MODELS 65A 65AW REPLACEMENT PARTS...
Страница 62: ...Bandit PRINTED 4 02 PAGE 48 MODELS 65A 65AW INFEED HOPPER COMPONENTS 21...
Страница 68: ...Bandit PRINTED 4 02 PAGE 54 MODEL 65A FRAME ACCESSORY COMPONENTS 10 11...
Страница 70: ...Bandit PRINTED 4 02 PAGE 56 MODEL 65AW FRAME ACCESSORY COMPONENTS 8 7...