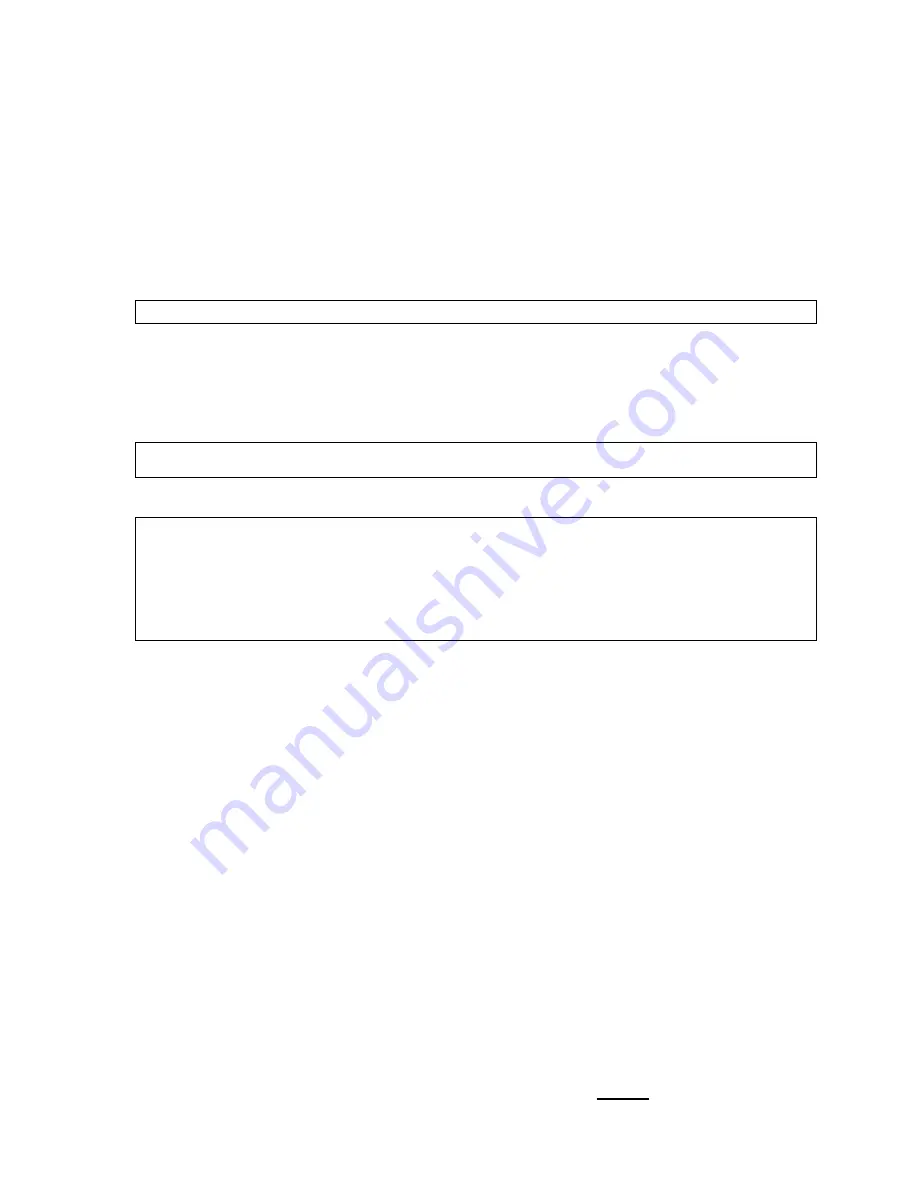
5
2.3 Splitting Internal Model Heaters
The SP5 & SP6 Internal model heaters can be split for ease of installation. To split the heater, follow these simple instructions:
• Remove the heater’s roof after removing the 4 roof screws.
• Disconnect the speed sensor loom from the control board and remove it from the heat exchanger cabinet.
• Remove the main fan motor and speed sensor loom access plate located on top of the fan cabinet
compartment by removing the single screw.
• Unplug the main fan loom at the connection located inside the access hole which has just been uncovered.
• Remove the 2 screws fastening the fan cabinet tabs to the heat exchanger cabinet. These are located at the
top of the fan cabinet on the heater’s split line.
• Pivot the fan cabinet upwards high enough to dislodge the lower locking tabs fixed to the fan cabinet near the base.
• The heater is now split in two.
• Protect the exposed looms and tabs from damage while the heater is split in two parts.
• Once ready, reassemble in reverse order.
Note:
Ensure when reassembling the heater that everything is put back and connected correctly.
2.4 Changing the Return Air Pop Orientation
The return air pop orientation can be changed from side to side or to the rear of the heater if necessary.
Reversing the Side Entry
• Remove the screws securing the side pop blanking plate and remove the blanking plate.
• Swap to the other side and fasten with the same screws.
Changing to Rear Entry
Note:
If this is done, predominantly when a unit is laid down, then the total number of outlets normally permitted for
that installation must be reduced by 2 (refer to the outlet register chart located on page 20).
• Remove the screws securing the end pop blanking plate and remove the blanking plate.
• Swap to the open side and fasten with the same screws.
IMPORTANT NOTE – RETURN AIR CONNECTION AT THE END OF THE UNIT (REAR ENTRY)
On applicable models, connecting the Return Air duct to the end of the unit (rear entry) will result in reduced air
flow – for example, when using a Brivis Lay Down Kit. In this situation:
– The total number of outlets normally permitted for a heating system shall be reduced by 2 (refer to the outlet
register chart located on page 20).
– DO NOT USE this configuration in Add-On Cooling applications, unless you ensure Minimum Recommended
Airflow required for the cooling is maintained.
2.5 Internal Model Flueing Instructions – StarPro Series
2.5.1 General
• All flues must be installed in accordance with AS 5601.
• Horizontal flues must have a minimum rise of 20mm per 1m run.
• Horizontal flues terminating on a wall must be at least 300mm above ground level.
• An external flue terminal clearance to an opening in a building shall be no less than 1000mm in the vertical
direction and 300mm in the horizontal direction.
• Systems with both vertical and horizontal flue runs should be treated as all horizontal.
• 1 x 45º bend is equivalent to 0.5 x 90º bend (i.e. 2 x 45º bends = 1 x 90º bend).
• Provide adequate support to flue sections (e.g. saddles / strapping).
2.5.2 SP4 & SP5 Internal Models – 100mm non-corrosive metal flue.
• Requires a 100mm round single or twin wall non-corrosive metal flue, suitably terminated.
• All flues must have a bolted flue sleeve connection to allow for repairs and/or removal of the appliance.
• Twin Wall flue - maximum flue length of 6m.
• Single Wall flue - maximum flue length of 2m.
• Up to 4 x 90º elbows are permitted with the same length requirements specified above.
2.5.3 SP6 Internal Models – 100mm DWV flue
All SP6 internal model heaters are supplied with a Level Invert Taper (LIT) fitting and flue connection to unit is with
100mm Drain Waste Vent pipe (DWV to AS/NZS 1260).
Flue must be installed in accordance with the following:
• Exit heater with a minimum 300mm straight run of 100mm DWV flue before the first elbow.
• All flue joints must be adequately sealed to prevent condensate leakage.
• Ensure there is continual fall back to the flue outlet on the heater from flue termination point.
• Flue must be removable from the heater to allow for repairs and/or removal of the appliance.
• Flat side of the LIT (not tapered side) must be positioned so it is always the lowest part of the fitting or the
closest point to ground.
If a lay down kit is used the LIT must be rotated to ensure the flat side
of LIT fitting is closest to ground, refer Diagram 6.
324702 CAAB024953 StarPro Installers Heat issue D.indd 8
17/05/16 8:41 AM