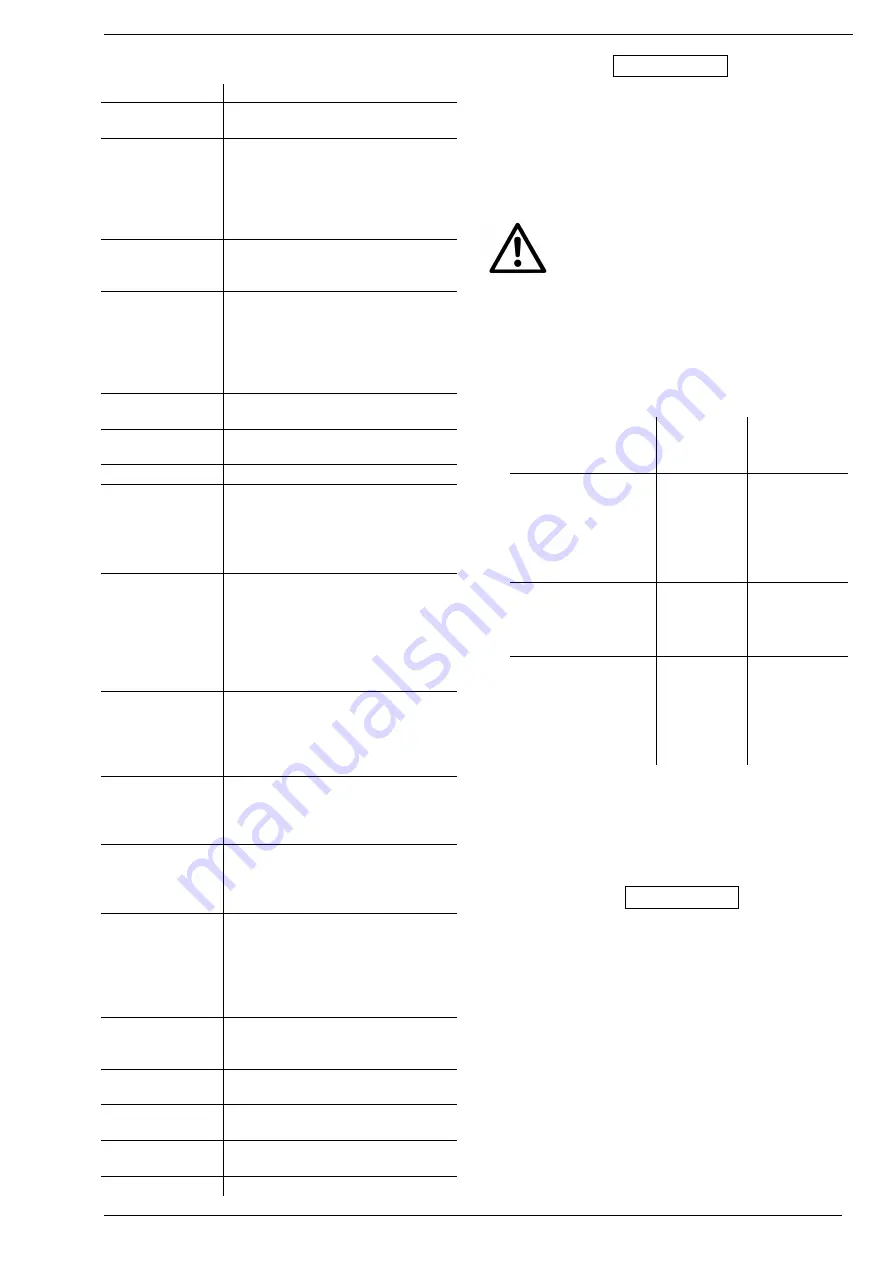
BE6100
Edition 08/2018
Page 3 of 13
2.6 Limit of Application
ATTENTION
The pumps are to be operated within their design
limits. Applications outside of these limits are not
approved. The manufacturer is not responsible for
any damages resulting from use of the pumps in
such applications.
2.7 Important instructions for screw pumps
Never allow screw pumps to run dry!
Incorrect rotation will lead to pump
damage!
Sufficient fluid supply must always be
ensured!
Large particles in the coolant fluid may
damage the screw pump!
The limits for size and concentration of
foreign particles depends on their hard-
ness!
Materials
Particle
size
Particle
concentra-
tion:
Steel / Forgeable
aluminium alloys
(without Si content)
/ GG25
BFG, FFG, BFS,
FFS
< 60
m
< 177 mg/l
Grey cast iron with
hard additives
(e.g. GGV)
BFS, FFS
< 50
m
< 63 mg/l
Ceramic/ corun-
dum / hard metal /
glass / CBN Alu-
minium alloy with
Si parts
BFS, FFS
< 20
m
< 19 mg/l
The particle concentration refers to standard-
ized test.
For additional information please refer to the
filtration diagram in the screw pump catalogue.
ATTENTION
If high pressure screw pumps are to be used
outside of the recommended ranges, a suitable
filter system (e.g. filter bags) must be installed
upstream from the pump or pumps with special
features must be used (e.g., with coated spin-
dles).
If pump failure is caused by excessive wear due
to foreign particles, the warranty is void!
In applications where hard or abrasive particles
are present, the use of coated spindles is highly
recommended.
2.8 Technical data
Detailed technical data can be found in the
screw spindle pump catalogue.
Type
BFS, TFS, FFS
Mediums
Oils, cooling / cutting oils
coolants
Max. delivery
pressure
60 bar (BFG, FFG with cast iron
spindle housing)
150 bar (200 bar for BFS/FFS1,
BFS/FFS2 and TFS/BFS/FFS3
upon request)
120 bar (-H)
Minimum dis-
charge pressure
Ensure that the discharge pressure
is at least 2 bar higher than the
inlet pressure
Minimum inlet
pressure
In order to pre-
vent damage
from cavitation
0.8 bar absolute, with increased
fluid temperature also more,
(Pumps with a flow rate of greater
than 800 l/min have to be operated
in conjunction with a feed pump >
1 bar).
Kinetic viscosity
of the medium
1...45 mm
2
/s (cSt)
higher viscosities upon request
Max. temperature
of medium
60 °C
over 60 °C on request
Max. air content
3
– 5 vol. %
Max. inlet pres-
sure with
me-
chanical seal
Execution -G4
< 7 bar
20 bar
Concentration of
coolant lubricants
and water soluble
coolants
The fluid must have a minimum
lubricity in accordance with indus-
try standards. This corresponds to
an approx. 4% concentration
equivalent to mineral oil. A labora-
tory analysis is available at the
factory.
Minimum flow
rate
The minimum flow rate must be
large enough to protect the pump
from overheating. If necessary,
consult with the manufacturer on
exact flow rate.
Minimum rpm
25 Hz (1500rpm), lower rpm are
available upon request. The mini-
mum rpm depends on the pressure
and medium.
Dry running
The pump MUST never be run dry
without fluid. When testing for the
direction of rotation, bump the
pump for not longer than 1 second.
Cycle times per
hour
Motors less 3 kW max. 200
from 3 kW to 4.0 kW max. 40
from 5.0 kW to 9.0 kW max. 20
from 10 kW to 22 kW max. 15
Increased cycle times are available
upon request.
Maximum fluid
velocity at pump
suction
2 m/s
Installation
positions
(Pump must not be installed with
motor facing down)
Piping / Fittings
Pay attention to max. pressure
ratings
Ambient tempe-
rature
40 °C
Set-up altitude
1000 m