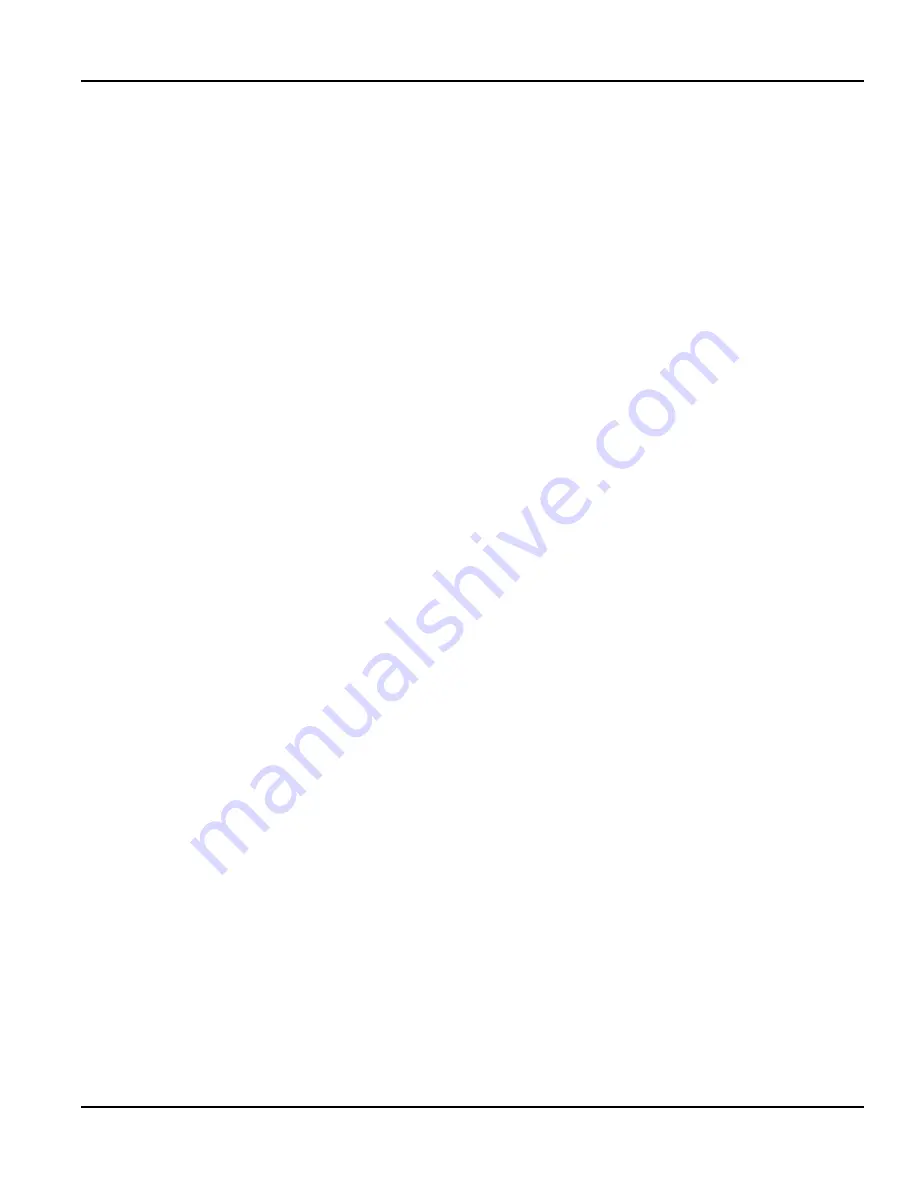
Classic Circular 36"/54" Washfountain with Foot Control
Installation Instructions
WF2605, WF2608 Terrazzo — WF2705, WF2708 Stainless Steel
Bradley Corporation • 215-603 Rev. M; EN 06-915B
17
4/6/2007
Soap Recommendations and Maintenance Tips
Quality soap dispensers require good quality soap and periodic maintenance to properly operate. Bradley
soap dispensers will provide dependable, consistent operation over the long term when soap with
reasonable viscosity and pH levels are used and when a minimal amount of periodic maintenance is
performed on the valves.
Soap thickness is determined by a measurement called viscosity. Soap viscosity should be between 100 cps
(centerpoise) and 2500 cps for all Bradley soap dispensers. Thinner soaps are perceived by the users as
being “watered down” so users tend to take more than they need, resulting in waste.
Thick soaps flow
slower and inhibit the “flushing” action of the valves, which allows the soap to congeal in the valve and
cause clogs.
The pH (acid) level of the soap should be in the range of 6.5 to 8.5. More acidic soaps (pH levels lower
than 6.5) will corrode metal parts (even stainless steel!!) and degrade rubber and plastic components. They
will also cause skin irritation.
Most inexpensive soaps (typically the pink lotion type) fall into this acidic
category and will eventually cause valve failure and metal corrosion.
Base soaps (pH levels higher than
8.5) will cause swelling or degradation of rubber and plastic parts and skin irritation.
Generally, any quality soap meeting the viscosity and pH guidelines above will work well with Bradley
soap dispensers. PCMX or Isapropanol based antibacterial soaps (within viscosity and pH limits) will also
work with Bradley dispensers. Soaps satisfying these basic guidelines will provide consistent flow and
reduce clogs.
Most soap dispenser problems are caused by soap that is too thick or corrosive, or by a lack of maintenance.
Many soaps come in concentrate form which must be diluted with water. Often, the soap is improperly
diluted or used straight out of the bottle, which causes clogging and valve failure. If proper soap is being
used, valves that have never been cleaned are usually the source of dispensing problems. Bradley has
entered into an agreement with Champion Brand Products to provide additional customer service for
purchasers of our dispensers regarding soap issues. They are very helpful and can get to the bottom of
almost any soap dispenser-related problem. They also sell an excellent “Bradley approved” soap. Please
see Bradley Instruction sheet 215-1286 for soap valve cleaning details and Champion Brand Products
contact information.
Check Valve Troubleshooting
If water just dribbles or does not flow from sprayhead:
1. Turn off water supplies to fixture.
2 Inspect check valves for proper installation. See Stop, Strainer and Check Valve on page 19.
3. Open the stops and clean the strainers, if necessary.
If water sprayhead delivers all hot or cold water:
1. Turn off water supplies to fixture.
2. Inspect check valves for proper installation.
3. Open the stops and clean the strainers, if necessary.
4. Inspect mixing valve for proper installation (see Vernatherm valve on page 24).