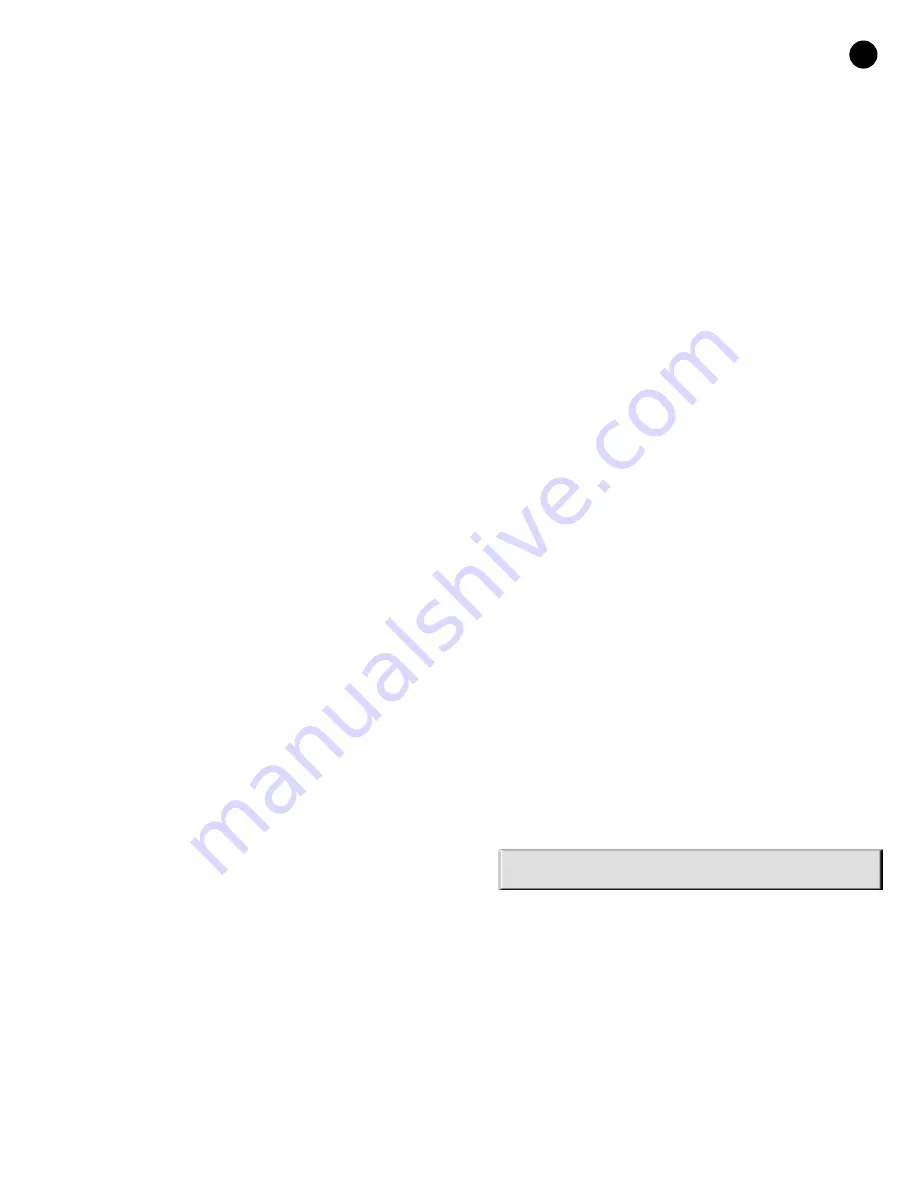
6720220330 Revised 05-12
9
SEQUENCE OF OPERATION-TWO STAGE UNITS:
(Figure #14 Wire Schematic)
COOLING MODE:
Energizing the “O” terminal energizes the unit reversing
valve in the cooling mode. The fan motor starts when the
“G” terminal is energized. Note that the fan motor will take
30 seconds to ramp up to operating speed and will run at
fan only rated air flow as long as there is no call for
compressor or heater operation.
When the thermostat calls for first stage cooling (Y1) the
loop pump or solenoid valve is energized and the first stage
of compressor capacity starts. The fan ramps up to first
stage cooling air flow in 30 seconds.
When the thermostat calls for second stage cooling (Y2) the
second stage (or full compressor capacity) is initiated. The
fan ramps up to full cooling air flow.
Once the thermostat is satisfied, the compressor shuts
down accordingly and the fan ramps down to either fan
only mode or off over a span of 30 seconds.
Note that a fault condition initiating a lockout will de-
energize the compressor irrespective of which stage is
engaged.
HEATING MODE:
The first two stages of heating (Y1 & Y2) operate in the
same manner as cooling, but with the reversing valve de-
energized. On a call for auxiliary heat (W1), the fan ramps
up to auxiliary heat air flow immediately and the electric
heater package is energized along with the compressor. As
the thermostat is satisfied, the heaters will shut off as soon
as W1 is de-energized, and the compressors will remain on
until the thermostat stages are satisfied. Note that if the
unit compressor lock out for any reason at this time, the
electric heaters will continue to function normally.
Once the thermostat is satisfied, the compressor shuts
down and the fan ramps down either fan only mode or off
over a span of 30 seconds. If emergency heat (W2/EM) is
called for, the fan will ramp up to emergency heat air flow
immediately and the heater package will energize in
emergency heat mode, all heater elements coming on. On
shut down the fan will ramp down over a period of 30
seconds.
WELL WATER SYSTEMS:
(Figure #10)
In well water applications water pressure must always be
maintained in the heat exchanger. This can be
accomplished with either control valve or a bladder type
expansion tank. When using a single water well to supply
both domestic water and the heat pump care must be
taken to insure that the well can provide sufficient flow for
both. In well water applications a slow closing solenoid
valve must be used to prevent water hammer.
Solenoid valves should be connected across Y1 and C1 on
the interface board for all. Make sure that the VA draw of the
valve does not exceed the contact rating of the thermostat.
INSTALLATION OF PRESSURE
REGULATING VALVES:
Pressure regulating valves are used to increase or decrease
water flow through the heat pump in response to
refrigerant pressure. In some cases more water may be
required in heating than in cooling, or vice versa. With the
Envirosaver heat pumps these valves are not required.
However, if installed, a pair of valves are required for proper
operation, one valve for cooling (direct acting) and another
valve for heating (indirect acting). A refrigerant tap is
provided in the refrigerant line located between the
reversing valve and the water-to-refrigerant heat exchanger
for proper monitoring of the refrigerant pressures.
The discharge water from the heat pump is not
contaminated in any manner and can be disposed of in
various ways depending on local building codes (i.e.
discharge well, dry well, storm sewer, drain field, stream or
pond, etc.) Most local codes forbid the use of a sanitary
sewer for disposal. Consult your local building and zoning
department to insure compliance in your area.
COOLING TOWER/BOILER SYSTEMS:
(Figure #11)
The cooling tower and boiler water loop temperature is
usually maintained between 50˚ F to 100 ˚ F to assure
adequate cooling and heating performance.
In the cooling mode, heat is rejected from the FHP unit into
the water loop. A cooling tower provides evaporative
cooling to the loop water thus maintaining a constant
supply temperature to the unit. When utilizing open
cooling towers, chemical water treatment is mandatory to
ensure the water is free from corrosive elements. A
secondary heat exchanger (plate frame) between the unit
and the open cooling tower may also be used. It is
imperative that all air be eliminated from the closed loop
side of the heat exchanger to insure against fouling.
In the heating mode, heat is absorbed from the water loop.
A boiler can be utilized to maintain the loop at the desired
temperature.
CAUTION:
Water piping exposed to extreme low ambient
temperatures is subject to freezing.
Consult the specification sheets for piping sizes. Teflon
tape sealer should be used when connecting to the unit to
insure against leaks and possible heat exchanger fouling.
Do not overtighten the connections. Flexible hoses should
be used between the unit and the rigid system to avoid
possible vibration. Ball valves should be installed in the
supply and return lines for unit isolation and unit water
flow
balancing.
Pressure/temperature
ports
are
recommended in both supply and return lines for system
flow balancing. Water flow can be accurately set by
measuring the water-to-refrigerant heat exchangers water
side pressure drop. See specification sheets for water flow
vs. pressure drop information.
ES SERIES
Содержание FHP ES Series
Страница 14: ...6720220330 Revised 05 12 14 ES SERIES Figure 13 ...
Страница 15: ...6720220330 Revised 05 12 15 Figure 14 ES SERIES ...