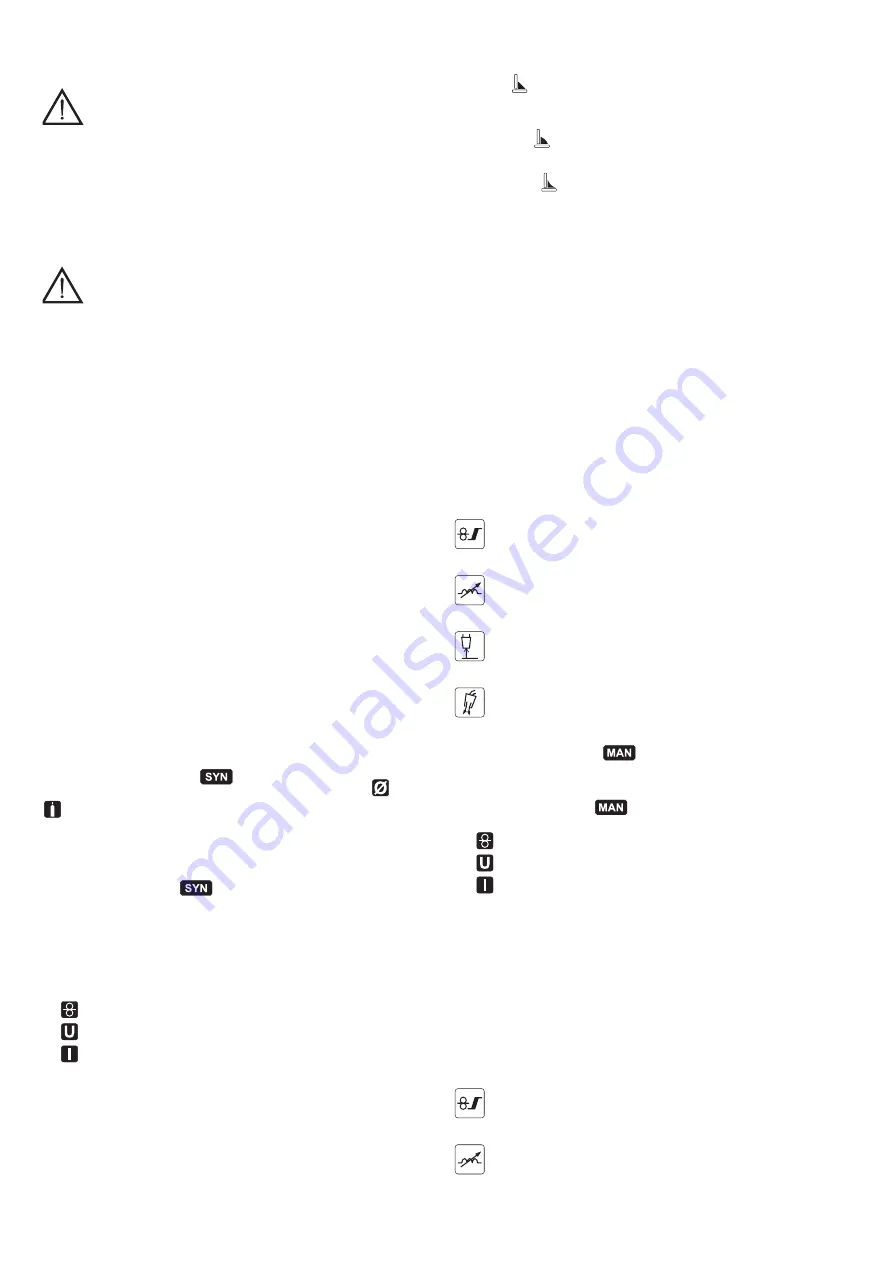
- 8 -
- Insert the welding machine plug in the power supply outlet, switch on the welding
machine, press the torch button and wait for the end of the wire to pass through the
whole of the wire guide hose and protrude by 10-15 cm from the front part of the
torch, release the button.
WARNING! During these operations the wire is live and subject to
mechanical stress; therefore if adequate precautions are not taken the wire
could cause hazardous electric shock, injury and striking of electric arcs:
- Do not direct the mouthpiece of the torch towards parts of the body.
- Keep the torch away from the gas bottle.
- Re-fit the contact tip and the nozzle onto the torch
(4b)
.
- Check that wire feed is regular; set the roller and spindle braking pressure to the
minimum possible values making sure that the wire does not slide in the groove and
when feed is halted the loops of wire are not loosened by excessive reel inertia.
- Cut the end of the wire so that 10-15 mm protrude from the nozzle.
- Close the reel compartment door.
5.5 LOADING THE WIRE SPOOL ONTO THE SPOOL GUN (Fig. I)
ATTENTION! BEFORE LOADING THE WIRE, MAKE SURE THE
WELDING MACHINE IS OFF AND DISCONNECTED FROM THE MAINS.
MAKE SURE THE WIRE FEEDERS, THE WIRE GUIDE HOSE AND THE TORCH
CONTACT PIPE CORRESPOND WITH THE DIAMETER AND NATURE OF THE
WIRE TO BE USED AND THAT THEY ARE CORRECTLY MOUNTED. DO NOT
WEAR PROTECTIVE GLOVES WHEN THREADING THE WIRE.
- Remove the cover by unscrewing the relative screw (1).
- Position the wire coil onto the reel.
- Release the pressure counter-roller and distance it from the lower roller (2).
- Free the wire end, cut off the misshaped end by cutting it cleanly and without leaving
a burr; rotate the reel counter-clockwise and position the wire end into the wire feed
input, pushing it by 50-100 mm into the torch swan neck (2).
- Reposition the counter-roller, adjusting the pressure at an intermediate value, make
sure the wire is positioned correctly in the hollow of the lower roller (3).
- Gently stop the reel, using the relative adjustment screw.
- With the
SPOOL GUN
connected, insert the welding machine plug into the mains
socket, switch on the welding machine, press the spool gun push-button and wait
for the end of the wire which is running along the whole wire feed casing, to exit by
100-50mm from the front of the torch, then release the torch push-button.
6. MIG-MAG WELDING: PROCESS DESCRIPTION
6.1 SHORT ARC
Wire welding and detachment of the drop takes place via subsequent short-circuits of
the wire tip and weld pool (up to 200 times per second). The stick-out length of the wire
is normally between 5 and 12mm.
Carbon, low-alloy steel
- Usable wire diameter:
0.6 - 0.8 - 1.0 mm (1.2 mm version 270A only)
- Usable gas:
CO
2
or Ar/CO
2
mixtures
Stainless steel
- Usable wire diameter:
0.8 - 1.0 mm (1.2 mm version 270A only)
- Usable gas:
Ar/O
2
or Ar/CO
2
mixtures (1-2%)
Aluminium and CuSi/CuAl
- Usable wire diameter:
0.8 - 1.0 mm (1.2 mm version 270A only)
- Usable gas:
Ar
Core wire
- Usable wire diameter:
0.8 - 0.9 - 1.2mm
- Usable gas:
None
6.2 PROTECTION GAS
The protective gas flow rate must be 8-14 l/min.
7. MIG-MAG OPERATION MODEE
7.1 SYNERGIC operating mode
Defined by the user, the parameters such as material, wire diameter
, gas type
, the welding machine is automatically set in optimal operating conditions
established by the various synergic curves saved. The user only has to select the
material thickness to begin welding (OneTouch Technology).
7.1.1 LCD display in SYNERGIC mode (Fig. L)
NB: All the values which be displayed and selected depend on the type of set welding.
1- Synergic operating mode
;
2- Material to weld. Types available: Fe (steel), Ss (stainless steel), AlMg
5
AlSi
5
(aluminium), CuSi/CuAl (zinc-plated sheet metal - brazing), Flux (core wire - NO
GAS welding);
3- Diameter of wire to use;
4- Recommended safety gas;
5- Thickness of material to weld;
6- Graphic indicator of thickness of material;
7- Graphic indicator of welding seam shape;
8- Welding values:
wire feed speed;
welding voltage;
welding current.
9- ATC (Advanced Thermal Control).
7.1.2 Parameters setting
Pressing button C-2 for at least 1 second, you can access the preset programs on
the machine.
Turning the knob C-2 you can slide all the programs (PRG 01, 02, etc.). Select the
program chosen by pressing and releasing the same knob. The welding machine
sets itself automatically in the best operation conditions established by the different
synergy curves that are saved. The user only has to select the material thickness
using knob C-1 to begin welding. The welding voltage and current is shown on the
display only during welding.
7.1.3 Adjustment of the welding seam shape
Adjustment of the shape of the seam takes place using the knob (Fig. C-2) that
regulates the arc length thereby establishing the greater or lesser welding temperature
input.
The settings scale varies from -10 ÷ 0 ÷ +10; in most cases, the knob in the intermediate
position (0,
) has an optimal base setting (the value is shown on the LCD display
on the left of the graphic symbol of the welding seam and disappears after a set time).
Using the knob (Fig. C-2), the graphic indication on the display of the shape of the
welding changes showing a more convex, flat or concave result.
Convex shape.
It means there is a low thermal load, therefore welding is "cold",
with little penetration; therefore, turning the knob clockwise you obtain more thermal
load with the effect of welding with greater melting.
Concave shape.
It means there is a high thermal load, therefore welding is too
"hot", with excessive penetration; then, turn the knob anti-clockwise to obtain greater
melting.
7.1.4 ATC Mode (Advanced Thermal Control)
This is enabled automatically when the thickness selected is less or equal to 1.5mm.
Description:
the particular instantaneous control of the welding arc and the ultra rapid
correcting of parameters minimize current spikes, something that is characteristic of
Short Arc transfer procedures, to the advantage of a low thermal load on the piece
to be welded. The result, on the one hand, is reduced deformation of materials and,
on the other, a fluid and accurate transfer of the weld material and the creation of a
welding seam that is easy to model.
Advantages:
- easy welding of thin materials;
- decreased deformation of material;
- stable arc even when working with low currents;
- rapid and accurate spot welding;
- easier coupling of spaced sheets.
7.1.5 Using the spool gun (where available)
All the settings procedures (material, wire diameter, gas type) are described above.
The spool gun knob (Fig. I-5) adjusts the wire speed (and the welding current and
thickness simultaneously). The user only has to adjust the arc voltage via the display
(if necessary).
7.1.6 Advanced parameter setting: MENU 1 (Fig. M)
Press the knobs (Fig. C1) and (Fig. C2) for at least 1 second and release to access
the advanced parameter settings menu. When MENU 1 appears, again press. Each
parameter can be set to the desired value by rotating/pressing the knob (Fig. C2) until
you exit the menu.
: trailing wire ramp correction (Fig. M-1)
Use to correct the trailing wire starting ramp to prevent any initial accumulation in the
welding seam. Settings from - 10 % to + 10 %. Factory value: 0 %
: electronic reactance correction (Fig. M-2)
A higher value determines a hotter welding bath. Settings from - 10 % (low reactance
machines) to + 10 % (high reactance machines). Factory value: 0 %
: burn-back correction. (Fig. M-3)
Use to adjust the wire burn-back time when welding is stopped. Settings from - 10 %
to + 10 %. Factory value: 0 %
: Post gas. (Fig. M-4)
Use to adapt the protective gas outflow starting from when welding is stopped. Settings
from 0 to 10 seconds. Factory value: 1 sec.
7.2 MANUAL operating mode
The user can customise all the welding parameters.
7.2.1 LCD display in MANUAL mode (Fig. N)
1- MANUAL operating mode
;
2- Welding values:
wire feed speed;
welding voltage;
welding current.
7.2.2 Parameters setting
In manual mode, the wire feeding speed and the welding voltage are adjusted
separately. The knob (Fig. C-1) adjusts the wire speed, the knob (Fig. C-2) adjusts
the welding voltage (which determines the welding power and influences the seam
shape). The welding current is shown on the display (Fig. N-2) only during welding.
7.2.3 Setting of spool gun parameters (where available)
In manual mode, the wire feeding speed and the welding voltage are adjusted
separately. The spool gun knob (Fig. L-5) adjusts the wire speed, whilst the welding
voltage is adjusted via the display.
7.2.4 Advanced parameter setting: MENU 1 (Fig. M)
Press the knobs (Fig. C1) and (Fig. C2) for at least 1 second and release to access
the advanced parameter settings menu. When MENU 1 appears, again press. Each
parameter can be set to the desired value by rotating/pressing the knob (Fig. C2) until
you exit the menu.
: Trailing wire ramp (Fig. M-1).
Use to adjust wire feed rate as welding starts, in order to optimise arc strike. Settings
from 20 to 100 % (start in % of full capacity speed). Factory value: 50 %
: Electronic reactance (Fig. M-2)
A higher value determines a hotter welding bath. Settings from 10 % (low reactance
machines) to 100 % (high reactance machines). Factory value: 50 %
Содержание Starmig 223 Treo Synergic
Страница 21: ... 158 FIG B2 WELDING POLARITY CHART TORCH WORKPIECE MIG MAG GAS TIG MMA 1 2 3 4 5 6 13 15 14 ...
Страница 22: ... 159 FIG B3 1 4 9 10 5 6 8 2 11 3 12 13 15 14 16 17 ...
Страница 26: ... 163 FIG D2 Nr 8 M6x16 H H H H H O P T I O N A L ...
Страница 27: ... 164 FIG E FIG F TAB 5 FIG G SUGGESTED VALUES FOR WELDING DATI ORIENTATIVI PER SALDATURA ...
Страница 28: ... 165 FIG H b c d a a b ...
Страница 29: ... 166 FIG H1 ...
Страница 30: ... 167 FIG H2 ...
Страница 31: ... 168 FIG I 0 8 0 8 1 2 3 4 5 ...