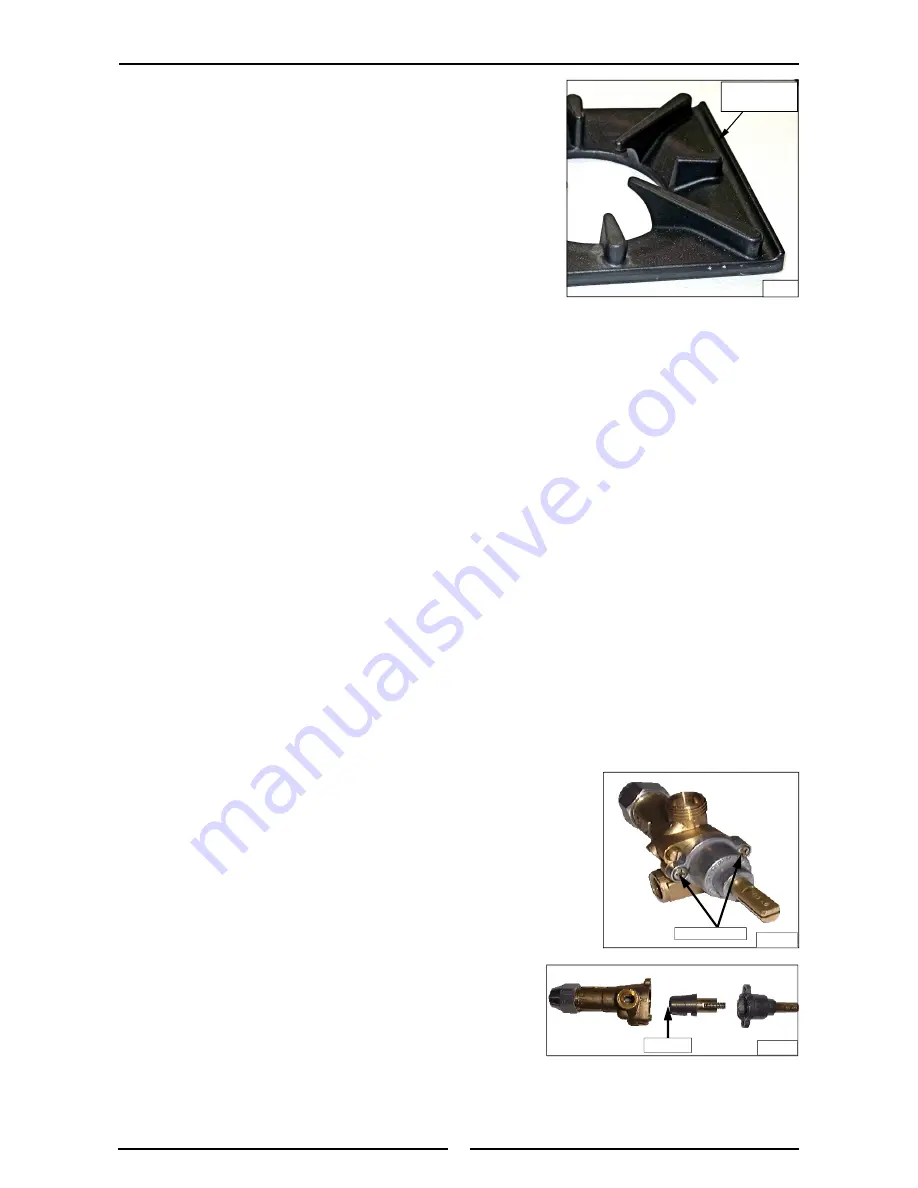
17
NOTE: It is imperative that the trivet supports are correctly
re-fitted to the unit to ensure that the trivets locate
correctly and sit flush and level. NOTE that the trivet
support front end side rail profiles are different at
either side (Refer to Fig 6) and only one of the side
rails seat into the cut-out in the range, whereas the
rear end of the trivet support side rail profiles are the
same and have 2 locating cut-outs.
b. Refit the burner bowl onto the manifolds protruding
through the splash guards, taking care not to damage the
thermocouple (and pilot tube - PF Option) which is close
to the manifold.
NOTE: The burner bowl (cast item) has 2 locating holes drilled into the base flange (See Fig 7)
these are to locate the burner bowl onto the cap screw on the gas manifold when re-fitting
the burner bowl onto the gas manifold (Refer to Fig 8 {F-Option} and Fig 9 {PF-Option}).
c. Refit the burner caps (cast brass) onto the burner bowls already fitted to the manifold. The
burner cap is a loose fit into the burner bowl.
d. Refit the trivets to the cook top, taking note that the trivets are manufactured with a lip on one
edge, the lip must always be fitted to the outer edge (front and back) of the range. (See Fig 10).
e. Refit the grease / spill tray(s) to the range.
Oven Interior
a. Do not use wire brushes, steel wool or other abrasive materials to clean the oven interior.
b. Clean the oven regularly with a good quality domestic oven cleaner.
c. Once a week, remove and clean any built up of grease etc. from the oven racks and the bottom
spill over cover.
d. Dry the oven thoroughly with a dry cloth and polish with a soft dry cloth.
Periodic Maintenance
NOTE: All maintenance operations should only be carried out by a qualified service person.
To achieve the best results cleaning must be regular and thorough and all controls and mechanical parts
should be checked and adjusted periodically by a qualified service person. If any small faults occur, have
them attended to promptly. Don't wait until they cause a complete breakdown. It is recommended that
the appliance is serviced every 6 months.
Gas Control Valve Re-Greasing
The gas control valve should be dismantled and greased every 6
months to ensure the correct operation of the gas control valve.
To carry out this operation;-
a. Remove the gas control knobs from the gas tap spindles by
pulling the knobs away from the control panel.
b. Remove the drip tray from the appliance.
c. Remove the two screws on the underside of the control panel,
securing the control panel to the hob.
d. Remove the control panel from the front of the appliance.
e. Remove the 2 screws holding shaft plate to gas control
body and remove control shaft and plate.
(See Fig 11).
Note orientation of shaft for correct re-assembly.
f. Using needle nose pliers or similar, pull out gas control
spindle, again noting its orientation.
g. Apply a suitable high temperature gas cock grease or
lubricant such as ROCOL - A.S.P (Anti scuffing paste)/
Dry Moly Paste to the outside of spindle.
(See Fig 12).
h. Replace spindle and re-assemble the gas control in reverse order.
i. Refit the control panel to the appliance and secure with 2 screws.
j. Refit the knobs to the gas control valve spindles.
Cleaning and Maintenance
Two Screws
Fig 11
Spindle
Fig 12
Notice Lip on
Trivet Edge
Fig 10
Содержание Evolution G504
Страница 7: ...5 Dimensions G504 G504D G504C G504B ...
Страница 8: ...6 Dimensions G528 G528D G528C G528B G528A ...
Страница 31: ...29 ...