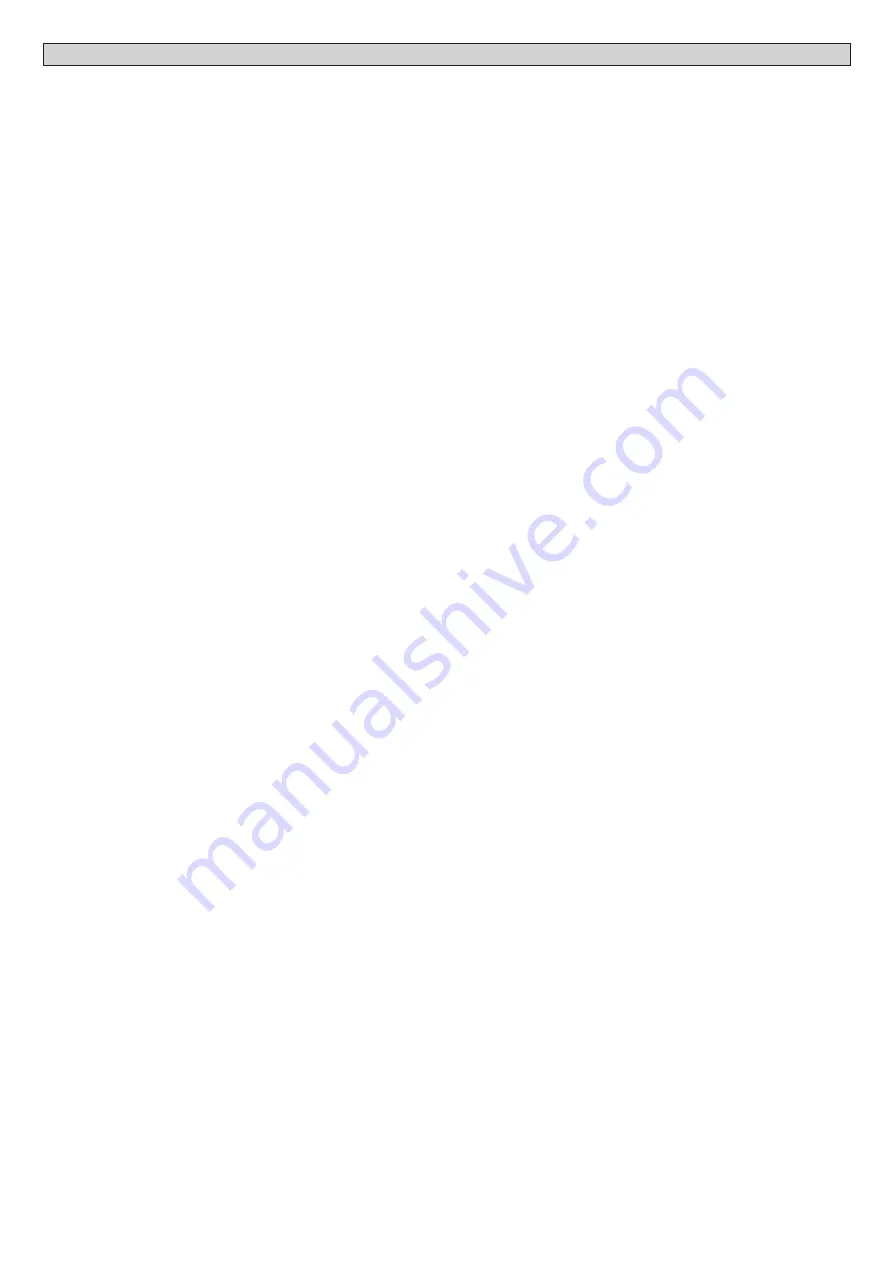
INSTALLATION MANUAL
ORO - Ver. 03 -
9
INSTALLATION MANUAL
ENGLISH
WARNING!
All versions are provided with a ball joint which allows the rod
to be lengthened or shortened by approximately 5mm, but only if it was fixed
using the dimensions shown in fig.8 before installation after installation, this
adjustment allows the rod stroke to be corrected.
Fig.9 illustrates the oscillation that the controllers may show with respect to
their horizontal axis.
During installation, carefully follow all the phases described below, taking
care to protect the actuator’s chromium-plated rod at all times, in order to
prevent it from being damaged by impact or any welding slag.
1) Identify “a - b -
α
°
” in the table in fig. 3.
2) Fix bracket “P” (fig.10) to the pillar.
3) Fit the piston in bracket “P”.
4) Make sure that the rod eye is adjusted see fig 8.
5) Pull the rod out completely after activating the emergency release
(fig.18)
6) Push the rod back in manually until you position the eye hole with the
hole of the template (fig.22).
7) Fit fork “F” (fig.8) to the rod.
8) Fully close the gate leaf against the centre stop plate.
9) Keeping the piston level, mark the position for attaching fork (fig. 10 ref.
“F”) to the leaf.
10) Remove fork “F” from the rod and move the piston sideways.
11) Fix fork (fig.10 ref. “F”) to the leaf by means of screws or welding.
12) Reconnect the rod to fork “F” remove bleed screw “S” (Fig.17) and
supply the actuator with power.
13) Make some full cycles.
14) In the case when you have to adjust the opening angle, do so by
adjusting the ball joint see fig.8.
15) After adjustment proceed as follows in order to secure piston into
mounting bracket: clean piston cover and secure with fastener, insert
mounting pin and tighten lock nut with open end wrench as shown in
Fig.8A.
5.4) Suggestions for particular installations
Fig.5 A recess must be made to house the controller when the leaf is
completely open; the recess measurements are shown in fig.5.
Fig.7 When the ”b” dimension is greater than the values shown in the
installation tables, it is necessary to move the leaf hinge-pivot or
make a recess in the pillar, as in fig.6.
5.5) Anchoring of attachments to the pillar
Weld or fix the bracket base supplied to the pillar, check the “a” and “b”
measurements and then weld plate “P” to the said base. (fig. 10).
• If the pillar is made of masonry, plate “P” must be welded to the metal
base “PF” and deeply anchored by means of suitable hooks “Z” which are
to be welded on the back of the said base (fig. 11a).
• If the pillar is made of stone, plate “P” is welded to the metal base “PF”
and can be fixed by means of four metal screw anchors “T” (fig. 11b); if
the gate is large, it is advisable to weld plate “P” to an angle-shaped base
(fig. 11c).
5.6) Anchoring of attachments to the leaf
Weld or fix fork “F” to the leaf at distance between centres “C” shown in fig.4,
making sure that the actuator is perfectly level (level “L”, fig. 10) with respect
to the gate movement plane.
• If the gate is made of metal, the fork can be welded (fig. 12a) or fixed
using appropriate screws (fig. 12c).
• If the gate is made of wood, the fork can be fixed using appropriate
screws (fig. 12b).
6) GROUND LEAF STOP PLATES
For the actuator to operate correctly, stop plates “FA” must be used during
both opening and closing manoeuvres, as shown in fig. 13.
The leaf stop plates must prevent the actuator rod from going to the end-
of- stroke position. Fig.14 specifies the dimensions needed to check the
correct actuator installation both for pushing and towing. The plates must
be positioned in such a way as to maintain a rod stroke margin of
approximately 5mm; this is to avoid possible operation anomalies (such as
a lock-up).
7) ELECTRIC LOCK FITTING
This is needed on mod.
ORO/E
only since these are not supplied with a
hydraulic lock on closing.
The
EBP
model electric lock (fig.15) consists of a continuous service
electromagnet being anchored to the ground.
This device remains energized throughout the actuator operation time, and
allows the catch to stay lifted when it reaches the closing position, without
opposing any resistance; the catch will drop into position when the gate has
completed the closing cycle.
The electric lock can also be used to keep the block of the gate in case of
actuator malfunction or current failure.
8) ELECTRICAL INSTALLATION SET-UP
Lay out the electrical installation (fig. 16) with reference to the CEI 64-8 and
IEC 364 provisions, complying with the HD 384 and other national standards
in force for electrical installation. The mains power supply connections must
be kept totally separate from the service connections (photocells, electric
edges, control devices etc.).
WARNING! For connection to the mains, use a multipolar cable with
a minimum of 3x1.5mm
2
cross section and complying with the
previously mentioned regulations. For example, if the cable is out side
(in the open), it has to be at least equal to H07RN-F, but if it is on the
inside (or outside but placed in a plastic cable cannel) it has to be or
at least egual to H05VV-F with section 3x1.5mm
2
.
Connect the control and safety devices in compliance with the previously
mentioned electrical installation standards.
Fig.16 shows the number of connections and the cross section for power
supply cables having a length of approximately 100 metres; in case of
longer cables, calculate the cross section for the true automation load.
When the auxiliary connections exceed 50-metre lengths or go through
critical disturbance areas, it is recommended to decouple the control and
safety devices by means of suitable relays.
8.1) The main automation components are
(fig.16):
I
Type-approved omnipolar circuit breaker with at least 3mm contact
opening, provided with protection against overloads and short circuits,
suitable for cutting out automation from the mains. If not already installed,
place a type-approved differential switch with a 0.03A threshold in the
circuit just before the automation system.
Qr
Control panel and incorporated receiver.
SPL
Preheating board for operation with temperature lower than 5
°
C
(optional).
S
Key selector.
AL
Blinker with tuned antenna and RG58 cable.
M
Actuator.
E
Electric lock.
Fte
Pair of external photocells (transmitter).
Fre
Pair of external photocells (receiver).
Fti
Pair of internal photocells with CF posts.
Fri
Pair of internal photocells with CF posts (receiver).
T
1-2-4 channel transmitter.
IMPORTANT
: Before electrically activating the actuator, remove bleed
screw “S” (fig. 17) which is positioned under the base with articulated joint
and keep it for any later reuse. Only remove bleed screw “S” when the
actuator is installed.
9) MANUAL OPENING
In emergency case, such as in the case of power cut-out, to release the
gate, insert the same key C used for the adjustment of the by-pass valve
inside the triangular pin (Fig.18) and rotate it counterclockwise.
The gate can now be opened manually.
WARNING! make sure that you manually push the gate open at the
same speed as the motor would have.
To reset the electric operation of the actuator, turn the key in clockwise
direction until pin is blocked.
9.1) Mod. ORO
In case of emergency, for example when the electrical power is disconnected,
to release the gate, insert the same key C used for the adjustment of the by-
pass valve inside the triangular pin (Fig.18) and rotate it counterclockwise.
The gate can now be opened manually. To reset the electric operation of
the actuator, turn the key in clockwise direction until pin is blocked.
9.2) Mod. ORO/E
Since these models are reversible, for the manual operation of the gate it
is sufficient that the electric lock be opened with the appropriate key. To
make the manual manoeuvre easier, the lock can be released by means of
a triangular pin which can be reached using the appropriate key.
10) PUSHING FORCE ADJUSTMENT
The pushing force is adjusted by two valves marked with the writing “
Close
”
and “
Open
” respectively, which are used to adjust the closing and opening
pushing force (fig.19).
Lift open the lid indicated in (Fig.19) there you will find the two valves.
ORO - Ver. 03 -
9
INSTALLATION MANUAL
ENGLISH
WARNING!
All versions are provided with a ball joint which allows the rod
to be lengthened or shortened by approximately 5mm, but only if it was fixed
using the dimensions shown in fig.8 before installation after installation, this
adjustment allows the rod stroke to be corrected.
Fig.9 illustrates the oscillation that the controllers may show with respect to
their horizontal axis.
During installation, carefully follow all the phases described below, taking
care to protect the actuator’s chromium-plated rod at all times, in order to
prevent it from being damaged by impact or any welding slag.
1) Identify “a - b -
α
°
” in the table in fig. 3.
2) Fix bracket “P” (fig.10) to the pillar.
3) Fit the piston in bracket “P”.
4) Make sure that the rod eye is adjusted see fig 8.
5) Pull the rod out completely after activating the emergency release
(fig.18)
6) Push the rod back in manually until you position the eye hole with the
hole of the template (fig.22).
7) Fit fork “F” (fig.8) to the rod.
8) Fully close the gate leaf against the centre stop plate.
9) Keeping the piston level, mark the position for attaching fork (fig. 10 ref.
“F”) to the leaf.
10) Remove fork “F” from the rod and move the piston sideways.
11) Fix fork (fig.10 ref. “F”) to the leaf by means of screws or welding.
12) Reconnect the rod to fork “F” remove bleed screw “S” (Fig.17) and
supply the actuator with power.
13) Make some full cycles.
14) In the case when you have to adjust the opening angle, do so by
adjusting the ball joint see fig.8.
15) After adjustment proceed as follows in order to secure piston into
mounting bracket: clean piston cover and secure with fastener, insert
mounting pin and tighten lock nut with open end wrench as shown in
Fig.8A.
5.4) Suggestions for particular installations
Fig.5 A recess must be made to house the controller when the leaf is
completely open; the recess measurements are shown in fig.5.
Fig.7 When the ”b” dimension is greater than the values shown in the
installation tables, it is necessary to move the leaf hinge-pivot or
make a recess in the pillar, as in fig.6.
5.5) Anchoring of attachments to the pillar
Weld or fix the bracket base supplied to the pillar, check the “a” and “b”
measurements and then weld plate “P” to the said base. (fig. 10).
• If the pillar is made of masonry, plate “P” must be welded to the metal
base “PF” and deeply anchored by means of suitable hooks “Z” which are
to be welded on the back of the said base (fig. 11a).
• If the pillar is made of stone, plate “P” is welded to the metal base “PF”
and can be fixed by means of four metal screw anchors “T” (fig. 11b); if
the gate is large, it is advisable to weld plate “P” to an angle-shaped base
(fig. 11c).
5.6) Anchoring of attachments to the leaf
Weld or fix fork “F” to the leaf at distance between centres “C” shown in fig.4,
making sure that the actuator is perfectly level (level “L”, fig. 10) with respect
to the gate movement plane.
• If the gate is made of metal, the fork can be welded (fig. 12a) or fixed
using appropriate screws (fig. 12c).
• If the gate is made of wood, the fork can be fixed using appropriate
screws (fig. 12b).
6) GROUND LEAF STOP PLATES
For the actuator to operate correctly, stop plates “FA” must be used during
both opening and closing manoeuvres, as shown in fig. 13.
The leaf stop plates must prevent the actuator rod from going to the end-
of- stroke position. Fig.14 specifies the dimensions needed to check the
correct actuator installation both for pushing and towing. The plates must
be positioned in such a way as to maintain a rod stroke margin of
approximately 5mm; this is to avoid possible operation anomalies (such as
a lock-up).
7) ELECTRIC LOCK FITTING
This is needed on mod.
ORO/E
only since these are not supplied with a
hydraulic lock on closing.
The
EBP
model electric lock (fig.15) consists of a continuous service
electromagnet being anchored to the ground.
This device remains energized throughout the actuator operation time, and
allows the catch to stay lifted when it reaches the closing position, without
opposing any resistance; the catch will drop into position when the gate has
completed the closing cycle.
The electric lock can also be used to keep the block of the gate in case of
actuator malfunction or current failure.
8) ELECTRICAL INSTALLATION SET-UP
Lay out the electrical installation (fig. 16) with reference to the CEI 64-8 and
IEC 364 provisions, complying with the HD 384 and other national standards
in force for electrical installation. The mains power supply connections must
be kept totally separate from the service connections (photocells, electric
edges, control devices etc.).
WARNING! For connection to the mains, use a multipolar cable with
a minimum of 3x1.5mm
2
cross section and complying with the
previously mentioned regulations. For example, if the cable is out side
(in the open), it has to be at least equal to H07RN-F, but if it is on the
inside (or outside but placed in a plastic cable cannel) it has to be or
at least egual to H05VV-F with section 3x1.5mm
2
.
Connect the control and safety devices in compliance with the previously
mentioned electrical installation standards.
Fig.16 shows the number of connections and the cross section for power
supply cables having a length of approximately 100 metres; in case of
longer cables, calculate the cross section for the true automation load.
When the auxiliary connections exceed 50-metre lengths or go through
critical disturbance areas, it is recommended to decouple the control and
safety devices by means of suitable relays.
8.1) The main automation components are
(fig.16):
I
Type-approved omnipolar circuit breaker with at least 3mm contact
opening, provided with protection against overloads and short circuits,
suitable for cutting out automation from the mains. If not already installed,
place a type-approved differential switch with a 0.03A threshold in the
circuit just before the automation system.
Qr
Control panel and incorporated receiver.
SPL
Preheating board for operation with temperature lower than 5
°
C
(optional).
S
Key selector.
AL
Blinker with tuned antenna and RG58 cable.
M
Actuator.
E
Electric lock.
Fte
Pair of external photocells (transmitter).
Fre
Pair of external photocells (receiver).
Fti
Pair of internal photocells with CF posts.
Fri
Pair of internal photocells with CF posts (receiver).
T
1-2-4 channel transmitter.
IMPORTANT
: Before electrically activating the actuator, remove bleed
screw “S” (fig. 17) which is positioned under the base with articulated joint
and keep it for any later reuse. Only remove bleed screw “S” when the
actuator is installed.
9) MANUAL OPENING
In emergency case, such as in the case of power cut-out, to release the
gate, insert the same key C used for the adjustment of the by-pass valve
inside the triangular pin (Fig.18) and rotate it counterclockwise.
The gate can now be opened manually.
WARNING! make sure that you manually push the gate open at the
same speed as the motor would have.
To reset the electric operation of the actuator, turn the key in clockwise
direction until pin is blocked.
9.1) Mod. ORO
In case of emergency, for example when the electrical power is disconnected,
to release the gate, insert the same key C used for the adjustment of the by-
pass valve inside the triangular pin (Fig.18) and rotate it counterclockwise.
The gate can now be opened manually. To reset the electric operation of
the actuator, turn the key in clockwise direction until pin is blocked.
9.2) Mod. ORO/E
Since these models are reversible, for the manual operation of the gate it
is sufficient that the electric lock be opened with the appropriate key. To
make the manual manoeuvre easier, the lock can be released by means of
a triangular pin which can be reached using the appropriate key.
10) PUSHING FORCE ADJUSTMENT
The pushing force is adjusted by two valves marked with the writing “
Close
”
and “
Open
” respectively, which are used to adjust the closing and opening
pushing force (fig.19).
Lift open the lid indicated in (Fig.19) there you will find the two valves.
10 -
ORO - Ver. 03
INSTALLATION MANUAL
ENGLISH
Turn the valves towards the “
+
” sign to increase the force transmitted; turn
the valves towards the “
-
” sign to reduce the force.
To achieve proper antisquash safety, the pushing force must be slightly
higher than that needed to move the leaf during both closing and opening
manoeuvres; the strength, which is measured on the leaf edge, must never
exceed the limits set out by the current national standards.
Under no circumstances whatsoever must the by-pass valves be fully
closed.
Complete the adjustments and restore the release system.
The actuator is not provided with electrical limit switches.
Therefore
the motors switch off at the end of the operation time set by the control unit.
The said operation time must last approximately 2-3 seconds after the
moment when the leaves meet the ground stop plates.
11) COVERING ELEMENT POSITIONING
Covering element “C” for all models can become left or right-handed by
reversing the position of cap “T” (fig. 21), taking care to keep the water
drainage channel always at the bottom, remember to screw back the Q
screw.
12) AUTOMATION CHECK
Before the automation device finally becomes operational, scrupulously
check the following conditions:
• Check that all components are tightly fixed.
• Check that all control devices (photocells, pneumatic edge etc) operate
correctly.
• Check the emergency manoeuvre command.
• Check the opening and closing operations using the control devices
provided.
• Check the normal (or personalised) function control logic in the control
unit.
13) AUTOMATION OPERATION
Since the automation system can be remotely controlled by means of a
radio control device or a Start button, all safety devices must be frequently
checked in order to ensure their perfect efficiency.
In the event of any irregular operation, request immediate assistance from
qualified personnel.
Children must be kept at a safe distance from the automation operation
area.
14) CONTROL
Various types of controls are provided (manual, radio control, magnetic
card access control etc.) depending on the installation requirements and
characteristics.
(See the specific instructions for the various control systems).
The installer undertakes to instruct the user about the correct automation
operation, and also point out the operations required in case of emergency.
15) MAINTENANCE
Before carrying out any maintenance to the controller, disconnect the
system power supply.
• Periodically check the system for oil leaks.
To recap the oil, please use the same oil as descibed in the ”
TECHNICAL
SPECIFICATIONS
” paragraph and proceed with tho following instruction:
a) With the piston all the way out take of the screw( P) situated on the
base see (Fig.20).
b) Top up using the prescribed oil until its level reaches the level of the
oil lid see (Fig.20).
c) Refit all the components paying attention to the seals.
ATTENTION -
Replace the actuator oil every 2 years with the same oil as
described in the ”
TECHNICAL SPECIFICATIONS
” paragraph.
• Check all automation safety devices.
• When any operational malfunction if found, and not resolved, disconnect
the systems power supply and request the assistance of a qualified
technician (installer).
• When the automation is out of order, activate the manual release knob
to allow the manual opening and closing operations to be carried out by
means of the electric lock.
16) MALFUNCTIONS AND REMEDIES
16.1) Faulty operation of the actuator
Using an appropriate instrument, check that the ends of the actuator are
supplied with voltage after the opening or closing command is given.
If the motor vibrates but does not turn, the causes could be as follows:
• Wrong connection of common wire C (always light blue).
• No connection between the drive capacitor and the two drive terminals.
• If the leaf movement is opposite to what it should be, reverse the motor
drive connections in the control unit.
Leaf stops: when the operation time is insufficient, the leaves may not
complete their strokes. In that case, slightly increase the operation time
setting in the control unit.
16.2) Faulty operation of the electrical accessories
All faulty control and safety devices can cause abnormal operation or
automation block.
If the control unit is provided with a self-diagnosing system, identify the
fault.
In case of malfunction, it is advisable to disconnect and bridge all the
automation devices one by one, if necessary, until the faulty device is
identified. After replacing or repairing it, restore all the devices which were
previously disconnected or bridged. For all devices installed, refer to their
respective instruction manual.
WARNING !
the above operation must be carried out by qualified personnel.
During maintenance, the gate operational area must be appropriately
indicated and closed off, in order to avoid any danger to persons, animals
and property.
WARNINGS! Correct controller operation is only guaranteed when the
data specified in this manual are respected. The company cannot be
held responsible for any damage caused by failure to observe the
standards on safety, installation and good technical practice, as well
as the directives specified in the present manual.
17) SCRAPPING
WARNING:
This operation should only be carried out by qualified personnel.
Materials must be disposed of in conformity with the current regulations.
In case of scrapping, the automation devices do not entail any particular
risks or danger.
In case of recovered materials, these should be sorted out by type
(electrical components, copper, aluminium, plastic etc.).
18) DISMANTLING
WARNING!
This operation should only be carried out by qualified personnel.
When the automation system is disassembled to be reassembled on
another site, proceed as follows:
• Disconnect the power supply and the entire external electrical installation.
• Replace the bleed screw (fig. 17) under the articulated joint block.
• In the case where some of the components cannot be removed or are
damaged, they must be replaced.
The descriptions and illustrations contained in the present manual
are not binding. The Company reserves the right to make any alterations
deemed appropriate for the technical, manufacturing and commercial
improvement of the product, while leaving the essential product
features.
ORO - Ver. 03 -
9
INSTALLATION MANUAL
ENGLISH
WARNING!
All versions are provided with a ball joint which allows the rod
to be lengthened or shortened by approximately 5mm, but only if it was fixed
using the dimensions shown in fig.8 before installation after installation, this
adjustment allows the rod stroke to be corrected.
Fig.9 illustrates the oscillation that the controllers may show with respect to
their horizontal axis.
During installation, carefully follow all the phases described below, taking
care to protect the actuator’s chromium-plated rod at all times, in order to
prevent it from being damaged by impact or any welding slag.
1) Identify “a - b -
α
°
” in the table in fig. 3.
2) Fix bracket “P” (fig.10) to the pillar.
3) Fit the piston in bracket “P”.
4) Make sure that the rod eye is adjusted see fig 8.
5) Pull the rod out completely after activating the emergency release
(fig.18)
6) Push the rod back in manually until you position the eye hole with the
hole of the template (fig.22).
7) Fit fork “F” (fig.8) to the rod.
8) Fully close the gate leaf against the centre stop plate.
9) Keeping the piston level, mark the position for attaching fork (fig. 10 ref.
“F”) to the leaf.
10) Remove fork “F” from the rod and move the piston sideways.
11) Fix fork (fig.10 ref. “F”) to the leaf by means of screws or welding.
12) Reconnect the rod to fork “F” remove bleed screw “S” (Fig.17) and
supply the actuator with power.
13) Make some full cycles.
14) In the case when you have to adjust the opening angle, do so by
adjusting the ball joint see fig.8.
15) After adjustment proceed as follows in order to secure piston into
mounting bracket: clean piston cover and secure with fastener, insert
mounting pin and tighten lock nut with open end wrench as shown in
Fig.8A.
5.4) Suggestions for particular installations
Fig.5 A recess must be made to house the controller when the leaf is
completely open; the recess measurements are shown in fig.5.
Fig.7 When the ”b” dimension is greater than the values shown in the
installation tables, it is necessary to move the leaf hinge-pivot or
make a recess in the pillar, as in fig.6.
5.5) Anchoring of attachments to the pillar
Weld or fix the bracket base supplied to the pillar, check the “a” and “b”
measurements and then weld plate “P” to the said base. (fig. 10).
• If the pillar is made of masonry, plate “P” must be welded to the metal
base “PF” and deeply anchored by means of suitable hooks “Z” which are
to be welded on the back of the said base (fig. 11a).
• If the pillar is made of stone, plate “P” is welded to the metal base “PF”
and can be fixed by means of four metal screw anchors “T” (fig. 11b); if
the gate is large, it is advisable to weld plate “P” to an angle-shaped base
(fig. 11c).
5.6) Anchoring of attachments to the leaf
Weld or fix fork “F” to the leaf at distance between centres “C” shown in fig.4,
making sure that the actuator is perfectly level (level “L”, fig. 10) with respect
to the gate movement plane.
• If the gate is made of metal, the fork can be welded (fig. 12a) or fixed
using appropriate screws (fig. 12c).
• If the gate is made of wood, the fork can be fixed using appropriate
screws (fig. 12b).
6) GROUND LEAF STOP PLATES
For the actuator to operate correctly, stop plates “FA” must be used during
both opening and closing manoeuvres, as shown in fig. 13.
The leaf stop plates must prevent the actuator rod from going to the end-
of- stroke position. Fig.14 specifies the dimensions needed to check the
correct actuator installation both for pushing and towing. The plates must
be positioned in such a way as to maintain a rod stroke margin of
approximately 5mm; this is to avoid possible operation anomalies (such as
a lock-up).
7) ELECTRIC LOCK FITTING
This is needed on mod.
ORO/E
only since these are not supplied with a
hydraulic lock on closing.
The
EBP
model electric lock (fig.15) consists of a continuous service
electromagnet being anchored to the ground.
This device remains energized throughout the actuator operation time, and
allows the catch to stay lifted when it reaches the closing position, without
opposing any resistance; the catch will drop into position when the gate has
completed the closing cycle.
The electric lock can also be used to keep the block of the gate in case of
actuator malfunction or current failure.
8) ELECTRICAL INSTALLATION SET-UP
Lay out the electrical installation (fig. 16) with reference to the CEI 64-8 and
IEC 364 provisions, complying with the HD 384 and other national standards
in force for electrical installation. The mains power supply connections must
be kept totally separate from the service connections (photocells, electric
edges, control devices etc.).
WARNING! For connection to the mains, use a multipolar cable with
a minimum of 3x1.5mm
2
cross section and complying with the
previously mentioned regulations. For example, if the cable is out side
(in the open), it has to be at least equal to H07RN-F, but if it is on the
inside (or outside but placed in a plastic cable cannel) it has to be or
at least egual to H05VV-F with section 3x1.5mm
2
.
Connect the control and safety devices in compliance with the previously
mentioned electrical installation standards.
Fig.16 shows the number of connections and the cross section for power
supply cables having a length of approximately 100 metres; in case of
longer cables, calculate the cross section for the true automation load.
When the auxiliary connections exceed 50-metre lengths or go through
critical disturbance areas, it is recommended to decouple the control and
safety devices by means of suitable relays.
8.1) The main automation components are
(fig.16):
I
Type-approved omnipolar circuit breaker with at least 3mm contact
opening, provided with protection against overloads and short circuits,
suitable for cutting out automation from the mains. If not already installed,
place a type-approved differential switch with a 0.03A threshold in the
circuit just before the automation system.
Qr
Control panel and incorporated receiver.
SPL
Preheating board for operation with temperature lower than 5
°
C
(optional).
S
Key selector.
AL
Blinker with tuned antenna and RG58 cable.
M
Actuator.
E
Electric lock.
Fte
Pair of external photocells (transmitter).
Fre
Pair of external photocells (receiver).
Fti
Pair of internal photocells with CF posts.
Fri
Pair of internal photocells with CF posts (receiver).
T
1-2-4 channel transmitter.
IMPORTANT
: Before electrically activating the actuator, remove bleed
screw “S” (fig. 17) which is positioned under the base with articulated joint
and keep it for any later reuse. Only remove bleed screw “S” when the
actuator is installed.
9) MANUAL OPENING
In emergency case, such as in the case of power cut-out, to release the
gate, insert the same key C used for the adjustment of the by-pass valve
inside the triangular pin (Fig.18) and rotate it counterclockwise.
The gate can now be opened manually.
WARNING! make sure that you manually push the gate open at the
same speed as the motor would have.
To reset the electric operation of the actuator, turn the key in clockwise
direction until pin is blocked.
9.1) Mod. ORO
In case of emergency, for example when the electrical power is disconnected,
to release the gate, insert the same key C used for the adjustment of the by-
pass valve inside the triangular pin (Fig.18) and rotate it counterclockwise.
The gate can now be opened manually. To reset the electric operation of
the actuator, turn the key in clockwise direction until pin is blocked.
9.2) Mod. ORO/E
Since these models are reversible, for the manual operation of the gate it
is sufficient that the electric lock be opened with the appropriate key. To
make the manual manoeuvre easier, the lock can be released by means of
a triangular pin which can be reached using the appropriate key.
10) PUSHING FORCE ADJUSTMENT
The pushing force is adjusted by two valves marked with the writing “
Close
”
and “
Open
” respectively, which are used to adjust the closing and opening
pushing force (fig.19).
Lift open the lid indicated in (Fig.19) there you will find the two valves.
WARNING! For connection to the mains power supply, use a multicore
cable with a cross-sectional area of at least 3x1.5mm
2
of the kind
provided for by the regulations in force.
To connect the motors, use a cable with a cross-sectional area of at
least 1.5mm
2
of the kind provided for by the regulations in force.
The cable must be type H05RN-F at least.
26 -
ORO - ORO E
D811247_05
Содержание ORO
Страница 9: ...ORO Ver 03 31 Fig 19 Fig 18 Fig 17 a b S C CLOSE OPEN 20 ORO ORO E D811247_05 ...
Страница 14: ...ITALY ...