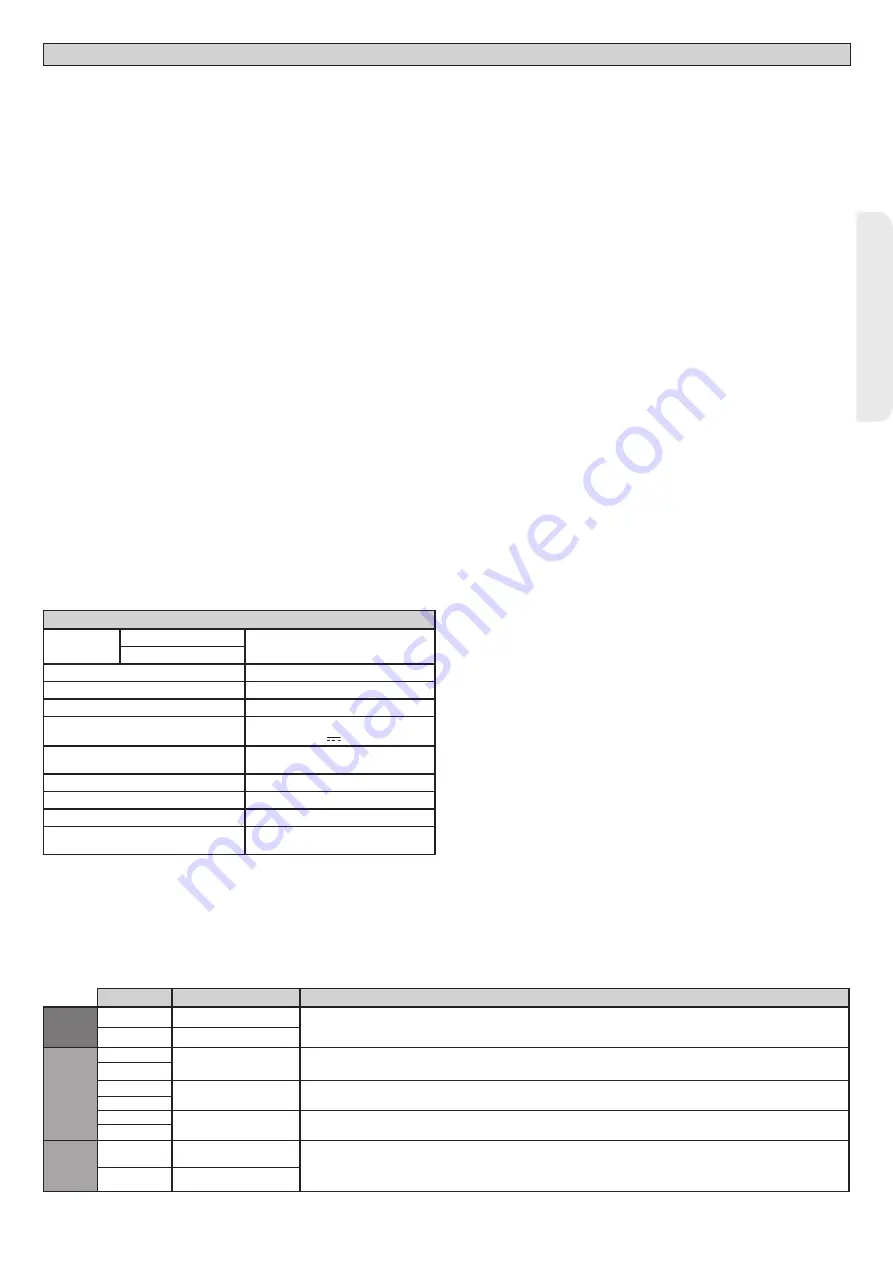
D812123 00100_02
CLONIX U-LINK
15
ENGLISH
INSTALLATION MANUAL
INSTALLER WARNINGS
Anything that is not explicitly provided for in the installation ma-
nual is not allowed. The operator’s proper operation can only be
guaranteed if the information given is complied with. The Firm shall
not be answerable for damage caused by failure to comply with the
instructions featured herein.
While we will not alter the product’s essential features, the Firm reserves
the right, at any time, to make those changes deemed opportune to
improve the product from a technical, design or commercial point of
view, and will not be required to update this publication accordingly.
WARNING! Important safety instructions. Carefully read and comply with
all the warnings and instructions that come with the product as incorrect
installation can cause injury to people and animals and damage to property.
The warnings and instructions give important information regarding safety,
installation, use and maintenance. Keep hold of instructions so that you can
attach them to the technical file and keep them handy for future reference.
GENERAL SAFETY
This product has been designed and built solely for the purpose indicated herein.
Uses other than those indicated herein might cause damage to the product and
create a hazard.
- The units making up the machine and its installation must meet the requirements
of the following European Directives, where applicable: 2004/108/EC, 2006/95/
EC, 2006/42/EC, 89/106/EC, 99/05/EC and later amendments. For all countries
outside the EEC, it is advisable to comply with the standards mentioned, in ad-
dition to any national standards in force, to achieve a good level of safety.
- The Manufacturer of this product (hereinafter referred to as the “Firm”) disclaims
all responsibility resulting from improper use or any use other than that for
which the product has been designed, as indicated herein, as well as for failure
to apply Good Practice in the construction of entry systems (doors, gates, etc.)
and for deformation that could occur during use.
- Installation must be carried out by qualified personnel (professional installer,
according to EN 12635), in compliance with Good Practice and current code.
- Before installing the product, make all structural changes required to produce
safety gaps and to provide protection from or isolate all crushing, shearing and
dragging hazard areas and danger zones in general in accordance with the
provisions of standards EN 12604 and 12453 or any local installation standards.
Check that the existing structure meets the necessary strength and stability
requirements.
- Before commencing installation, check the product for damage.
- The Firm is not responsible for failure to apply Good Practice in the construction
and maintenance of the doors, gates, etc. to be motorized, or for deformation
that might occur during use.
- Make sure the stated temperature range is compatible with the site in which the
automated system is due to be installed.
- Do not install this product in an explosive atmosphere: the presence of flammable
fumes or gas constitutes a serious safety hazard.
- Disconnect the electricity supply before performing any work on the system.
Also disconnect buffer batteries, if any are connected.
- Before connecting the power supply, make sure the product’s ratings match the
mains ratings and that a suitable residual current circuit breaker and overcur-
rent protection device have been installed upline from the electrical system.
Ensure that there is an automation, switch or 16A all-pole thermal magnetic
circuit breaker on the grid to enable complete disconnection in the conditions
of overvoltage III category.
- Make sure that upline from the mains power supply there is a residual current
circuit breaker that trips at no more than 0.03A as well as any other equipment
required by code.
- Make sure the earth system has been installed correctly: earth all the metal parts
belonging to the entry system (doors, gates, etc.) and all parts of the system
featuring an earth terminal.
- Installation must be carried out using safety devices and controls that meet
standards EN 12978 and EN 12453.
- Impact forces can be reduced by using deformable edges.
- In the event impact forces exceed the values laid down by the relevant standards,
apply electro-sensitive or pressure-sensitive devices.
- Apply all safety devices (photocells, safety edges, etc.) required to keep the
area free of impact, crushing, dragging and shearing hazards. Bear in mind the
standards and directives in force, Good Practice criteria, intended use, the instal-
lation environment, the operating logic of the system and forces generated by
the automated system.
- Apply all signs required by current code to identify hazardous areas (residual
risks). All installations must be visibly identified in compliance with the provisions
of standard EN 13241-1.
-
Once installation is complete, apply a nameplate featuring the door/gate’s data.
- This product cannot be installed on leaves incorporating doors (unless the motor
can be activated only when the door is closed).
- If the automated system is installed at a height of less than 2.5 m or is accessible,
the electrical and mechanical parts must be suitably protected.
- Install any fixed controls in a position where they will not cause a hazard, away
from moving parts. More specifically, hold-to-run controls must be positioned
within direct sight of the part being controlled and, unless they are key operated,
must be installed at a height of at least 1.5 m and in a place where they cannot
be reached by the public.
- Apply at least one warning light (flashing light) in a visible position, and also
attach a Warning sign to the structure.
- Attach a label near the operating device, in a permanent fashion, with informa-
tion on how to operate the automated system’s manual release.
- Make sure that, during operation, mechanical risks are avoided or relevant
protective measures taken and, more specifically, that nothing can be banged,
crushed, caught or cut between the part being operated and surrounding parts.
- Once installation is complete, make sure the motor automation settings are
correct and that the safety and release systems are working properly.
- Only use original spare parts for any maintenance or repair work. The Firm dis-
claims all responsibility for the correct operation and safety of the automated
system if parts from other manufacturers are used.
- Do not make any modifications to the automated system’s components unless
explicitly authorized by the Firm.
- Instruct the system’s user on what residual risks may be encountered, on the
control systems that have been applied and on how to open the system manu-
ally in an emergency. give the user guide to the end user.
- Dispose of packaging materials (plastic, cardboard, polystyrene, etc.) in accord-
ance with the provisions of the laws in force. Keep nylon bags and polystyrene
out of reach of children.
WIRING
WARNING! For connection to the mains power supply, use: a multicore cable with
a cross-sectional area of at least 5x1.5mm
2
or 4x1.5mm
2
when dealing with three-
phase power supplies or 3x1.5mm
2
for single-phase supplies (by way of example,
type H05 VV-F cable can be used with a cross-sectional area of 4x1.5mm
2
). To con-
nect auxiliary equipment, use wires with a cross-sectional area of at least 0.5 mm
2
.
- Only use pushbuttons with a capacity of 10A-250V or more.
- Wires must be secured with additional fastening near the terminals (for example,
using cable clamps) in order to keep live parts well separated from safety extra
low voltage parts.
- During installation, the power cable must be stripped to allow the earth wire
to be connected to the relevant terminal, while leaving the live wires as short
as possible. The earth wire must be the last to be pulled taut in the event the
cable’s fastening device comes loose.
WARNING! safety extra low voltage wires must be kept physically separate from
low voltage wires.
Only qualified personnel (professional installer) should be allowed to access
live parts.
CHECKING THE AUTOMATED SYSTEM AND MAINTENANCE
Before the automated system is finally put into operation, and during maintenance
work, perform the following checks meticulously:
- Make sure all components are fastened securely.
- Check starting and stopping operations in the case of manual control.
- Check the logic for normal or personalized operation.
- For sliding gates only: check that the rack and pinion mesh correctly with 2 mm
of play along the full length of the rack; keep the track the gate slides on clean
and free of debris at all times.
- For sliding gates and doors only: make sure the gate’s running track is straight
and horizontal and that the wheels are strong enough to take the weight of the
gate.
- For cantilever sliding gates only: make sure there is no dipping or swinging
during operation.
- For swing gates only: make sure the leaves’ axis of rotation is perfectly vertical.
-For barriers only: before opening the door, the spring must be decompressed
(vertical boom).
- Check that all safety devices (photocells, safety edges, etc.) are working properly
and that the anti-crush safety device is set correctly, making sure that the force
of impact measured at the points provided for by standard EN 12445 is lower
than the value laid down by standard EN 12453.
- Impact forces can be reduced by using deformable edges.
- Make sure that the emergency operation works, where this feature is provided.
- Check opening and closing operations with the control devices applied.
- Check that electrical connections and cabling are intact, making extra sure that
insulating sheaths and cable glands are undamaged.
- While performing maintenance, clean the photocells’ optics.
- When the automated system is out of service for any length of time, activate the
emergency release (see “EMERGENCY OPERATION” section) so that the operated
part is made idle, thus allowing the gate to be opened and closed manually.
- If the power cord is damaged, it must be replaced by the manufacturer or their
technical assistance department or other such qualified person to avoid any risk .
- If “D” type devices are installed (as defined by EN12453), connect in unverified
mode, foresee mandatory maintenance at least every six months
- The maintenance described above must be repeated at least once yearly or at
shorter intervals where site or installation conditions make this necessary.
WARNING!
Remember that the drive is designed to make the gate/door easier to use and
will not solve problems as a result of defective or poorly performed installation
or lack of maintenance
SCRAPPING
Materials must be disposed of in accordance with the regulations in
force. Do not throw away your discarded equipment or used batteries
with household waste. You are responsible for taking all your waste
electrical and electronic equipment to a suitable recycling centre.
DISMANTLING
If the automated system is being dismantled in order to be reassembled at another
site, you are required to:
- Cut off the power and disconnect the whole electrical system.
- Remove the actuator from the base it is mounted on.
- Remove all the installation’s components.
- See to the replacement of any components that cannot be removed or happen
to be damaged.
THE DECLARATION OF CONFORMITY CAN bE vIEWED ON THIS WEbSITE:
WWW.bFT.IT IN THE PRODUCT SECTION.
AVVERTENZE PER L’INSTALLATORE D812160_01
2) GENERAL OUTLINE
The Clonix U-Link receiver is supplied by the manufacturer with stan-
dard settings. Any change must be made using the programmer with
built-in display or universal handheld programmer. Fully supports
U-LINK protocol.
Its main features are:
- Built-in rolling-code or fixed code radio receiver with transmitter cloning
to manage up to 2048 codes.
- 3 input slots managed to house up to 3 boards with U-Link protocol.
- 2 or 3 relays/outputs settable as non-latching, latching, timed and panic
managed.
- Password protected receiver.
The Clonix U-Link receiver combines the characteristics of utmost safety
in copying variable code (rolling code) coding with the convenience of
carrying out transmitter “cloning” operations thanks to an exclusive system.
Cloning a transmitter means creating a transmitter which can be included
automatically within the list of the transmitters memorised in the recei-
ver, either as an addition or as a replacement of a particular transmitter.
Therefore it will be possible to remotely program a large number of
additional transmitters, or for example, replacement transmitters for
those which have been lost, without making changes directly to the
receiver. Cloning by replacement is used to create a new transmitter
which takes the place of the one previously memorised in the receiver;
in this way the lost transmitter is removed from the memory and will
no longer be usable
When coding safety is not a decisive factor, the receiver allows you to
carry out fixed code additional cloning, which although abandoning the
variable code, provides a high number of coding combinations.
Using clones when there is more than one receiver (as in the case of
communal buildings),
and especially when a distinction is to be made between clones to be
added to or replaced in individual or collective receivers, could turn out
to be rather difficult. The receiver cloning system for communal buildings
makes it particularly easy to solve the problem of clone storage for up
to 250 individual receivers.
Entrance control is managed by relays. Two relays in N.O. configuration
are available in the 2E version while there are 3 relays in the UNI version,
two with N.O contact while the third has N.O. or N.C. contact based on
the configuration the user sets with the jumper.
3) TECHNICAL SPECIFICATIONS
Power supply
CLONIX UNI AC U-LINK 230
220-230V~ 50/60 Hz*
CLONIX 2E AC U-LINK 230
Operating temperature range
-10/+60°C
Protection rating
IP 55**
Antenna impedance
50 Ohm (Rg58)
OUT 1 , OUT 2 , OUT 3 ***
NO contact
(120V~/1A, 24V /max 1A)
Max. n° of radio transmitters that can
be memorized
2048
N° of combinations
4 billion
Dielectric rigidity
3750V~ for 1 minute
Built-in Rolling-Code radio-receiver
frequency 433.92MHz
Setting of parameters and options
Universal handheld programmer/
LCD display
(*) other voltages to order
(**) only guaranteed when using the appropriate cable glands
(***) three outputs only in the UNI
4) TERMINAL BOARD WIRING Fig. B
WARNINGS - When performing wiring and installation, refer to the
standards in force and, whatever the case, apply good practice principles.
Wires carrying different voltages must be kept physically separate from
each other, or they must be suitably insulated with at least 1mm of ad-
ditional insulation.
Wires must be secured with additional fastening near the terminals,
using devices such as cable clamps.
All connecting cables must be kept far enough away from the dissipater.
WARNING! For connection to the mains power supply, use a multicore
cable with a cross-sectional area of at least 3x1.5mm
2
of the kind
provided for by the regulations in force.
5) CALLING UP MENUS: FIG. 1
5.1) RADIO MENU (radio) (RADIO TABLE “A”)
- IMPORTANT NOTE: THE FIRST TRANSMITTER MEMORIZED MUST
BE IDENTIFIED BY ATTACHING THE KEY LABEL (MASTER).
In the event of manual programming, the first transmitter assigns the
RECEIVER’S KEY CODE: this code is required to subsequently clone the
radio transmitters.
The Clonix built-in on-board receiver also has a number of important advanced
features:
• Cloning of master transmitter (rolling code or fixed code).
• Cloning to replace transmitters already entered in receiver.
• Transmitter database management.
• Receiver community management.
To use these advanced features, refer to the universal handheld
programmer’s instructions and to the general receiver programming guide.
5.2) OUTPUT CONFIGURATION MENU (
OUTPUTS
) (OUTPUT TABLE “B”)
5.3) LOGIC MENU (
LOGIC
) (LOGIC TABLE “C”)
5.4) SLOTS CONFIGURATION MENU (
conf.slots
) (INPUT TABLE “D”)
5.5) MENU DEFAULT (
default
)
Riporta la centrale ai valori preimpostati dei DEFAULT.
5.6) MENU LINGUA (
lingua
)
Consente di impostare la lingua del programmatore a display.
5.7) STATISTICS MENU (
stat
)
Displays the board version and number of saved transmitters.
5.8) PASSWORD MENU (
PASSWORD
)
Used to set a password for the board’s wireless programming via the
U-link network.
With “PROTECTION LEVEL” logic set to 1,2,3,4, the password is required
to access the programming menus. After 10 consecutive failed attempts
to log in, you will need to wait 3 minutes before trying again. During
this time, whenever an attempt is made to log in, the display will read
“BLOC”. The default password is 1234.
6) CONNECTION WITH EXPANSION BOARDS AND UNIVERSAL HAND-
HELD PROGRAMMER VERSION> V1.40 (Fig. D) Refer to specific manual.
7) RESTORING FACTORY SETTINGS Fig. D
WARNING: this operation will restore the control unit’s factory
settings and all transmitters stored in its memory will be deleted.
- Cut off power to the board.
- Press the +, - and OK keys together.
- Switch on the board’s power.
- The display will read RST; confirm within 3 sec. by pressing the OK key.
- Wait for the procedure to finish.
Terminal
Definition
Description
Po
w
er
supply
L
LINE
See Par. 3) Technical Specifications Table
N
NEUTRAL
O
utputs
20
OUT 1
OUT 1 configurable output - Default setting NON-LATCHINg.
NON-LATCHINg; LATCHINg; ANTIPANIC.
Refer to the OUTPUT CONFIgURATION table.
21
22
OUT 2
OUT 2 configurable output - Default setting NON-LATCHINg.
NON-LATCHINg; LATCHINg; ANTIPANIC.
Refer to the OUTPUT CONFIgURATION table.
23
24
OUT 3*
OUT 3 configurable output - Default setting NON-LATCHINg.
NON-LATCHINg; LATCHINg; ANTIPANIC. Refer to the OUTPUT CONFIgURATION table.
25
A
nt
enna
Y
ANTENNA
Antenna input.
Use an antenna tuned to 433MHz. Use Rg58 coax cable to connect the Antenna and Receiver. Metal bodies close to the an-
tenna can interfere with radio reception. If the transmitter’s range is limited, move the antenna to a more suitable position.
#
SHIELD
* only on CLONIX UNI AC U-LINK 230.
Содержание CLONIX 2E AC U-LINK 230
Страница 43: ......