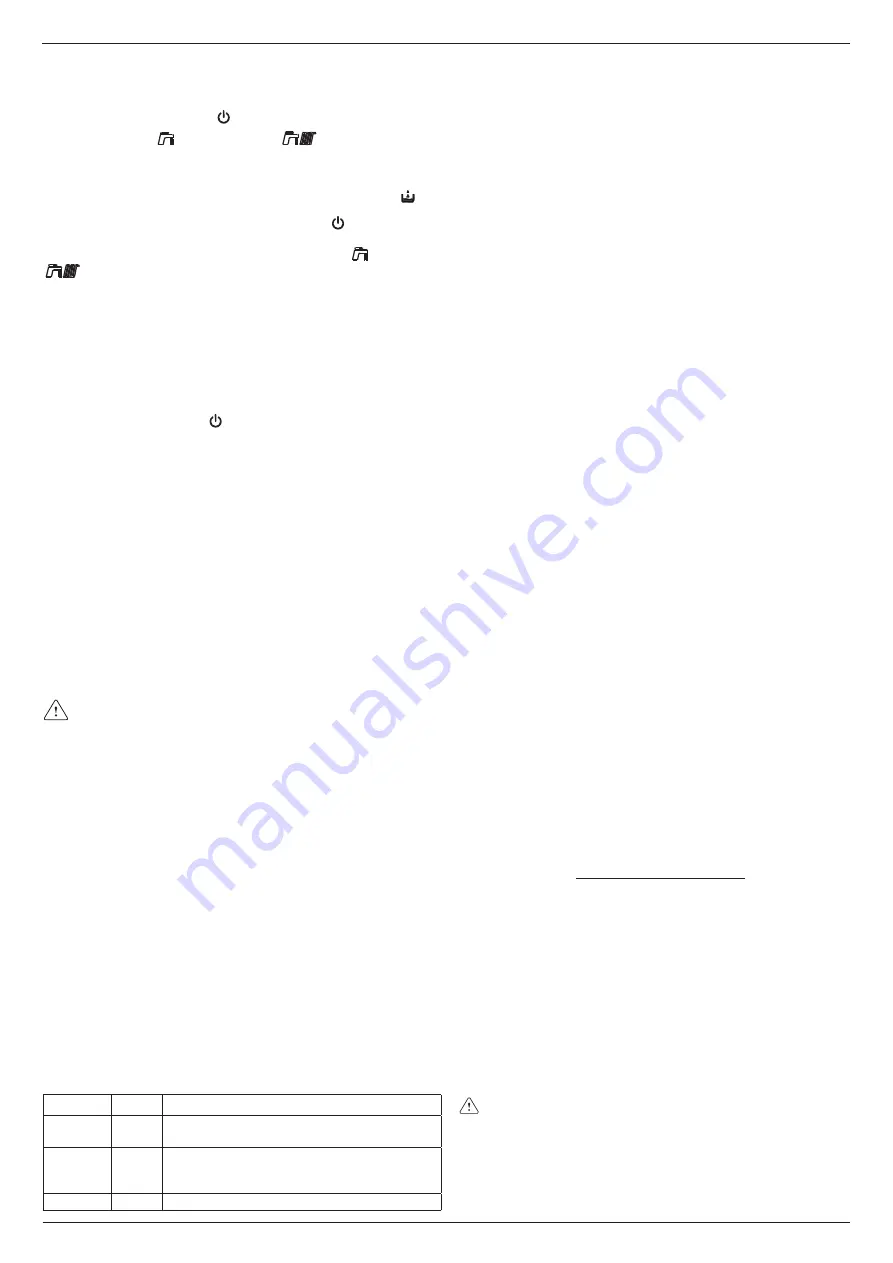
9
8
ENGLISH
QUADRA GREEN 25 R.S.I.
4.3 Light signals and faults
To restore operation (deactivate alarms):
Faults A 01-02-03
Position the function selector to (OFF), wait 5-6 seconds then set it to
the required position
(summer mode) or
(winter mode).
If the reset attempts do not reactivate the boiler, contact the Technical As-
sistance Centre.
Fault A04
In addition to the fault code, the digital display shows the symbol .
Check the pressure value indicated by the water gauge:
if it is less than 0.3 bar, position the function selector to (OFF) and adjust
the filling tap until the pressure reaches a value between 1 and 1.5 bar.
Then position the mode selector to the desired position
(summer) or
(winter). The boiler will perform one purge cycle lasting approxi-
mately 2 minutes. If pressure drops are frequent, request the intervention of
the Technical Assistance Service.
Fault A06
Contact the Technical Assistance Centre.
Fault A07
Contact the Technical Assistance Centre.
Fault A08
Contact the Technical Assistance Centre.
Fault A09 with fixed red LED lit
Position the function selector to (OFF), wait 5-6 seconds then set it to the
required position (summer mode) or (winter mode).
If the reset attempts do not reactivate the boiler, request the intervention of
the Technical Assistance Service.
Fault A09 with flashing red and green LEDs
The boiler is equipped with an auto-diagnostic system which, based on the
total number of hours in certain operating conditions, can signal the need
to clean the primary exchanger
(alarm code 09 with flashing red and green
LEDs and flue gas meter >2,500).
Once the cleaning operation has been completed, using the special kit sup-
plied as an accessory, the total hour meter will need to be reset to zero as
follows:
- switch off the power supply
- remove the housing
- loosen the fixing screw then turn the instrument panel
- loosen the fixing screws on the cover (
F
) to access the terminal board (fig. 16)
- while the boiler is powered up, using a small screwdriver included, press
the CO button (fig. 26) for at least 4 seconds, to check the meter has
been reset, power down then power up the boiler; the meter reading is
shown on the monitor after the “-C-” sign.
Live electrical parts.
Note: the meter resetting procedure should be carried out after each in-
depth cleaning of the primary exchanger or if this latter is replaced. To
check the status of the total hour meter, multiply the reading by 100 (e.g.
reading of 18 = 1800 total hours; reading of 1 = 100 total hours).
The boiler continues to operate normally even when the alarm is activated.
Fault A77
This is an automatic-reset fault, if the boiler does not restart, contact the
Technical Assistance Centre.
Flashing yellow LED
Combustion analysis in progress.
4.4 Alarm records
The “ALARM RECORDS” function starts automatically once the display has
been on for 2 hours, or immediately by setting the P1 parameter to 1.
The records include all the latest alarms, up to a maximum of 5 alarms, and
they are displayed in sequence by pushing and releasing the P1 button on
the display board. If the records are empty (P0=0) or if tracking the same is
disabled (P1=0), the display function is not available.
Alarms are displayed in reverse order compared to the order in which they
occurred: this means that the last alarm generated is the first to be display
-
ed. To delete the alarms records, simply set parameter P0 to 0.
NOTE:
To get to the P1 button the cover on the control panel must be remo-
ved and the display board must be identified (fig. 36a).
PROGRAMMING PARAMETERS
Functioning of the display can be personalised by programming three pa-
rameters:
Parameter Default
Description
P0
0
Deletion of alarms records
(0 = records empty/1 = records not empty)
P1
0
Immediate activation of alarm record management
(0 = delayed records management activated/
1 = immediate records management activated
P2
0
Do not change
When button P1 on the display (fig. 36a) is held down for at least 10 sec,
the programming procedure is activated. The three parameters, with their
respective values, are shown in rotation on the display (fig. 36b). To edit a
parameter value, simply push the P1 button again when the required para-
meter is displayed, and then hold it down until the value switches from 0 to
1 or vice-versa (approx. 2 sec).
The programming procedure is closed automatically after 5 minutes, or if
there is an electrical power failure
4.5 Boiler configuration
There is a series of jumpers (JPX) available on the electronic board which
enable the boiler to be configured.
To access the board, proceed as follows:
- turn off the main switch on the system
- loosen the fixing screws on the housing, move the base of the housing
forwards and then upwards to unhook it from the chassis
- undo the fixing screws (
E
) from the instrument panel (fig. 14)
- loosen the screws (
F
- fig. 16) to remove the cover of the terminal board
(230V).
JUMPER JP7 - fig. 37:
preselection of the most suitable heating temperature adjustment field ac
-
cording to the installation type.
Jumper not inserted - standard installation
Standard installation 40-80°C
Jumper inserted - floor installation
Floor installation 20-45°C.
In the manufacturing phase, the boiler is configured for standard installations.
JP1
Calibration (Range Rated)
JP2
Reset heating timer
JP3
Calibration (see paragraph on “Adjustments”)
JP4
Do not use
JP5
Heating only function with a predisposition for external storage tank
with thermostat (JP8 inserted) or probe (JP8 not inserted)
JP6
Enable night-time compensation function and continuous pump (only
with external sensor connected)
JP7
Enable management of low temperature/standard installations (see above)
JP8
Management of an external storage tank with thermostat enabled
(jumper inserted)/ management of an external storage tank with pro-
be (jumpers not inserted) fig. 37.
The boiler foresees jumpers JP5 and JP8 inserted as standard (heating
only version arranged for storage tank with thermostat); if the use of an
exterior storage tank with probe is required, jumper JP8 must be removed.
4.6 Setting the thermoregulation (graphs 1-2-3)
The thermoregulation only operates with the external sensor connected;
once installed, connect the external sensor (accessory available on request)
to the special terminals provided on the boiler terminal board (fig. 5).
This enables the THERMOREGULATION function.
Selecting the compensation curve
The compensation curve for heating maintains a theoretical temperature of
20°C indoors, when the external temperature is b20°C and -20°C.
The choice of the curve depends on the minimum external temperature
envisaged (and therefore on the geographical location), and on the delivery
temperature envisaged (and therefore on the type of system). It is carefully
calculated by the installer on the basis of the following formula:
envisaged delivery T. - Tshift
KT=
20- min. envisaged external T.
Tshift = 30°C standard installations
25°C floor installations
If the calculation produces an intermediate value between two curves, you
are advised to choose the compensation curve nearest the value obtained.
Example: if the value obtained from the calculation is 1,3 this is between
curve 1 and curve 1,5. Choose the nearest curve, i.e. 1,5.
Select the KT using trimmer
P3
on the board (see multiwire wiring diagram).
To access
P3
:
- remove the housing,
- loosen the fixing screw on the instrument panel
- turn the instrument panel towards you
- loosen the fixing screws on the terminal board cover
- unhook the board casing
Live electrical parts.
The KT values which can be set are as follows:
standard installation: 1,0-1,5-2,0-2,5-3,0
floor installation 0,2-0,4-0,6-0,8
and these are displayed for approximately 3 seconds after rotation of the
trimmer P3.
Содержание 20084408
Страница 2: ...2...