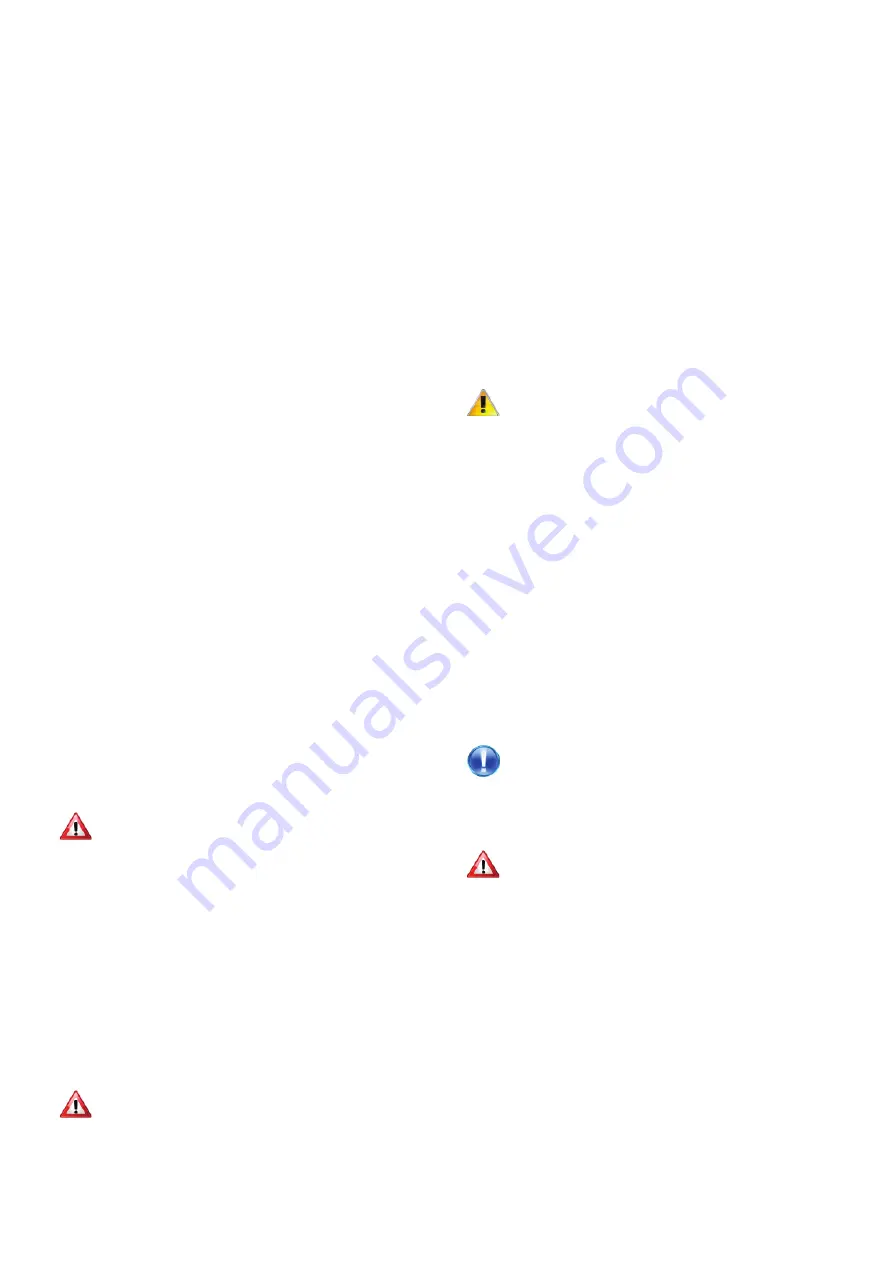
eff ective when located as close to the working area as
possible. However care should be exercised to avoid directing
the discharged air directly onto the occupants of the area to
be heated.
On exposed walls heaters should be positioned so as to
discharge towards, or along the length of the exposed wall. In
areas where it is proposed that more than one heater is to be
installed, a general scheme of circulation should be drawn up
and maintained, thereby off ering the best heat distribution.
Air pressure within the area heated and the outside air
pressure must remain the same, factors infl uencing this would
be the presence of extraction systems, ventilation systems,
and various types of process plant. OUHA 60-100 models can
be installed to allow the fans to work in opposite directions.
This enables the heater to be installed centrally in the area to
be heated and allows warm air to be discharged to both the
front and rear of the heater.
The heater must be installed on a fl at and level surface made
from non-combustible material, which is suffi
ciently robust
to withstand the weight of the heater and any ancillary
equipment. Any combustible material adjacent to the heater
or fl ue system must be so placed or shielded so that its surface
temperature does not exceed 65°C.
In areas where it is proposed that more than one heater is to
be installed, a general scheme of circulation should be drawn
up and maintained, thereby off ering the best heat distribution
All
Suspended Oil fi red Unit Heaters are fi tted with a pressure
relief facility, this is incorporated into the design of the fl ue gas
exit duct.
Care should therefore be taken in siting service connections
and controls well away from the pressure relief vent.
Warning
Under no circumstances must the pressure relief be
restricted, blocked, or have the free exit of exhaust gas
impaired or re-directed.
1.9
Fuel supply - general
The
Suspended Oil fi red Unit Heater range are all
manufactured and pre-set for use with either 28 second or
35 second gas oil delivered to the burner via a suitable piped
system from the oil storage tank.
Galvanised or plastic pipe work and fi ttings must
not be used. (see BS 5410 Part 1 1997)
The constraints of the application will, to a large extent,
determine whether it is preferable to use a single pipe gravity
feed system, or whether the two pipe pumped system is more
appropriate.
Where more than one appliance is to share a common supply
it will be necessary to use a pressurised ring main system.
All pipe work must be constructed and installed so that it does
not permit the ingress of air.
The construction, size, and position of the oil storage tank
must take account of the current regulations, as well as suiting
the requirements of the installation.
Please refer to pages 9 and 10 for additional information.
Caution
On pumped systems always check that the pump is correctly
set up prior to running, and always ensure that valves are
open allowing a free fl ow of oil through the system.
1.9.1 Fuel
In order to promote trouble free operating it is necessary that
the oil within the storage tank and oil line does not fall below
the cold fi lter plugging point (cfpp), in this country and with
class D fuel (also referred to as gas oil). The critical
temperature is -4°C for this summer grade.
The cfpp critical temperature for the winter grade is -12°C.
If summer grade fuel is stored for winter use in areas prone
to severe frosts and low temperatures it will be necessary to
insulate or even heat the supply tank and pipe work.
Note
The fuel supplier should be contacted prior to installation so
that any requirements concerning delivery, transport, storage
and use can be addressed before work commences.
Warning
The inlet pump pressure must not exceed a maximum of 0.4
bar, this is because beyond this point gas is liberated from the
oil.
1.9.2 Storage tank
An externally painted steel storage tank to BS 799 part 5 1987
or a medium density polyethylene oil tank OFTEC certifi ed
to OFS T-100 may be used. Local, national, European and fi re
regulations must also be complied with and must include:
•
A fuel level gauge (not made from glass) a vent pipe
with a diameter greater than that of the fi ller and
featuring a weatherproof termination.
•
A sludge valve.
Содержание OUH 2 100
Страница 20: ...Wiring Diagram 33 65 245 Models OUHA OUHC40 ON OFF Riello Oil Fried Burner...
Страница 21: ...Wiring Diagram 33 65 246 Models OUHA 60 70 ON OFF Riello Oil Fried Burner...
Страница 22: ...Wiring Diagram 73 65 010 Models OUHA 90 100 ON OFF Riello Oil Fried Burner...
Страница 23: ...Wiring Diagram 33 65 247 Models OUHC 60 100 ON OFF Riello Oil Fried Burner...
Страница 24: ...Wiring Diagram 33 65 248 Models OUHA OUHC 40 HI LOW Riello Oil Fried Burner...
Страница 25: ...Wiring Diagram 33 65 249 Models OUHA 60 70 HI LOW Riello Oil Fried Burner...
Страница 26: ...Wiring Diagram 73 65 011 Models OUHA 90 100 HI LOW Riello Oil Fried Burner...
Страница 27: ...Wiring Diagram 33 65 250 Models OUHC 60 100 HI LOW Riello Oil Fried Burner...
Страница 28: ...Remote Connections 33 65 132 ON OFF HI LOW Less Controls Remote Connections 33 65 228 ON OFF to SmartCom SC3 SZ...
Страница 29: ...Remote Connections 33 65 229 HI LOW to SmartCom SC3 MZ Remote Connections 33 65 131 ON OFF HI LOW to CP4...
Страница 35: ...Turbulator positions in models 40 70 8 off Turbulator positions in models 90 100 12 off...
Страница 43: ...Notes...