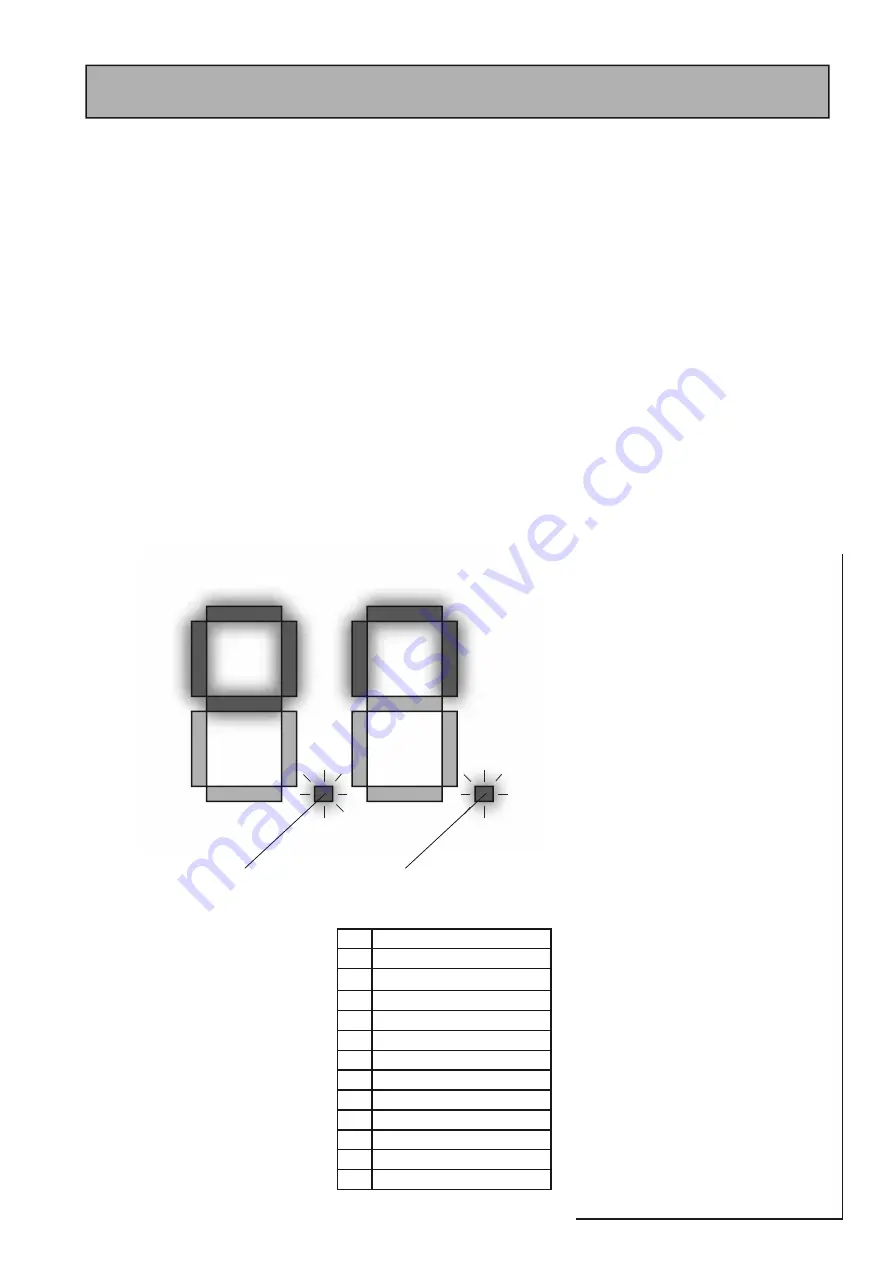
Page 31
BOILERMA
TE
A-CL
ASS
OV
2.3 COMMISSIONING
2.0 INSTALLATION
Once the system is fi nally fi lled turn down the servicing valve for the ballvalve
in the F & E cistern to the point where the warning/overfl ow will cope with the
discharge arising from a ballvalve failure.
Cleansing Hot/Cold Water System Treatment
Fully fl ush and if necessary chlorinate the hot and cold water system in accordance
with the recommendations in the Model Water Byelaws and BS 6700.
Note: Incorrect chlorination will damage the plate heat exchanger so care must
be taken that the system is fully fl ushed.
Commissioning the BoilerMate control system
For maximum system effi ciency the store thermostat must be in control of the boiler
i.e. the boiler cycles on the store thermostat and not on its integral thermostat. The
BoilerMate control system will automatically commission itself to match the actual
performance of the installed boiler. However the operation of the control system
should be checked as follows.
LED
Description
H1.1
Middle store sensor calling for heat
H1.2
Bottom store sensor calling for heat
H1.3
Spare
V1.1
HW Programmer calling for heat
V1.3
CH Programmer calling for heat
V1.4
Room thermostat calling for heat
H2.1
PHE pump on
H2.2
3 port valve on (for heating)
H2.3
Boiler/heating system pump on
V2.1
Boiler on
V2.2
Switch on / electric boost on
V2.4
Boiler boost mode on
Note: If both ‘dots’ are fl ashing then the
controller is working. However it is a
warning of limited/alternative control
functionality
@&LASHING
,OCKOUT&AILURE
@&LASHING
#ONTROLLERW
(
6
6
(
(
6
6
(
6
6
(
(
6
6
(a) Check that the BoilerMate front panel mode
rocker is in the ‘normal’ position. Put the hot
water control rocker in the constant position
and the central heating control rocker in the
off position.
(b) The boiler will not start i.e there will be
no 240V ac start signal at BoilerMate terminal
‘SL-B’ until:-
• The heating programmer calls for hot water
/heating which will bring display segment V1.1
on, and
• Store sensors are calling for heat which will
bring display segments H1.1 and H1.2 on (see
opposite)
(c) Set the boiler thermostat to maximum and
commission the boiler as per manufacturer’s
instruc tions and ensure that the flow
temperature reaches more than 77
o
C before
switching off. Display segments H2.3 and V2.1
will be on whilst the boiler is fi ring.
(d) Check and adjust the speed of the boiler
pump to provide a differential temperature of
about 11ºC across the fl ow and return when
the space heating is off.
(e) Check on the A.C.B. that the appliance
reaches a suitable temperature ie above 75ºC
(f ) To manually check the ‘switch’ electric
backup is working, move the mode rocker on
front panel display from ‘normal’ to ‘switch’
position. The electric backup operation can
now be checked. Draw a bath full of hot water
from the appliance to lower the temperature
and bring ‘switch’ into operation.
This is easily checked with the aid of a clamp
meter that should show a current drawn
of around 26 amp. If a suitable meter is not
available a bath full of hot water should be
drawn from the appliance after which the store
temperature should be noted. With no further
demand a rise in store temperature of 5 – 10
o
C
in about 15-20 minutes (dependent on store
size) should be observed. Display segment
V2.2 will be on whilst ‘Switch’ is working. Once
it has been proved that ‘switch’ is working move
the mode rocker switch back to the normal
position.
Содержание BoilerMate BMA 125 OV
Страница 45: ......