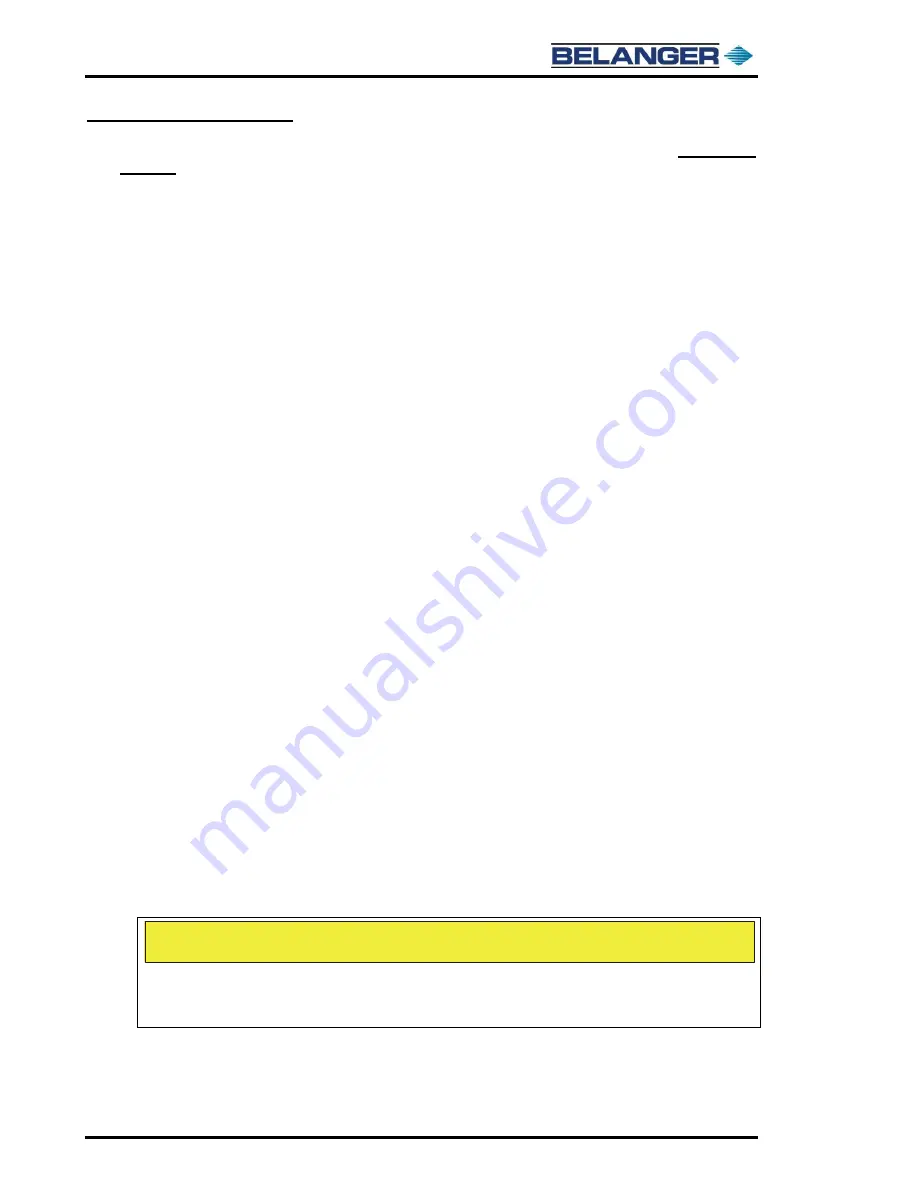
TopWinder
®
2
Belanger, Inc. ®* 1001 Doheny Ct. * Northville, MI 48167 * Ph (248) 349-7010 * Fax (248) 380-9681
1MANUL755
Operational Warning
Formulations containing the chemicals listed below are particularly dangerous and
should not
be used
even at low concentrations:
•
Hydrofluoric Acid
•
Ammonium Bi-fluoride
•
Bromic Acid
•
Muriatic Acid
•
Sulfonic Acid
•
Phosphoric Acid
•
Hydrogen Cyanide
•
Hydrochloric Acid
•
Chlorinated Solvents
Belanger, Inc.®, does not endorse or condone the use of chemicals that are potentially dangerous
to human health, the environment or property. Belanger® recognizes that it is the right and sole
decision of the end user operators of our equipment as to the type and dilution ratio of the
chemicals used in their facilities. We strongly recommend that the end user does not select
products containing any of the chemicals listed above as an ingredient in the wash solutions. The
chemicals listed above are potentially dangerous to human health, and have a detrimental,
deteriorating effect on the equipment and the facility. Be advised that a portion of, or all of your
warranty will be voided if you determine to use any of the chemicals listed above as an ingredient
in the wash solutions in conjunction with your Belanger® automatic car wash equipment:
Limitation (4), of Paragraph (8), Limited Warranty, of the Belanger® Terms and Conditions of
Sales describes the potential limitation of warranty due to your chemical selection:
(4) This warranty shall be void for all equipment failures and premature component wear
caused by the use of corrosive chemicals in the wash process. The following list includes
some, but not all, of the particularly corrosive chemicals that if used in conjunction with
Belanger® equipment will void the warranty: Hydrofluoric Acid, Ammonium Bi-fluoride, Bromic
Acid, Muriatic Acid, Sulfonic Acid, Phosphoric Acid, Hydrogen Cyanide, Hydrochloric Acid,
and Chlorinated Solvents. The Purchaser also agrees to accept the responsibility and liability
for the selection and use of any chemicals listed above;
However, should the end user decide to use formulations containing any of the above ingredients,
the end user should institute a comprehensive training program and implement detailed
operational parameters within their organization for the proper handling and treatment of such
products to minimize the potential dangers involved. Consult your chemical supplier for
assistance in establishing operational guidelines in the use of their products. MSDS (Material
Safety Data Sheet) should be obtained from the chemical supplier before using any chemical
formulation.
CAUTION
During the installation process the installer is responsible for re-tightening ALL
lugs, set screws and terminals located in the electrical panels. Components may
vibrate loose during shipping.