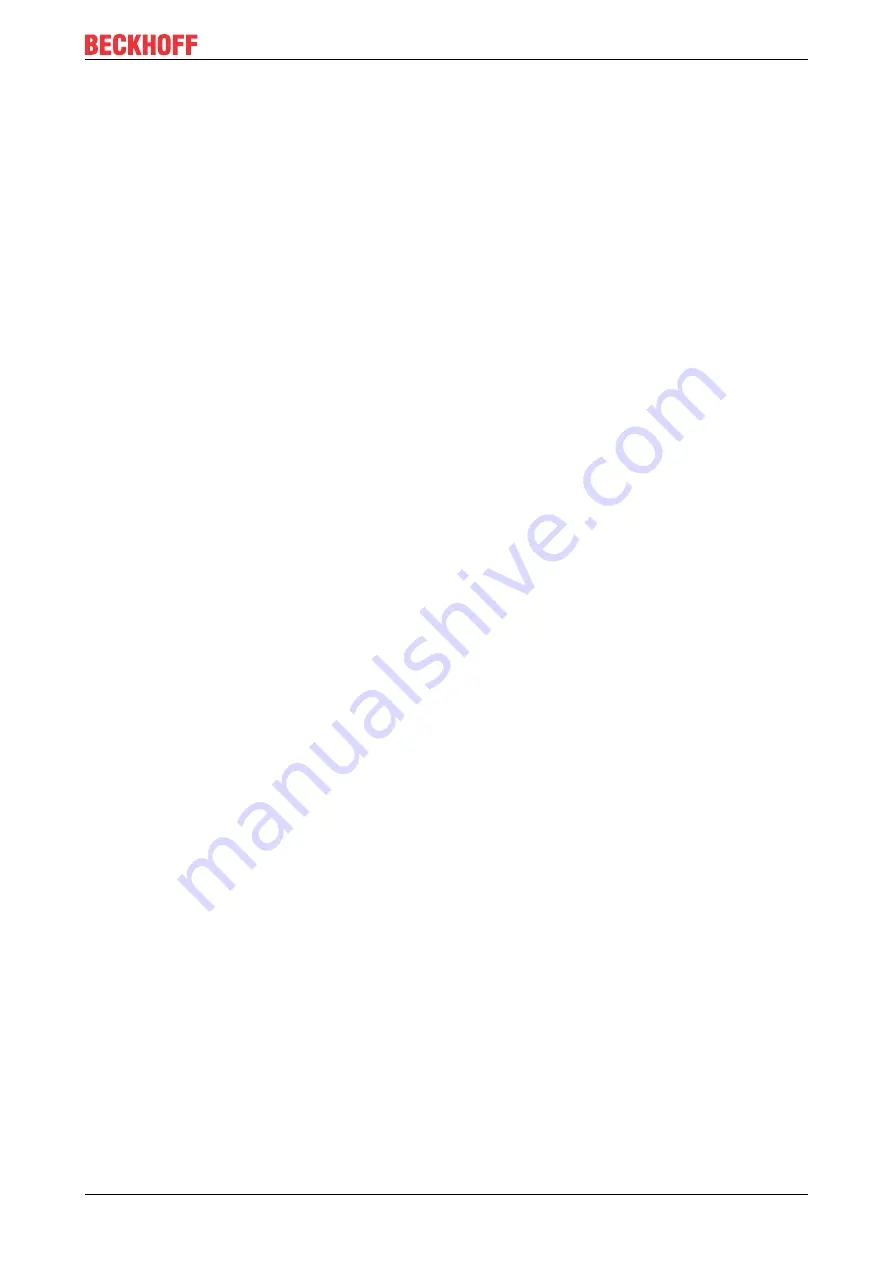
Product overview
EL72x1-901x
23
Version: 1.9
With a rated voltage up to 50 V
DC
and a rated current of up to 4.5 A, this enables the user to operate a
servomotor with a power of up to 276 W. Permanent magnet synchronous motors with a rated current of up
to 4.5 A can be connected as loads. The monitoring of numerous parameters, such as overvoltage and
undervoltage, overcurrent, terminal temperature or motor load, offers maximum operational reliability.
Modern power semiconductors guarantee minimum power loss and enable feedback into the DC link when
braking.
With the integration of a complete servo drive into a standard EL7201 EtherCAT Terminal only 12 mm wide,
Beckhoff is setting new standards in matters of size. This small manufactured size is possible thanks to the
latest semiconductor technology and the resulting very high power factor. And yet, despite the small
dimensions, nothing has to be sacrificed.
The integrated fast control technology, with a field-orientated current and PI speed control, supports highly
dynamic positioning tasks. Apart from the direct connection of motor and resolver, the connection of a motor
holding brake is also possible.
Connection to the control system
A further big advantage of the EL72x1-xxxx is the easy incorporation into the control solution. The complete
integration into the control system simplifies commissioning and parameterization. As with all the other
Beckhoff terminals, the EL72x1-xxxx is simply inserted into the terminal network. Then the full terminal
network can be scanned by the TwinCAT System Manager or manually added by the application engineer.
In the System Manager the EL72x1-xxxx can be linked with the TwinCAT NC and parameterized.
Scalable motion solution
The servo terminal complements the product range of compact drive technology for Beckhoff I/O systems
that are available for stepper motors, AC and DC motors. With the EL72x1-xxxx, the range of servo drives
becomes even more finely scalable: from the miniature servo drive up to 170 W in the EtherCAT Terminal
through to the AX5000 servo drive with 118 KW, Beckhoff offers a wide range including the servomotors.
The AM81xx series was specially developed for the servomotor terminal EL72x1-xxxx.
One Cable Technology (OCT)
In the servomotors from the AM8100-xF
2
x series the feedback signals are transmitted directly via the power
supply cable, so that power and feedback system are combined in a single motor connection cable. With the
use of the One Cable technology, the information is sent reliably and without interference through a digital
interface. Since a cable and plug are omitted at both the motor and controller end, the component and
commissioning costs are reduced.
Thermal I²T motor model
The thermal I²T motor model represents the thermal behavior of the motor winding taking into account the
absolute thermal resistance R
th
and the thermal capacity C
th
of motor and the stator winding.
The model assumes that the motor reaches its maximum continuous operating temperature T
nom
during
continuous operation with rated current I
nom
. This temperature corresponds to 100% motor load. During
operation at rated current the motor model reaches a load of 63% after a time of τ
th
=R
th
∙C
th
and slowly
reaches its continuous operating temperature.
If the motor is operated with a current that is greater than the rated current, the model reaches 100% load
more quickly.
If the load of the I²T model exceeds 100%, the requested set current is limited to the rated current, in order to
protect the motor winding thermally. The load reduces to a maximum of 100%. If the current falls below the
rated current, the load falls below 100% and the set current limitation is cancelled.
For a motor that has been cooled to ambient temperature, the time for reaching 100% load with a set current
that exceeds the rated current can be estimated with τ
th
∙I
nom
²/I
actual
².
The actual load must be known for exact calculation of the time when the 100% load threshold is exceeded.
Содержание EL72 1-901 Series
Страница 1: ...Documentation EL72x1 901x Servo Motor Terminals with OCT and STO 50 V DC 1 9 2020 02 18 Version Date...
Страница 2: ......
Страница 6: ...Table of contents EL72x1 901x 6 Version 1 9...
Страница 20: ...Product overview EL72x1 901x 20 Version 1 9 2 3 Technical data...
Страница 49: ...Installation EL72x1 901x 49 Version 1 9 Fig 36 Shield busbar Fig 37 Shield busbar clamp...
Страница 86: ...Commissioning EL72x1 901x 86 Version 1 9 Fig 88 Incorrect driver settings for the Ethernet port...
Страница 140: ...Commissioning EL72x1 901x 140 Version 1 9 0hex 80hex Fault reset 6hex Shutdown 7hex Switch on Fhex Enable operation...
Страница 141: ...Commissioning EL72x1 901x 141 Version 1 9 Fig 176 DS402 State Machine...
Страница 150: ...Commissioning EL72x1 901x 150 Version 1 9 Fig 184 Touch Probe inputs...
Страница 172: ...Commissioning EL72x1 901x 172 Version 1 9 Fig 207 Process Data tab SM2 EL72x1 0010 default...
Страница 256: ...Appendix EL72x1 901x 256 Version 1 9 9 5 Certificates Fig 233 EL72x1 9014_Certificate...