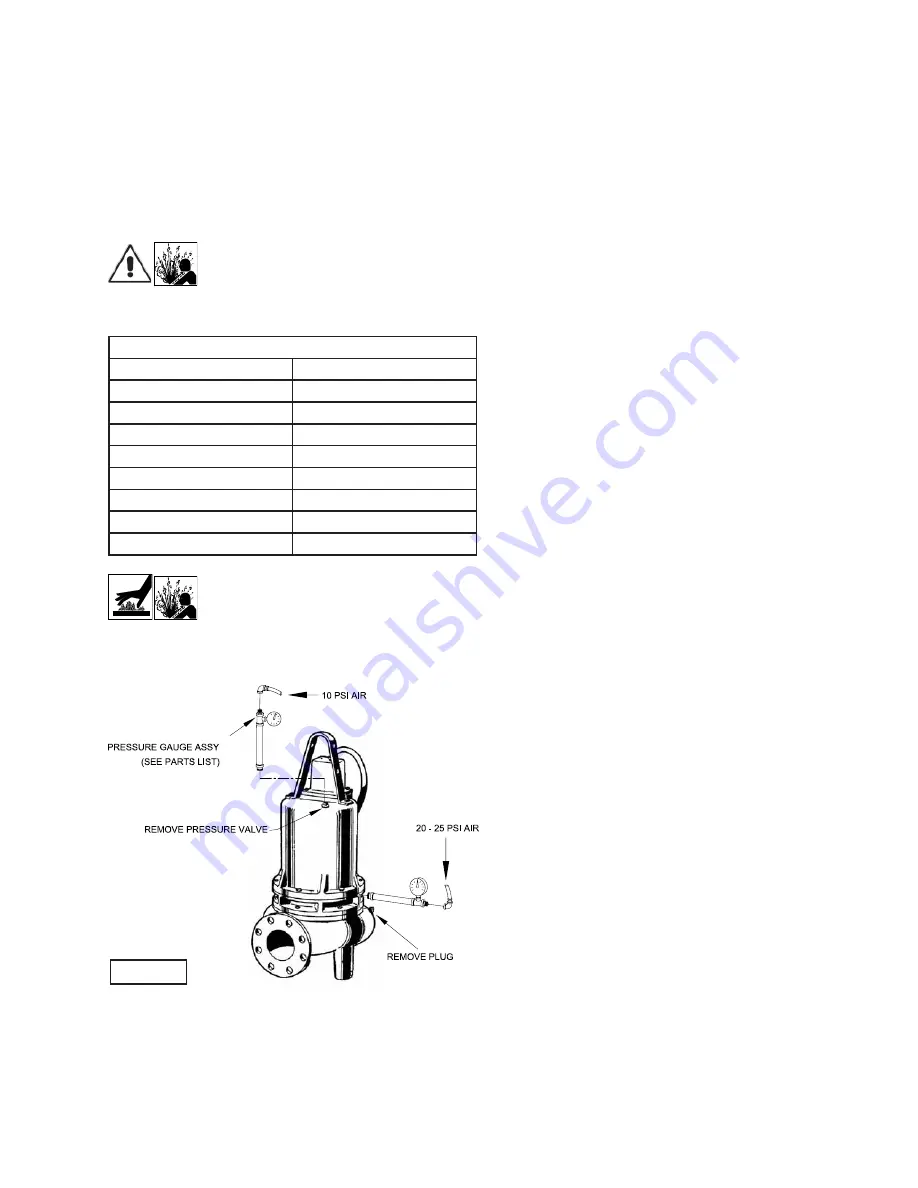
9
FIGURE 2
Set unit upright and fi ll only until the motor, as viewed through
the conduit box opening, is just covered and no more. Reas-
semble the O-ring (21), conduit box assembly (49) and cap
screws (23), apply thread locking compound (38) to each cap
screw (23) thread before installing. Torque cap screws (23) to
15 ft., lb.
Seal Chamber -
Refi ll chamber completely full with new cool-
ing oil per Table 1 or reuse the uncontaminated oil. (See parts
list for amount.)
Important! - Do not overfi ll oil!
Overfi lling of motor housing with oil can
create excessive and dangerous hydraulic
pressure which can destroy the pump and
create a hazard. Overfi lling oil voids warranty.
TABLE 1 - COOLING OIL - Dielectric
SUPPLIER
GRADE
BP
Enerpar SE100
Conoco
Pale Paraffi n 22
Mobile
D.T.E. Oil Light
G & G Oil
Circulating 22
Imperial Oil
Voltesso-35
Shell Canada
Transformer-10
Texaco
Diala-Oil-AX
Woco
Premium 100
Caution! - Pressure builds up extremely
fast, increase pressure by “tapping” air
nozzle. Too much pressure will damage
seal. Do Not exceed 10 P.S.I. in motor
housing & 20-25 P.S.I. in seal chamber.
F-1.4) Pressure Test:
Motor Housing -
Before checking the pump for leaks around
the shaft seal, square rings, and cord inlet, the oil level should
be full as described in section F-1.3. Remove pressure valve
(26) from motor housing (1).
Apply pipe sealant to pressure gauge assembly and tighten
into pressure valve hole (See Fig. 2). Pressurize motor
housing to 10 P.S.I. Use a soap solution around the sealed
areas and inspect joints for “air bubbles”. If, after fi ve minutes,
the pressure is still holding constant, and no “bubbles” are
observed, slowly bleed the pressure and remove the gauge
assembly. Replace the Pressure valve using a sealant. If the
pressure does not hold, then the leak must be located.
Seal Chamber -
Remove pipe plug (8) from Bearing Bracket
(4) and check that seal chamber is full of oil. Apply pipe
sealant to pressure gauge assembly and tighten into hole in
bearing bracket (4). Pressurize seal chamber to 20-25 PSI
and check for leaks as outlined above.
F-2) Impeller and Volute Service:
F-2.1) Disassembly and Inspection:
To clean out volute (43) or replace impeller (48), or replace
wear ring (60), on High-Effi ciency pumps, disconnect power,
remove hex nuts (7) and vertically lift motor and seal assembly
from body (43). Clean out body if necessary. Clean and ex-
amine impeller (48), for pitting or wear and replace if required,
inspect gasket (19) and replace if cut or damaged. If the impel-
ler (48) requires replacing, remove cap screw (46) and washer
(45). The impeller is keyed onto the shaft with a square key
(18) and to remove, pull impeller straight off the shaft using a
wheel puller, if required. If the wear ring (60) on High-Effi ciency
pumps require replacing, split the wear ring (60) and remove,
be careful not to damage the volute. Before reinstalling, check
the motor shaft and impeller bore for damage.
F-2.2) Reassembly:
To install wear ring (60) on High-Effi ciency pumps, fi rst apply
retaining compound (42) to the bore of body (43) and then
press wear ring (60) into bore of body (43) until seated. To
install impeller (48), on all models, apply a thin fi lm of oil to
motor shaft and slide impeller straight onto shaft, keeping
keyways lined up. Drive key (18) into keyway. Locate washer
(45), apply thread lock primer (such as Loctite® Primer T) let
set per manufactures’ directions. Apply thread locking com-
pound to cap screw (46) threads, thread cap screw (46) into
shaft and torque to 35 ft. lb. Rotate impeller to check for bind-
ing. Position gasket (19) on volute fl ange and install impeller
and motor housing over studs and onto volute (43). Apply
thread locking compound (38) to threads of each stud (20).
Thread nut (7) onto stud (20) and torque to 24 ft. lb. Check
for free rotation of motor and impeller.
F-3) Motor and Bearing Service
F-3.1) Disassembly and Inspection:
To examine or replace the motor (47) and bearings (2) and
(5), disassemble pump, volute and impeller (as outlined in
paragraph F-2.1) and disassemble seal plate and shaft seal
(as outlined in paragraph F-4.1). Drain oil from motor as out-
lined in paragraph F-1.3.
Position unit upright, using blocks to avoid resting unit on
shaft. After removal of cable and box assembly (49) from
motor housing (1), remove cable lead wires from motor
lead wires and moisture and temperature sensors wires (if
equipped) from control cable by unscrewing connectors (22)
and (32). The wiring connections should be noted to insure
correct connections when reassembling. Remove cap screws
(6) and hex nuts (7).
Содержание BARNES 4DSE-HL Series
Страница 15: ...15 FIGURE 10 4DSE L Pump Series...
Страница 16: ...16 FIGURE 11 4DSE L Pump Series...
Страница 17: ...17 4DSE L Pump Series FIGURE 12...
Страница 21: ...21 4DSE HL High Ef ciency Pump Series FIGURE 13...
Страница 22: ...22 4DSE HL High Ef ciency Pump Series FIGURE 14...
Страница 23: ...23 4DSE HL High Ef ciency Pump Series FIGURE 15...
Страница 27: ...27 NOTE...