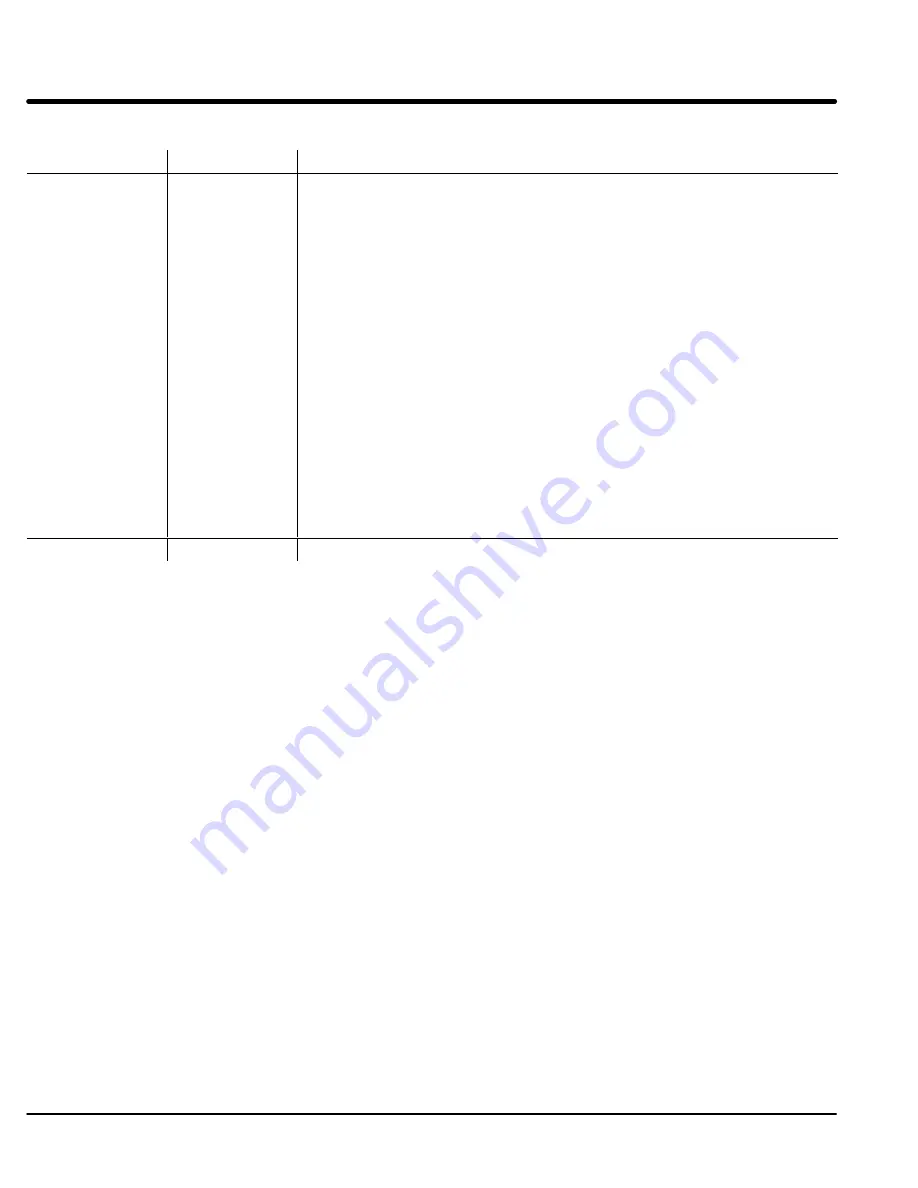
Section 1
General Information
4-24 Programming & Operation
MN722
Table 4-5
Power Output Control Board
Level 2 Parameter Definitions
- Continued
Block Title
Parameter
Description
AUTO TUNING
CALC Presets
CMD Offset Trim
CUR Loop COMP
Stator R1
Flux CUR Setting
Feedback Tests
Slip FREQ Test
SPD CNTRLR
CALC
The Auto Tune procedure is used to automatically measure and calculate certain
parameter values. Dynamic Brake Hardware is required to perform “Slip Freq Test”
and “Spd Cntrlr Calc” autotuning test. Occasionally, the Auto Tune procedure cannot
be run due to various circumstances such as the load cannot be uncoupled from the
motor. The control can be manually tuned by entering the parameter values based on
calculations you have made. Refer to “Manually Tuning the Control” in the
Troubleshooting section of this manual.
Loads operating values into memory. These values are based on information
programmed into the Level 2 Output Limits and Motor Data parameter values.
CALC Presets must be run before Autotuning or manually tuning the drive.
This procedure trims out voltage offsets for the differential analog input at J1-4 and J1-5.
Measures current response to pulses of one half the rated motor current.
Measures the motor stator resistance.
Sets motor magnetizing current by running motor at near rated speed.
Checks the values for Encoder Lines per revolution and encoder alignment parameters
while the motor is running at near full rated speed. Test will automatically switch
encoder phasing to match motor rotational direction.
Calculates motor Slip Frequency during repeated motor accelerations.
Should be performed with the load coupled to the motor shaft. Sets the motor current to
acceleration ratio, Speed INT gain and Speed PROP gain values. If done under no
load, the Integral gain will be too large for high inertia loads if the PK Current Limit is
set too low. If the control is too responsive when the drive is loaded, adjust the PK
Current Limit parameter to a greater value and repeat this test.
LEVEL 1 BLOCK
ENTERS LEVEL 1 MENU
Содержание 22H series
Страница 1: ...SERIES 22H Line Regen AC Flux Vector Control Installation Operating Manual 9 97 MN722 VECTOR DRIVE...
Страница 5: ...Section 1 General Information iv Table of Contents MN722...
Страница 105: ...Section 1 General Information 5 22 Troubleshooting MN722...
Страница 109: ...Section 1 General Information 6 4 Manual Tuning the Series 22H Control MN722...
Страница 137: ...Section 1 General Information A 8 Appendix A MN722...
Страница 138: ...Appendix B Appendix B 1 MN722...