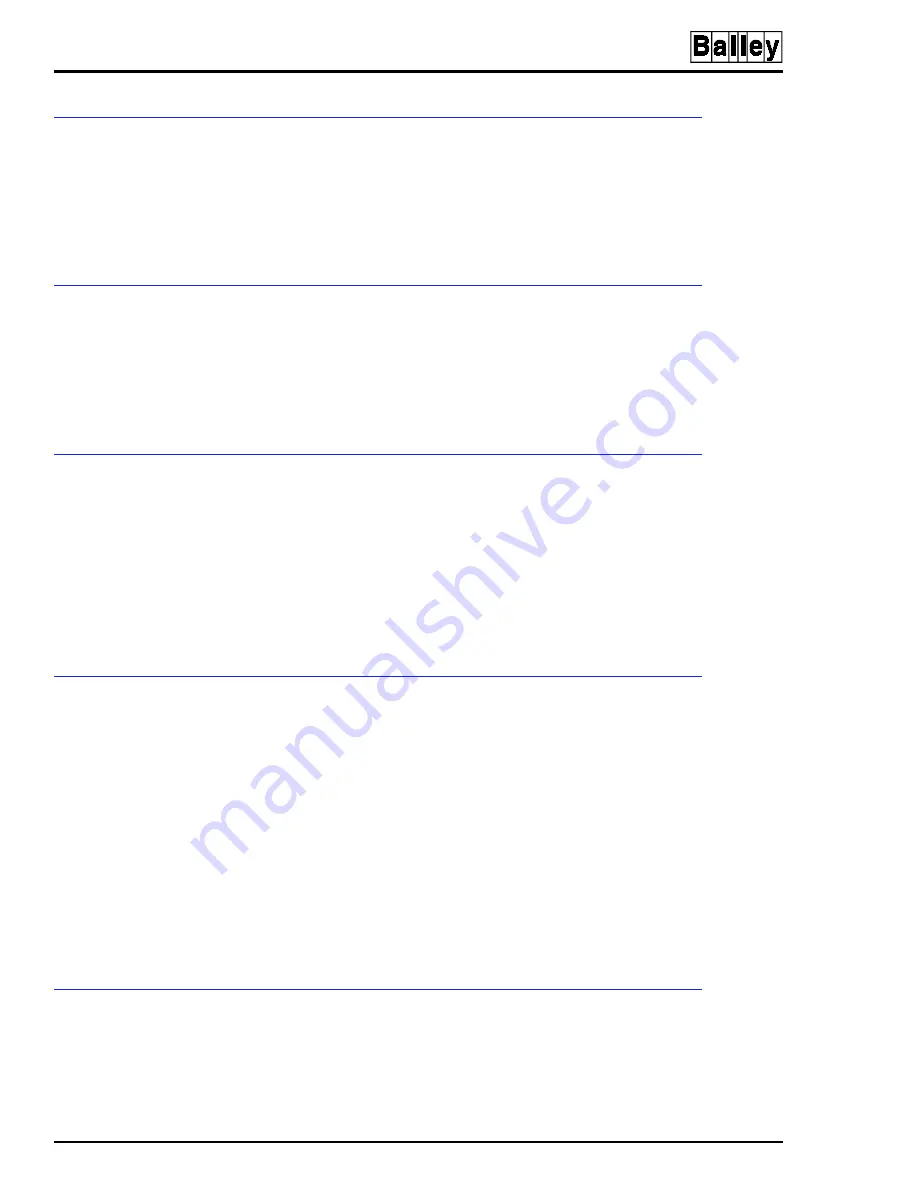
FUNCTION CODE CONFIGURATION
FUNCTION CODES
4 - 2
WBPEEUI240759A0
®
Analog Output Subscriber
The analog output subscriber function code (FC 187) sends a
group of analog outputs to an Ethernet PLC device. Each ana-
log output subscriber can handle up to eight analog outputs.
The analog output subscriber function code has one output
which gives the quality of the communication between the
EDI module and the MFP module.
Digital Output Subscriber
The digital output subscriber function code (FC 188) sends a
group of digital outputs to an Ethernet PLC device. Each digi-
tal output subscriber can handle up to eight digital outputs.
The digital output subscriber function code has one output
which gives the quality of the communication between the
EDI module and the MFP module.
PLC Support
Function code specifications determine the EDI module opera-
tion. The definition of these specifications varies slightly
depending on the family of PLC being interfaced. Currently, the
EDI module interfaces Allen Bradley controllers and Triconex
Systems controllers. Refer to the following appendices for func-
tion code specifications:
•
– Allen Bradley PLC-5E and higher.
•
– Triconex Systems Tricon V6 PLC and higher.
Configuration
The function codes can be added to the MFP module configura-
tion in the same way as other function codes. Refer to the
Function Code Application Manual
,
Multifunction Proces-
sor Module
, and
Module Configuration Tools (WCAD)
instructions for an explanation of function codes and module
configuration (Table
Because the EDI module is dependent on the MFP module, an
EDI module must only be driven by one MFP module. One MFP
module can drive multiple EDI modules however.
On-line configuration cannot be used to add points to an EDI
module that has already been configured by the MFP module.
A new EDI module can be added on-line however.
PLC Performance
NOTE: All performance is based on the EDI module and PLCs oper-
ating on a dedicated Ethernet network.