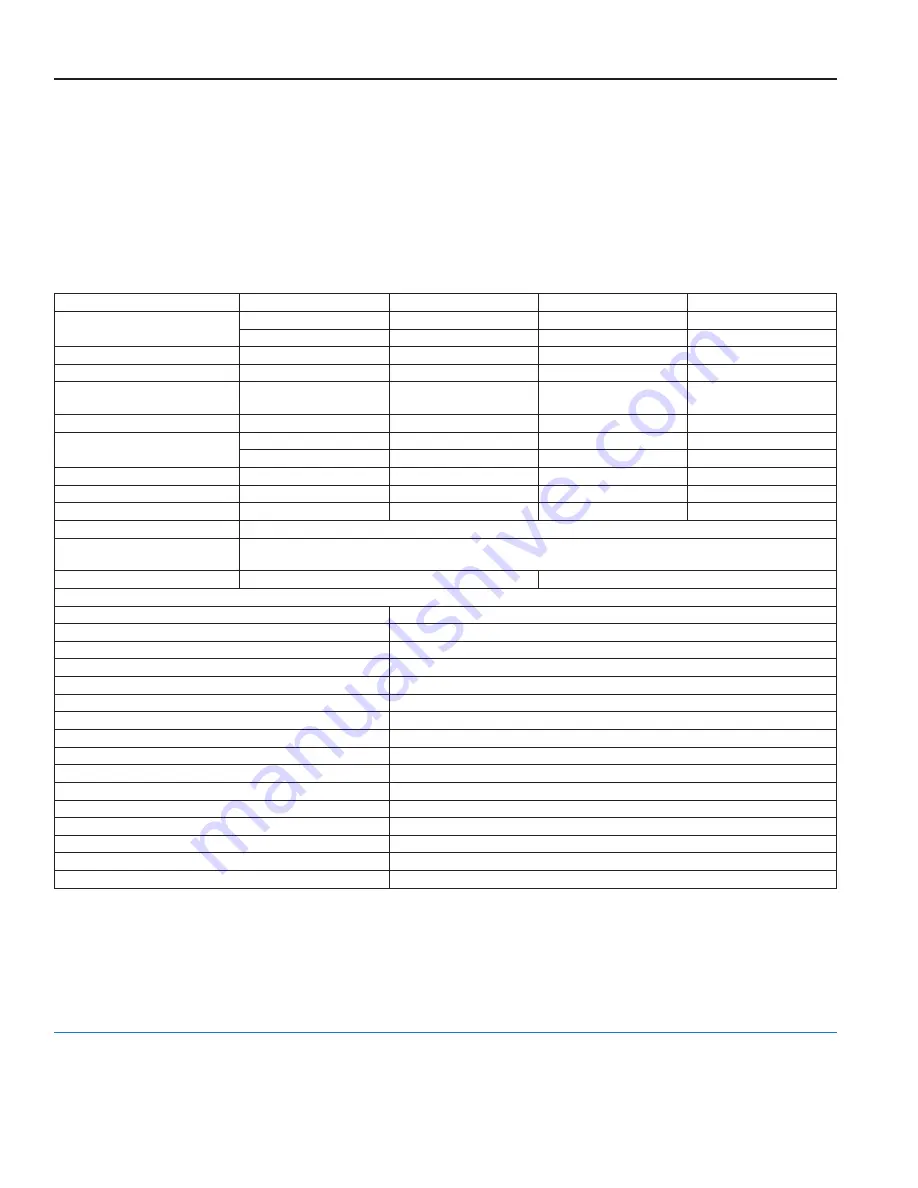
Reinstalling the Cover Assembly
Badger
Meter recommends that a new O-ring be used after each teardown and reassembly of the cover assembly To assure a
tight seal, make sure the O-ring is positioned correctly on the housing and that the O-ring and cover assembly are clean and
free of dirt or residual traces of old O-ring material If necessary, use silicone grease to help retain the O-ring and to serve as a
lubricant in reassembling it to the housing
Cover bolts should be tightened in a crisscross pattern similar to Turbo head bolts Torque 2" and 3" cover assembly bolts to
16…18 ft-lb Torque the bolts for the 4" and 6" cover assemblies to 35…40 ft-lb
SPECIFICATIONS
Compound Series Model
2" (50 mm)
3" (80 mm)
4" (100 mm)
6" (150 mm)
Meter Flanges, Class 150
2" elliptical or round
3" round
4" round
6" round
(50 mm)
(80 mm)
(100 mm)
(150 mm)
Typical Operating Range
0 5…200 gpm
0 5…450 gpm
0 75…1000 gpm
0 75…2000 gpm
(100% ± 1.5%)
(0 1…45 m
3
/h)
(0 1…102 m
3
/h)
(0 17…227 m
3
/h)
(0 17…454 4 m
3
/h)
Low Flow Registration
(95% minimum)
0 25 gpm (0 06 m
3
/h)
0 25 gpm (0 06 m
3
/h)
0 375 gpm (0 09 m
3
/h)
0 375 gpm (0 09 m
3
/h)
Maximum Continuous Flow
170 gpm (38 3 m
3
/h)
400 gpm (90 3 m
3
/h)
800 gpm (181 6 m
3
/h)
1500 gpm (340 5 m
3
/h)
Pressure Loss at Maximum
Continuous Flow
5 4 psi at 170 gpm
6 0 psi at 400 gpm
11 0 psi at 800 gpm
9 3 psi at 1500 gpm
(0 38 bar at 38 3 m
3
/h)
(0 41 bar at 90 3 m
3
/h)
(0 75 bar at 181 6 m
3
/h)
(0 64 bar at 340 5 m
3
/h)
Crossover Flow Rate, Typical
12 gpm
12 gpm
20 gpm
30 gpm
Pressure Loss at Crossover
3 5 psi (0 24 bar)
4 0 psi (0 28 bar)
4 0 psi (0 28 bar)
5 0 psi (0 35 bar)
Minimum Crossover Accuracy
97%
97%
97%
95%
Maximum Operating Pressure
150 psi (10 bar)
Maximum Operating
Temperature
105° F (41° C)
Test Plug
1-1/2"
2"
Materials
Meter Housing & Cover
Lead-free bronze alloy
Turbo Cast Head
Lead-free bronze alloy
Nose Cone & Straightening Vanes
Thermoplastic
Rotor
Thermoplastic
Rotor Radial Bearings
Lubricated thermoplastic
Rotor Thrust Bearing
Sapphire jewels
Rotor Bearing Pivots
Passivated 316 stainless steel
Calibration Mechanism
Stainless steel & thermoplastic
Measuring Chamber & Disc
Thermoplastic
High Flow Valve
Stainless steel & thermoplastic
Magnets
Ceramic
Register Lens
Glass
Register Housing & Cover
Thermoplastic or bronze
Trim
Stainless steel
Drain Plug (3/4")
Stainless steel or lead-free bronze alloy
Test Plug
Stainless steel or lead-free bronze alloy
Recordall® Compound Series Meter, Lead-Free Bronze Alloy, Sizes 2", 3", 4" & 6"
www.badgermeter.com
Making Water Visible, GALAXY, ORION and Recordall are registered trademarks of Badger Meter, Inc Other trademarks appearing in this document are the property of their respec-
tive entities Due to continuous research, product improvements and enhancements, Badger Meter reserves the right to change product or system specifications without notice,
except to the extent an outstanding contractual obligation exists © 2016 Badger Meter, Inc All rights reserved
Making Water Visible®
The Americas | Badger Meter | 4545 West Brown Deer Rd | PO Box 245036 | Milwaukee, WI 53224-9536 | 800-876-3837 | 414-355-0400
México | Badger Meter de las Americas, S A de C V | Pedro Luis Ogazón N°32 | Esq Angelina N°24 | Colonia Guadalupe Inn | CP 01050 | México, DF | México | +52-55-5662-0882
Europe, Middle East and Africa | Badger Meter Europa GmbH | Nurtinger Str 76 | 72639 Neuffen | Germany | +49-7025-9208-0
Europe, Middle East Branch Office | Badger Meter Europe | PO Box 341442 | Dubai Silicon Oasis, Head Quarter Building, Wing C, Office #C209 | Dubai / UAE | +971-4-371 2503
Czech Republic | Badger Meter Czech Republic s r o | Maříkova 2082/26 | 621 00 Brno, Czech Republic | +420-5-41420411
Slovakia | Badger Meter Slovakia s r o | Racianska 109/B | 831 02 Bratislava, Slovakia | +421-2-44 63 83 01
Asia Pacific | Badger Meter | 80 Marine Parade Rd | 21-06 Parkway Parade | Singapore 449269 | +65-63464836
China | Badger Meter | 7-1202 | 99 Hangzhong Road | Minhang District | Shanghai | China 201101 | +86-21-5763 5412
Switzerland I Badger Meter Swiss AG I Mittelholzerstrasse 8 I 3006 Bern I Switzerland I +41-31-932 01 11
Legacy Document Number: RCS-IOM-1