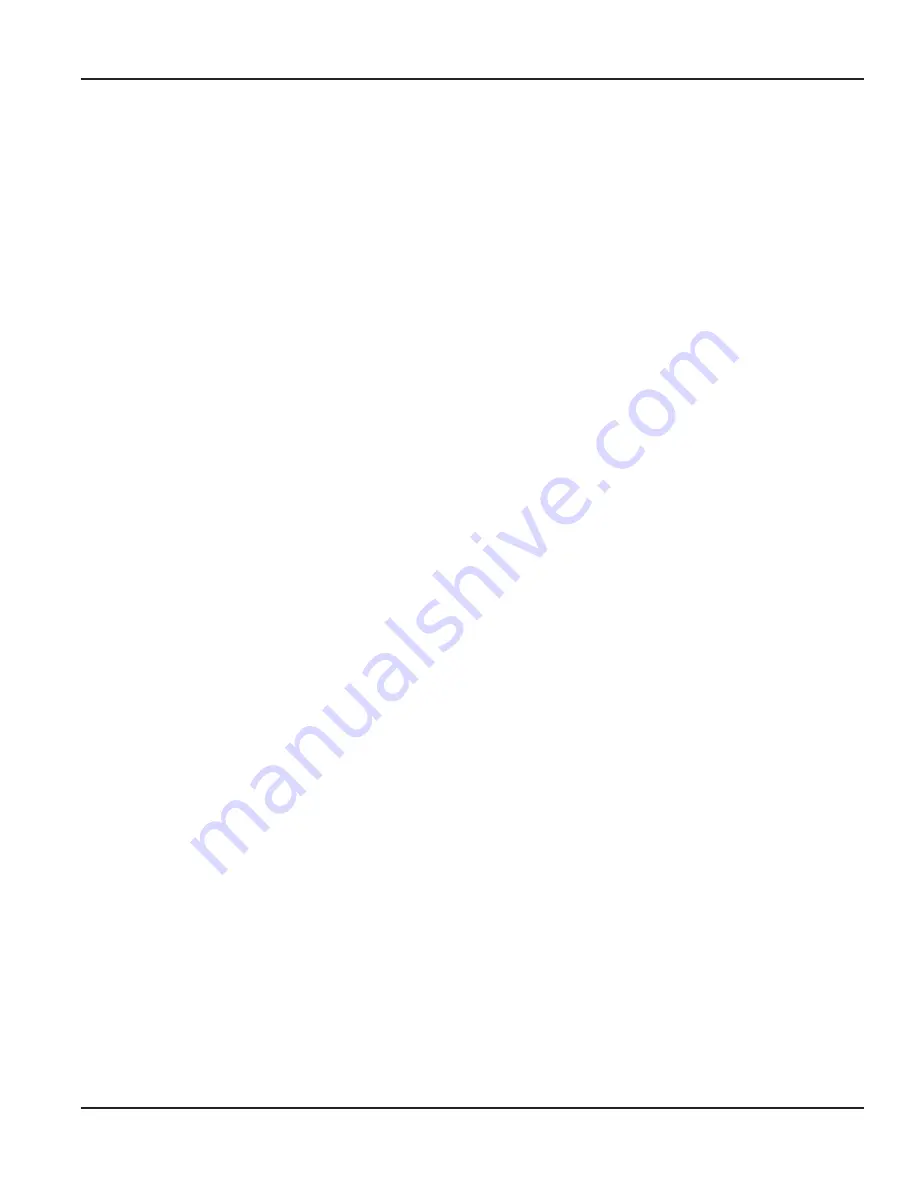
6 Press the nose cone assembly fully into the cage insert and turn it counter-clockwise, catching the calibration linkage
in the slot
7 Check to see that the rotor spins freely If it does not, remove the nose cone assembly and repeat the procedure
8 Install and tighten the nose cone assembly setscrew
9 Holding the cover plate in one hand, align the thermoplastic cage bayonet-like tabs with the slots in the cover plate
(2", 3" and 4" only)
10 Rotate the element clockwise until the cage setscrew hole is aligned Install and tighten the cage setscrews (quantity of
1 for 2", 3" and 4" meters, a quantity 4 for the 6" meter)
Removing the Rear Nose Cone
Rear nose cone removal requires transmission shaft removal
1 Remove the strap over the gear (2", 3", and 4" only)
2 Lift the gear off the shaft The shaft has a flat spot that aligns with the D-shaped bore in the gear
3 Remove the nose cone set screw
4 Remove the protection tube by carefully pressing (with flat surface of blade screwdriver) on the bottom of the tube
located inside the rear nose cone
5 Press to release the detent lock, approximately 1/4" vertical travel, then lift the tube out from the top of the cage insert
6 Lift the transmission shaft assembly up and out of the bottom bearing, then slide shaft downward and diagonally out
(towards you) to remove it from the nose cone/cage assembly
7 Holding cage firmly with one hand, rotate the nose cone clockwise with other hand, then carefully lift it off the cage
To reinstall the rear nose cone, follow this procedure in reverse See
“Inspecting the Rotor and Bearings” on page 16
for
instructions on reassembling the components
Reinstalling the High Flow Turbo Meter Head Assembly
• Use a new O-ring after each teardown and reassembly Apply a light coat of silicone grease to the O-ring to aid
in assembly
• To provide a tight seal, make sure the surfaces of the housing and meter head are clean and free of any old O-ring material
• Be careful not to force the measuring element insert into the meter housing If you experience any binding, do not force
the element into the housing Remove the element from the housing and properly reinsert the unit
NOTE:
N
Head bolts should be tightened similar to that on car tire First insert the bolts and snug-fit each Then, using a
crisscross pattern, tighten the bolts down Following this pattern, the meter head will not turn and the rotor will
remain perpendicular to the flow, eliminating any potential flow distortion Tighten the head bolts to 10…11 ft-lb for
the 2" size, and 35…40 ft-lb for the 3", 4" and 6" sizes
Servicing Parts and Assemblies
June 2016
RCS-UM-00076-EN-04
Page 17