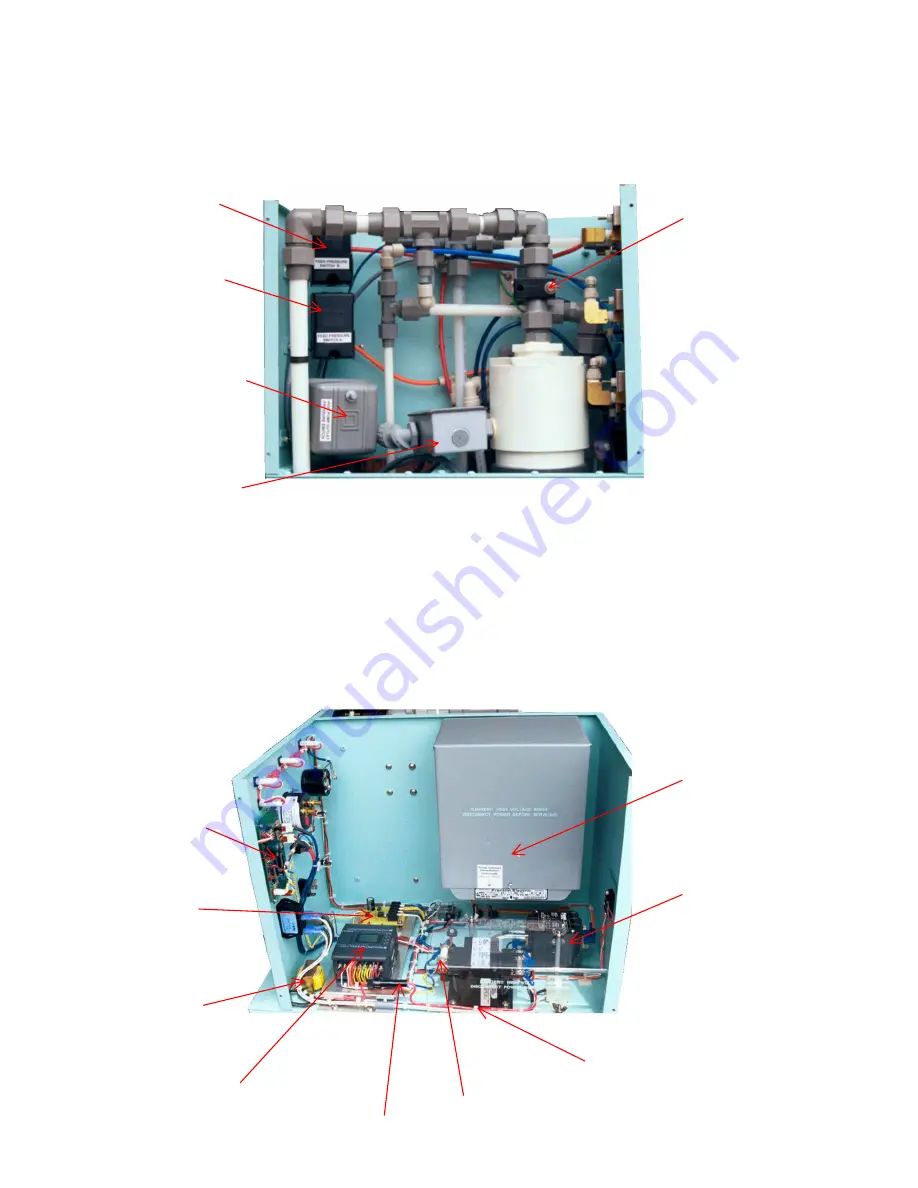
G01
SPD Owner's Manual
5
Figure 2
LEFT VIEW INSIDE CONTROL COVER
Figure 3
Electrical Controls
Feed Pressure
Switch A
Feed Pressure
Switch B
Pump Outlet
Pressure Switch
Pump Wiring Box
Pump Torque Block
Franklin Pump
Control Box
Control Transformer
Main Control Fuse
In Line Fuse
Keyence PLC
Contactor
Conductivity
Transformer
Auxiliary
Circuit Board
Conductivity
Monitor
Содержание SPD2H
Страница 2: ......
Страница 11: ...G01 SPD Owner s Manual 9 FIGURE 5 ...
Страница 22: ...G01 SPD Owner s Manual 20 FIGURE 7 ...
Страница 33: ...G01 SPD Owner s Manual 31 ...
Страница 35: ...G01 SPD Owner s Manual 33 Appendix 1 Keyence Ladder Program ...
Страница 36: ...G01 SPD Owner s Manual 34 ...
Страница 37: ...G01 SPD Owner s Manual 35 ...
Страница 38: ...G01 SPD Owner s Manual 36 ...