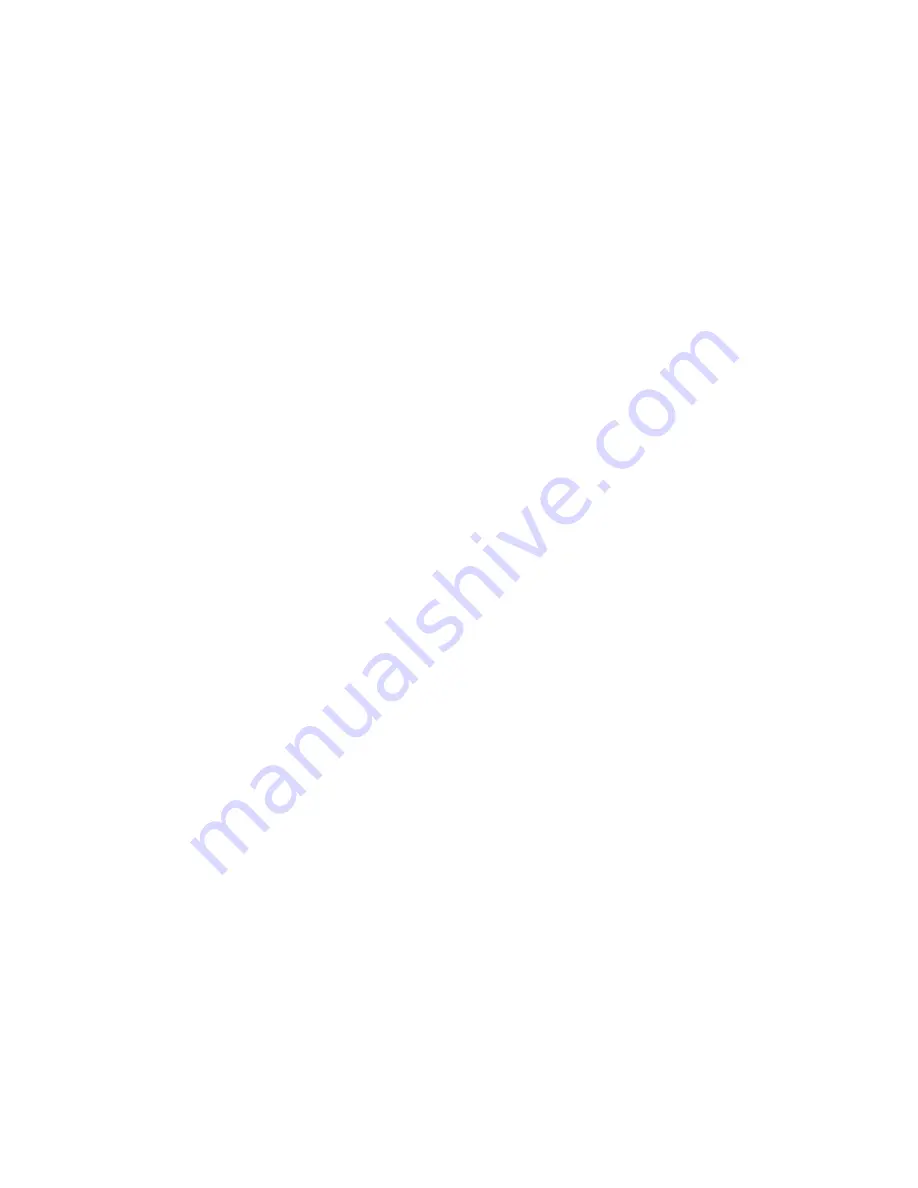
G01
SPD Owner’s Manual
18
cool down for several minutes, turn all the way off and then on again to restart.
The Franklin pump electrical power box has an overcurrent thermal sensor that will trip if the pump
motor draws excessive current. The button is on the bottom of the box. The overload button is
accessible after removing the control panel cover, see Figure 3. After allowing several minutes for cool
down, press the red button to reset.
The control fuse will open if there is a short in the low voltage control circuitry. The fuse must be
replaced to resume operation.
The occurrence of any of these shutdowns indicates something was wrong. Resetting the protective
device will likely merely allow the shutdown to repeat. So service is indicated.
MONITORING SYSTEM OPERATION
A log of pertinent operating conditions should be kept so the condition of the RO system and especially
the membranes is tracked. Doing so reveals trends that help insure preventative maintenance is
performed rather than emergency service. It also provides a record that indicates the system is
performing as expected.
ELECTRICAL CONTROLS
Description:
Refer to the enclosed electrical schematic, Figure 7. The incoming electrical power all
passes through the two pole circuit breaker/power switch. From there power is supplied to the pump
contactor (R1) and to the control transformer. A primary tap on the transformer supplies 115 volts AC to
the conductivity monitor through an inline fuse. The secondary side of the transformer provides 24 volts
AC.
An auxiliary circuit board rectifies and regulates the 24 volts for use by a Keyence PLC (programmable
logic controller). This board also contains an opto-isolator for accepting the alarm output voltage from
the conductivity monitor.
The Keyence PLC runs a program written for the SPD system. The program can be changed on a
personal computer with the Keyence software loaded. A cable connection allows transfer of the
program to the Keyence. The ladder logic program and inputs and outputs used by the Keyence are in
Appendix A.
The Keyence outputs operate the solenoid valves, lights, alarm and R1 with 24 VAC. To achieve
maximum life from the relay contacts in the Keyence, varistors are placed around all coils.
If the Keyence PLC were to fail, emergency operation could be achieved by jumpering the outputs on
the PLC that control the feed solenoid and R1. See troubleshooting.
Relay contactor R1 applies power to the Franklin Control Box. This box contains a thermally actuated
overload, a starting capacitor, a running capacitor, and a potential relay. At first power is applied to both
the start and the run windings. The coil of the potential relay responds to the voltage on the run winding
and opens up the start winding when this voltage is high enough. Some current in the start winding is
Содержание SPD2H
Страница 2: ......
Страница 11: ...G01 SPD Owner s Manual 9 FIGURE 5 ...
Страница 22: ...G01 SPD Owner s Manual 20 FIGURE 7 ...
Страница 33: ...G01 SPD Owner s Manual 31 ...
Страница 35: ...G01 SPD Owner s Manual 33 Appendix 1 Keyence Ladder Program ...
Страница 36: ...G01 SPD Owner s Manual 34 ...
Страница 37: ...G01 SPD Owner s Manual 35 ...
Страница 38: ...G01 SPD Owner s Manual 36 ...